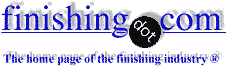
-----
Premature white corrosion on trivalent plated hydraulic tubing
I am a supplier quality engineer for a very large manufacturer of construction equipment. One of our plants that uses trivalent plated steel hydraulic tubing for hard plumbed lines in the vehicles is reporting premature white corrosion on these lines. This tubing is cut to length, goes through an alkaline zinc plating process, clear trivalent chromate and then has a sealer applied. Parts are later cold formed in a CNC bending machine. All our tests indicate that the thickness of the plating meets or exceeds specifications. Parts that have been processed through the CNC bending process consistently fail in salt fog testing for white corrosion in less than 24 hours. However, red corrosion does not form before 144 hours. We also tested tubes that were plated in the same manner but not put through the bender. These pass the white corrosion requirement. This leads me to believe that bending the tubing after plating either compromises the sealer or the plating. Our supplier agrees but is not able to pinpoint the specific variables involved so we can attempt to improve the process. I am looking for a technical explanation or theory. Should we focus on the sealer, the chromate layer, or the zinc layer? Would it be the act of bending which creates microscopic cracks in the surface? Could the surface be compromised from the metal on metal contact of the tube to the CNC bender as it is manipulated and formed? We cannot see scratches. Could there be some type of embedded contamination in the sealer from contact with the bender and this metallic dust is what is corroding? Any suggestions would be appreciated. Thanks.
Jerry HawkinsSupplier quality engineer - Sanford, North Carolina, USA
April 8, 2009
Then bending operation is most certainly affecting the chromate and sealer. Unless the bend is very tight and crimped the underlying zinc plating should be ok. The evidence for this is the lack of red rust. The chromate and sealer are passivating the zinc, so when they are damaged you get the zinc corroding, hence the white corrosion. Can you bend the tubing before the zinc plating? If not, how about zinc plating, bending and then chromate and seal?
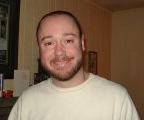
David J. Wolf
Medina, Ohio
April 13, 2009
April 15, 2009
The way I would attempt to resolve this problem is to have salt spray testing, to white salt failure, done on samples of bent tubing and unbent tubing. This would give you a comparison standard. Further, test parts which have no seal over the chromate, both bent and unbent for another level of comparison.
It would stand to reason that the bent tubing will fail earlier as the handling and bending is going to "break" the sealer (the thicker the sealer the more prone to fracture)and consequently may cause scratches in the chromate. Trivalent chromates are, with rare exceptions, not self healing and scratching will lead to salt failures.
Using the data from the first paragraph as a reference, have the plater/plating dept. try other conversion coatings (thick film vs thin film) sealer, etc. to see if any is more applicable to your process.
You might also, although the cost will be higher, look into the use of an alloy zinc.
process supplier - Great Neck, New York
Q, A, or Comment on THIS thread -or- Start a NEW Thread