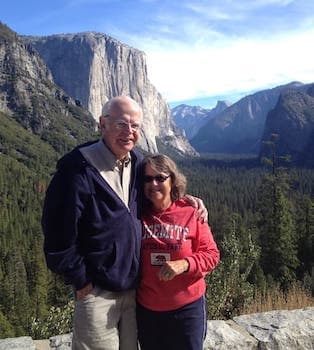
Curated with aloha by
Ted Mooney, P.E. RET
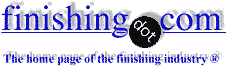
The authoritative public forum
for Metal Finishing 1989-2025
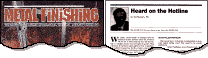
-----
More Corrosion Problems with Structural Stainless Steel?
2000
We use structural 304 and 304L stainless steel on the systems we manufacture. All though I can't prove this with fact it seems we have more material that comes in with corrosion problems versus five or more years ago. The worst is material that has been slit or sheared. In some cases welded tube, square and rectangular. I have been keeping track of the alloy chemistry for about 12 months now, with very few exceptions the chrome and nickel content is at the minimum ASTM spec. With the exceptions the chrome 19%, and nickel 9%, the corrosion problems were minimal. This material comes from South Africa. I am speculating the price of chrome/nickel has driven the mills to produce materials that are lower in alloying elements while still maintaining ASTM specifications. If anyone out there has similar experiences with iron contamination/corrosion please respond. If any one can explain my theory on more corrosion problems this would also be GREATLY APPRECIATED.
Additional item: We use to get by with "bead blasting", now we have to pickle and passivate to remain rust free from fresh water exposure. I realize this is a loaded question with hundreds of variables here, to eliminate a bunch of them, we do know how to handle the material once it is delivered here.
Regards, Bradford
Bradford Maas- Northfield, Minnesota
Two major factors will be affecting the corrosion resistance of the stainless steel that you are using. One is composition, as you have mentioned. I doubt that minor variations in Cr and Ni will be noticeable in structural fresh water applications. Mills with good composition control have been holding Cr and Ni contents to the minimum levels for a lot more than just the past 5 years. The second factor is the surface condition. Composition, contamination, and finish will be a factor. Iron contamination is a major factor, but other contamination of the surface will also diminish corrosion resistance.
One thing that you may want to watch out for in material from second and third tier mills is variability in the composition from the mill test report. I have seen "certified" material that did not meet the composition requirements. Another is material that has not been properly annealed. These conditions will not be obvious (usually)unless you are testing the incoming material.
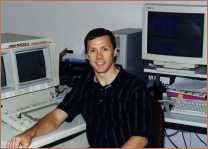
Larry Hanke
Minneapolis, Minnesota
2000
Corrosion problems with stainless steel prior to fabrication is a common lament. Little thought is given to the proper handling and storage of the material which leads to it coming in contact with mild steel storage racks, brake dust from fork lifts, other grinding and finishing operations, etc. There is a fair amount of "bad" stainless out there, but usually it is a misunderstanding of the passive layer and how it is maintained that is the greater area of concern.
Contact me if you would like assistance in doing a "self survey" of your operations or a survey of your suppliers operations to pinpoint the exact cause of your stainless corrosion problems.
Dan Weaver- Toccoa, Georgia
2000
Bradford,
The issues raised are classic. While the mill capacity to sharpen the knife is understandable the real problem resides with the approach to fabrication taken by many work shops.
It is my experience that most people make the mistake of assuming that the stainless steel is inert. That is, it does not react with its environment. Nothing could be further from the truth. I run a high quality manufacturing operation for the Pharmaceutical and Food Industry in Australia. We are continually being brought sub-standard product made by big name manufacturers for repair evaluation. These manufacturers should know better than trying to pass off an apparently glossy SS surface as corrosion resistant.
The biggest problem faced by the SS industry as a whole is sloppy manufacture by unskilled individuals who think that just because they can purchase a TIG or MIG welder they can with minimal education weld stainless steel. When you couple this with the grinding of welds using ferritic abrasives in a dusty environment, and lack of correct final finishing such as passivation with chemistry that is in appropriate for the scale levels generated you have the correct conditions for RAPID corrosion of Stainless Steel. A cursory look at EMF/Free Energy should be enough to illustrate this.
Remember it is always better to pay a little more and get want you want than pay less and be miserable. This goes for buying anything. Cheers
Hamish Hunt- Melborne, Australia
2000
Our experience with 304 and 304L shows that even with the lower carbon content and higher Chromium content, the service will "rouge" or rust. We suggest using one of the several methods recommended in ASTM A967. As a high purity cleaning company doing passivation work in the Pharmaceutical and Semi Conductor industries, we have developed a Citric based chelating process that shows extremely high CRFe ratios and enhanced Cr Fe oxide rations. These enhanced passive layers are the way you increase rust resistance. Passivation is the key!
CARL W. VERHEYEN- Downey, California
2000
Hi
I understand the problems that you write about and was wanting to ask if cathodic corrosion prevention can help you in any way.
- Ayrshire, U.K.
December 1, 2008
Q, A, or Comment on THIS thread -or- Start a NEW Thread