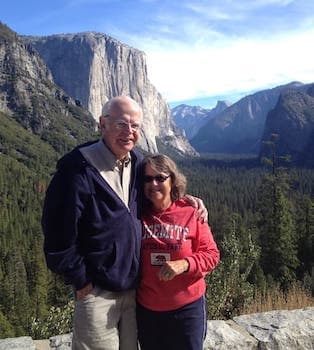
Curated with aloha by
Ted Mooney, P.E. RET
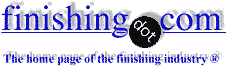
The authoritative public forum
for Metal Finishing 1989-2025
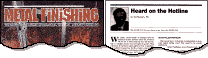
-----
Cadmium plating is blistering -- problems & solutions
Quickstart (no readers left behind):
Cadmium plating is no longer popular because cadmium is a biocumulative poison similar in effect to mercury and lead. But no other material offers ALL of the benefits of cadmium plating, so there are still legacy aerospace applications.
'Blistering' is a defect exactly like it sounds, with the plating pulling away from the substrate in small or large blisters resembling human blisters.
Q. Good day dears, I had a problem that my Cd plating in high current density becomes blistered while low current density is smooth and sometimes adherent not always. Also, my part has an external surface which really cannot attract the ions and be plated even in the first 10 mins, after 10 mins it attracts the ions partially but not plated fully. This part is a mass production part which means we have 5,000 like it.
Omar Ibrahim- Minnesota
April 11, 2025
Ed. note: Please send a pic to mooney@finishing.com for posting here. Sorry, we don't undertand "external surface which really cannot attract the ions"
⇩ Related postings, oldest first ⇩
Q. We are leading connector manufacturing company in India. My customer are demanding checking of cadmium plated parts under 10 x magnification. After plating we are able to see micro blister under 4X. But when subjected to 10X small micro blister observed and this will be rejected at customer end. I want to know any correct specification for checking cadmium plated parts.
KAMLESH M.BHATT.DEPUTY MANAGER - PUNE, MAHARASTRA, India
2007
![]() |
A. The correct specification is whatever the customer puts in the contract or the purchase order. - Navarre, Florida A. If you are leading the way who is going to give you advice? What is typical when inspecting this? You have to determine whether or not your process can meet his expectations. If you can't you need to improve your system to meet his demands or he needs to go to a different supplier. That's what competition is all about. ![]() Sheldon Taylor supply chain electronics Wake Forest, North Carolina |
Q. WE ARE PLATING CADMIUM PLATING OVER ALUMINIUM AND ALUMINIUM DIE CASTING USING ELECTROLESS AS UNDERCOAT. WE ARE USING 6061 AND 7075 ALUMINIUM MATERIAL. 6061 MATERIAL COMES FOR PLATING AS EXTRUSION . wE ARE FACING PROBLEM OF BLISTERS AFTER OVEN TEST. BLISTER WHAT WE OBSERVE IS A PIN HOLE SIZE. WE HAVE NOT OBSERVE BLISTER BIGGER IN SIZE. WE HAVE TESTED MATERIAL FOR POROSITY AND MICROPOROSITY OBSERVED WITH THE MATERIAL.cAN YOU PUT YOUR SUGGESTIONS ON THIS WHETHER POROSITY WILL LEAD TO BLISTERS AND HOW TO AVOID?
OUR CLEANING CYCLE FOR COMPONENT IS DEGREASING (TCE), SOAK CLEAN,RINSE, DESMUTTING (HNO3 95% + 5 %HF ) +RINSE.ZINCATING( CMP-ALBOND DIP),RISE,80% HNO3 ( STRIP),RINSE, ZINCATING,RINSE, ELECTROLESS NICKEL 15 MIN. MID PHOS, RINSE, CADMIUM PLATING 40 MIN. RINSE, O.5 % HNO3,O.G. PASSIVATION, RINSE,RINSE, DRY.
THANKS,
KAMLESH BHATT [returning]
PLATING SHOP - PUNE, MAHARASTRA, INDIA
A. Your pretreatment is not adequate for treating 7000 series aluminum.
You also may check if your EN is not stressed.This may also a cause of blister problems , even when you've done a good pre-treatment.
I believe your local electroplating supplier can supply the right process for you.
Bnei Berak, Israel
Cadmium Plating on Stainless Steel is Blistering
Q. Can you suggest plating process for cadmium plating over 304 stainless steel. it should withstand for 1 hr. with 150 degree after plating.
At present we are plating with following sequence.
DEGREASING/ANODIC CLEANING/RINSE/HCL DIP 10 MIN/NICKEL PLATING/RINSE/CADMIUM PLATING/0.5% HNO3/OLIVE GREEN PASSIVATION/DRY/OVEN TEST.
OBSERVATION: No consistency 20 to 30% blister before oven after oven 50% blister.
Any heat treatment required before plating?
Thanks,
plating manager - Pune, Maharastra, India
April 17, 2009
A. Hi, Kamlesh. You can't just plate any old nickel onto stainless steel -- it needs to be a proper Wood's Nickel Strike to activate the stainless steel. Good luck.
Regards,
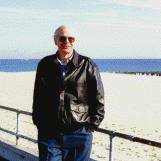
Ted Mooney, P.E.
