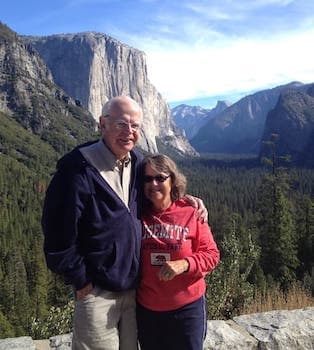
Curated with aloha by
Ted Mooney, P.E. RET
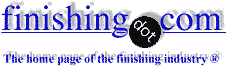
The authoritative public forum
for Metal Finishing 1989-2025
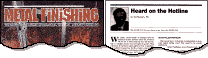
-----
Electroless Nickel plating degrades surface finish
We have a cast V process aluminum plate about 12 inches in diameter. The machine shop cuts the critical surfaces with a diamond cutter end mill to a finish of about 3 - 10 µinch before plating. For the most part, the parts that come back are in the 13 - 24 µinch range. The cast plate is made from A356 T51 and the finish is called out as Electroless Nickel with 15% Teflon .0003 to .0005" thick.
Do the different grades of phosphorous affect the final surface finish? Is the problem with the plater and the way they hang the part
(horizontal vs vertical)? What factors would cause the surface finish to degrade - prep? plating bath? something else.
Thanks for your help.
Gary
end user - Rochester, New York
April 17, 2009
The Teflon particles will give a little bit of a false reading if you are using a profilometer. It is also possible that the plater is staying in a caustic etch a tiny bit too long. There is no way for any of us to do anything but guess at the reason as there are so many places for it to have a small but cumulative effect. It could even go back to the machinist causing a bit of smearing which the plater would remove in a normal process.
In short, there is no way to definitely tell with out being there and running a bunch of tests.
- Navarre, Florida
April 21, 2009
May 4, 2009
You may want to check the part's roughness as it comes out after the cleaning step and right after the preparation cycle
(zincate) just before the final EN plating.
Running some samples on a more conventional metal (like steel) or comparing your platers performance on other smooth substrates might give you the perspective James was telling you about.
Monterrey, NL, Mexico

Q, A, or Comment on THIS thread -or- Start a NEW Thread