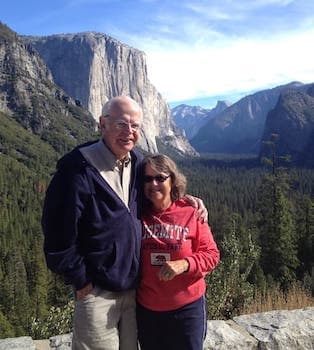
Curated with aloha by
Ted Mooney, P.E. RET
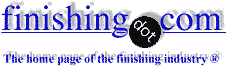
The authoritative public forum
for Metal Finishing 1989-2025
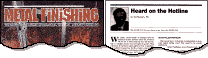
-----
Electroless = Single Element Replacement Process?
My name is Tim Wei, I sell non-toxic shot for shot shell industry and to steel BB users.
I am asked by a customer to do what he calls 'single element replacement process' in depositing a layer of copper on my steel shot. It sounds very much like your electroless plating of copper, can someone tell me if they are the same?
Single element replacement process allows copper to escape from copper sulphate
⇦ this on
eBay or
Amazon [affil links] solution and be deposited on the steel shot (or any steel surface, I was told it is used often on plating copper onto plastics too).
Can someone tell me where I can find solution providers for doing this process?
thanks.Tim Wei
buyer - Irvine, California
March 29, 2009
Hi, Tim. I believe that what you are looking for is what we in the finishing industry call an "immersion plating process". In theory it is indeed as easy as placing the shot in a copper sulphate solution. Due to copper being a more noble metal than iron, iron will dissolve off of the surface of the shot and go into solution, replaced by a small amount of copper coming out of solution and depositing on the shot. This process produces only a very thin coating of copper because as soon as the iron is covered with copper, there is no exposed iron available to go into solution and thus nothing to drive the copper to continue to deposit.
For the process to work reliably and well, you need to thoroughly clean the shot and activate it first. And addition agents including wetters and stabilizers may allow a commercial solution to function better than straight copper sulphate. It isn't clear to me whether you are seeking the process and equipment to do this in house, or a jobshop service to do it for you.
"Electroless copper plating" which is used on plastics is a different and more complicated process, but the reducing agents needed to drive the process are included in the solution, so it can produce thicker deposits.
Regards,
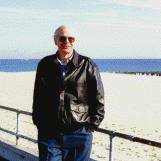
Ted Mooney, P.E.
Striving to live Aloha
finishing.com - Pine Beach, New Jersey
April 2, 2009
The widest use of the immersion coppering process, which Ted describes accurately and well, is a base for mechanical plating and mechanical galvanizing. Anyone who does mechanical plating can do immersion coppering, and suppliers who sell and provide technical support for these process can provide the chemicals and processes required. Keep in mind that this process provides NO corrosion protection. So, why don't they do BB's this way? It's cheaper to zinc plate them and then dye them copper-colored. And it's even cheaper to skip the dyeing step, which is the current practice.
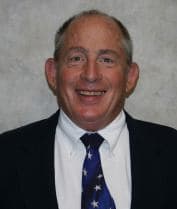
Tom Rochester
CTO - Jackson, Michigan, USA
Plating Systems & Technologies, Inc.

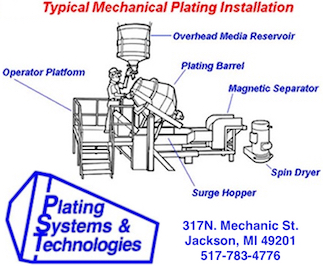
April 3, 2009
April 28, 2009
I posted question number 51752 a month ago and received some good answers.
Further Question:
Does immersion plating of Copper onto steel surface produce any toxic chemicals? What kinds of treatment of waste is required.
I am seeking equipment to do this job.
My product is steel shot, which is spherical and relatively smooth. I was told this process is very quick in coating steel shot surfaces with copper...something like 10 minutes?
Please advice.
Tim
Buyer - Irvine, California
I will speculate that more copper is used for immersion plating electrical ground rods than any other use. As Ted said, consider a commercial copper immersion solution as plain acidified copper sulphate tends to be rough and slough off with contact.
I do not know what various solutions use, but 10 min is probably a good starting point.
- Navarre, Florida
April 30, 2009

Q, A, or Comment on THIS thread -or- Start a NEW Thread