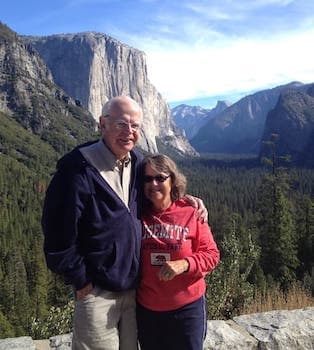
Curated with aloha by
Ted Mooney, P.E. RET
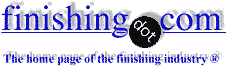
The authoritative public forum
for Metal Finishing 1989-2025
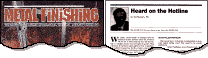
-----
Trivalent Chromate Immersion Times
Hi. My name is Kate Schwab. I'm the quality manager for a metal finishing company in Edgewood, MD. We are looking to add trivalent chromate conversion conforming to MIL-DTL-5541 [⇦ this spec on DLA] Type II to our list of pretreament processes and are in need of information regarding immersion times for obtaining Class 1A and Class 3 coatings. The supplier for the trivalent chrome chemical we are using recommends an immersion time of 3 - 5 minutes, but we'd like to narrow that down to specific times for each class. The trivalent chrome chemical we are using is Luster-On Aluminescent. If anyone has any information, please contact me. Thank you.
Kate SchwabQuality Manager - Edgewood, MD, United States
March 25, 2009
Chromate conversion coatings, hexavalent or trivalent,have three main variables to control the thickness of the coating. They are: Time, temperature, concentration.
A change in any one of these will result in a change of thickness. Therefore, for time to be constant the concentration and temperature would need to be constant and to a lesser extent an additional variable - agitation. Basically, if you are controlling the temperature and the concentration you should be able to run some trials and determine the time necessary. Get some help from a tech rep from the supplier!
process supplier - Great Neck, New York
March 28, 2009
April 16, 2009
Hi Kate,
In our experience (so far) in a production environment the contact resistance requirements for Class 3 coatings are the hardest to meet with the Navair TCP products, pre treatment is critical and it seems must be optimised for what ever "flavour" of TCP you use and they appear to be more sensitive than the clear chromates such as Alodine 1500. Non etch cleaners, minimum de ox time and clean rinses (as in de min) are a start, immersion times less than 3 minutes - the original Navair project ran panels at 2 mins immersion time (We've been through a test program from 30 seconds to 2 minutes in 15 second intervals) and its still work in progress.
The only thing I can say is don't take it for granted that using a product from the QPL will mean you meet Class 3 until you put some work in to optimise the pre treatment cycle and process immersion time. I'd ask the vendor for what ever real life data they might have.
Best of luck
- Lowestoft ,UK
Q, A, or Comment on THIS thread -or- Start a NEW Thread