Striving to live Aloha
finishing.com - Pine Beach, New Jersey
A. Also on Ted's answer, the part needs to be properly cleaned before the activation/strike. Then the rack needs to move with little delay thru the rinses into the cad tank, or the nickel will passivate -- yielding blisters, or worse, peeling plate.
James Watts- Navarre, Florida
Q. Dear Ted Mooney,
Thanks for suggestion.
Our problem of plating cadmium on stainless steel is solved by introducing Wood's Nickel strike bath. We are using following cleaning cycle.
-Degreasing / Electroclean cathodic /Rinse
-Proprietary cleaning ( NITRIC + HF ) 8 MIN
-Woods bath 2 min 3-4 volt /rinse /cadmium
-Plating /rinse/0.5 % HNO3 /O.G.Passivation
-Dry/oven test 150 degree 1 hr.
-
-Result : 100 % o.k.
I want some cleaning information for stainless steel; at present I am using above proprietary but it is costly. Can you please suggest me for the same.
Thanks
sometimes on
AbeBooks or Amazon
(affil links)
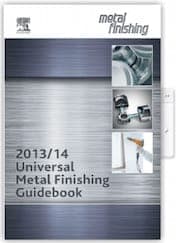
free pdf is currently available from academia.edu
- Pune, Maharastra, INDIA
A. Hi Kamlesh. Here in the USA proprietaries are even more expensive than in India, but virtually everyone uses them anyway. Moving away from proprietaries discards decades of progress, and abandons a great source of local help -- but you can pretty easily find some old technical journals, guidebooks, and conference proceedings from the 1950's. A copy of the Metal Finishing Guidebook from those days will probably include some formulations.
If you want to formulate your own cleaners, remember that they must saponify, wet & emulsify, deflocculate, chelate or sequester, buffer, and inhibit -- it's not easy 🙂
Regards,
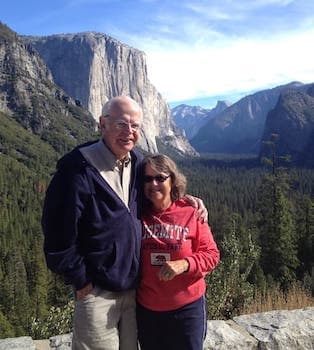
Ted Mooney, P.E. RET
Striving to live Aloha
finishing.com - Pine Beach, New Jersey
Q. We are experiencing small microblisters mainly around the threaded area at the end of a threaded shank. the shank is approx. 1/2" to 5/8" diameter. It doesn't do this all the time, maybe 10-20% of the total.
What would be some of the things to look for in correcting this problem?
thanks
Sherrill
machining and plating business - Monroe, North Carolina, USA
December 2, 2010
A. Medium size blisters are frequently the cause of the part not being clean. This might be because of the cutting fluid burning in that area and requires more aggressive cleaning. It is somewhat possible that caustic or acid is leaking out of the hole during plating. Correct this by better rinsing, possibly even water jet cleaning.
For very tiny blister, normally on 44xx series steel, it is sometimes caused by excessive cleaning or activation steps.
I know that that statement sounds weird, but it is a fact that I learned the hard way.
- Navarre, Florida
Clear cad over EN blisters at masked holes
Q. Aluminum alloy 6061 T6 shell is experiencing blistering at the thread hole edge that was...
1) masked prior to plating.
2) plating consists of clear cadmium per SAE-AMS-P-416, Type II, .0003" to .0005" thick
3) over electroless nickel per SAE-AMSC26074, Class 4, .0005" to .0008" thick
4) shell is then subject to 151° C heat cure of ink marking for two hours.
Blistering causes plating to flake off when pierced.
Does the masked thread hole expose plating layers after the masking is removed?
If so, do the exposed layers of plating contribute to the blistering effect?
Will heat treatment (temperature/time) of the marked shell violate any SAE-AMS-P-416 or SAE-AMSC26074 requirements ? If so, please state paragraph where requirements will be violated.
Quality Assurance - Irvine, California, USA
January 31, 2012
by R. A. Farrara
on Amazon
"Replacement for Cadmium Plating and Hexavalent Chromium on Fasteners and Electrical Connectors"
by I. C. Handsy
on Amazon
(affil links)
A. Most surely your problem comes from the masking tightness or effectiveness. Chemical plating solutions almost always interfere with the next one. That is why rinsing (and proper masking) are so important.
G. Marrufo
Monterrey, NL, Mexico
A. You have two possibilities.
1: the masking is not solution-tight and thermal differences of solutions might be sucking in some of a colder solution.
I would try putting it in a hot rinse tank for two minutes, followed by two minutes in a clean cold rinse tank. Then plate as normal.
The second possibility is that you are not rinsing adequately. This normally means using considerable agitation in each rinse tank.
Surface tension tends to hold a film of solution on the lower side of the masking.
Threaded holes are not easy to mask. If they are blind holes, I normally used neoprene plugs. Insert with twisting and pressure.If they are thru holes, you can not beat proper silicone pull plugs.
- Navarre, Florida
February 7, 2012
Cadmium plating on SS304
Q. Please help me to find out ways for having Type 2 cadmium plating on SS304 wire coils. Coil wire dia is just 2 mm.
Saurabh KumarMechanical Engineer - Hyderabad, India
December 2, 2015
Q, A, or Comment on THIS thread -or- Start a NEW Thread