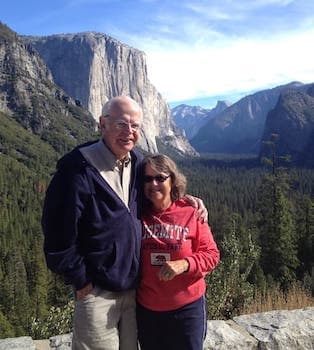
Curated with aloha by
Ted Mooney, P.E. RET
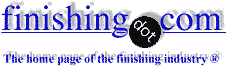
The authoritative public forum
for Metal Finishing 1989-2025
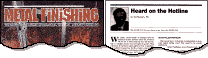
-----
Anodizing Problem, part gets thinner instead of thicker.
I am currently working on a project to set up my own anodizing line. I am anodizing cylindrical aluminium tubes, 80 mm in length and
10 mm outer diameter. I have a problem when I anodize the parts, the anodizing process is removing material from the aluminum tubes instead of building up an oxide layer. Approximately 0.3 mm is taken from the tube wall. I have checked after each stage in the anodizing process and it is not the etching or desmut stage that the material is removed but when I try to anodize the parts. I was wondering what the solution to this problem would be.
The electrolyte I use is 20% sulfuric acid and I use a current of 4.5 amps and 15 volts. Before anodizing I etch the parts in 20% sodium hydroxide and then desmut in phosphoric acid. I have aluminium cathodes and I hang the parts on aluminium welding wire. Also the anodizing tank I use is 100 mm x 200 mm x 100 mm (LxWxH) and I space the cathode/anode as far away as possible.
All the chemicals I use came from a chemistry lab in my college so they should not contain any impurities.
Also my parts don't seem to take the dye I am using. After I seal, and the part has dried the dye has just stuck to the outer surface of the part and falls off when rubbed.
student - Galway, Co.Galway, Ireland
March 26, 2009
Hi, Kevin. The first hint is to concentrate on the anodizing step. The dye is supposed to be absorbed into the honeycomb structure of the anodized film, so the dye cannot be expected to work at all until the anodizing works.
Your electricity is going somewhere. Are the parts or the anodes fizzing like crazy? Is the current being lost to the rack instead of the parts? Good luck.
Regards,
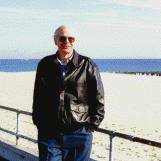
Ted Mooney, P.E.
Striving to live Aloha
finishing.com - Pine Beach, New Jersey
March 31, 2009
First of three simultaneous responses -- April 1, 2009
20% is too strong for the acid. Typical is 15% by weight, NOT by volume. Also, reagent grade sulfuric acid is typically slightly more concentrated than commercial sulfuric.
Next is temperature. If it gets above 72F at anytime during the process, the acid will eat the oxide as fast as it forms.
Kick your voltage up a bit, to say 18Volts and drop your temperature down to about 68F.
- Navarre, Florida
Second of three simultaneous responses -- April 1, 2009
Kevin
You do not say how many tubes you are anodizing at one time so here goes, based on one-at-a-time.
Depending upon the bore size, your part has an effective surface area ranging from .03 - .04 sq.ft. We will discount the surface area of the wire rack. At 15 asf, you should be drawing .67 amps (per part). At 4.5 amps, you have a current density of about 100 asf. At 100 asf, you could expect to be dissolving the aluminum surface rather than forming an oxide film. The resulting coating would be powdery at best.
Process your parts at .5 - .67 amps each. Wire them securely and provide some solution movement to dissipate heat. Run for 30 - 25 minutes to form a coating ~.5 mils thick.
- Colorado Springs CO
Third of three simultaneous responses --
You are clearly not succeeding in anodising, so I suspect you are dissolving the aluminium. First of all, what temperature are you anodising at and secondly have you got your connections round the right way? When anodising, the bath should be ideally below 5C and the workpiece should be anodic.
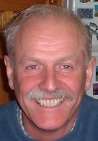
Trevor Crichton
R&D practical scientist
Chesham, Bucks, UK
April 2, 2009
April 3, 2009
I am a little surprised that no one has pointed out that the parts ALWAYS get thinner. The aluminium oxide forms by dissolving some of the aluminium and converting it. Typically the loss from the surface is ~50% of the thickness of the oxide.
Typical acid concentration is 10% or 160-280g/l
Anodes are commonly lead sheet
You refer to the tubes as aluminium. Very few parts are manufactured from pure aluminium. The sulfuric anodise process is not suitable for alloys with more than ~7.5% alloying elements. Mixing alloys in one bath load may cause problems.
Wind those jigging wires tight. Intermittent contact is a disaster. The wire gets anodised and then is insulated from the work!
Most sulfuric anodise lines are voltage controlled with the voltage being ramped up from zero over about 5 minutes and then held at maximum for the required time.
The temperature is commonly not controlled (17-22C) unless high currents cause heat build up.
Temperatures below 5C produces 'hard anodising', This can produce a thicker oxide film but is not suitable for dying.
Do not leave the parts in the bath after anodising or the oxide will start to dissolve.
Test the anodised surface by applying a spot of dye (a felt tip pen is a crude test) and see if it can be rubbed off. A similar test after sealing proves the quality of seal.
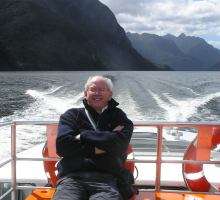
Geoff Smith
Hampshire, England
Q, A, or Comment on THIS thread -or- Start a NEW Thread