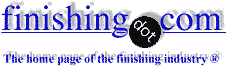
-----
What Vibro finishing does to lengthen salt spray life?
March 23, 2009
Recently we changed our passivation process from hexavalent to trivalent chrome for Al components [composition Classic LM6 with extra 1% Cu. i.e Cu- 1.2% max.]
We were able to achieve Neutral salt spray Life of 240 hours as per our customer specification by introducing a vibro-finishing process.
Now, due to cost considerations when we wanted to eliminate it, we tried different shot blasting techniques with less appreciable results.
What is the mechanism by which vibro improves life?
process designer - Chennai, TamilNadu, India
First of all, the surface will be smoother than a blasted finish. It is just the nature of how the energy transfer system works.A blasted finish produces a greater impact at a single point; where a a mass finishing system produces more of a line similar to lapping. That smooth finish also relates to a slightly more dense surface material profile which is work hardened to some extent by the mechanical action.
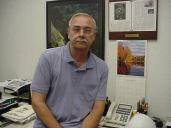
AF Kenton
retired business owner - Hatboro, Pennsylvania
March 26, 2009
Dear Mukundhan RaghuNathan,
for increasing the salt spray Hours, why you want to do Blasting? Better you do Zinc alloy plating like Zn-Ni or Zn-Fe plating or Zinc flake coating all available in Chennai or if only Corrosion better you will do paint by CED and better appearance.
- Salem, Tamil Nadu, India
April 24, 2009
Our customer wants us to do Trivalent Chrome Plating whose coating has to withstand 240 hours. Hence we don't have much freedom to choose the process..
Mukundhan RaghuNathan- Chennai, TamilNadu, India
April 26, 2009
May 4, 2009
Dear Mukumd,
Trivalent Chromium plating is only the passivation, this you are able to do only on Zinc plating.
Better for 240 Hours salt spray, select Zn-Fe with Trivalent Chromium passivation. and for the thickness of plating discuss with your customer or you decide based on the mating part. for me minimum 5 micron is required. for colour again you discuss with your customer.
- Salem, Tamil Nadu, India
May 7, 2009
Are we getting our terms mixed up here? I assume that you require to do a trivalent chrome conversion coating on aluminium, rather than plating and trivalent passivation.
If you blast or peen the surface you impart a certain amount of compressive stress into the surface of the material (with blasting it is only a small amount and not controlled, with peening there is a high level of control and the amount of stress can be monitored). This has the effect of covering any potential flaws in the surface that may initiate corrosion. A compressively stressed surface also resists stress corrosion cracking.
So if you chromate over this surface you tend to get better results than on the unblasted surface. The other effect that blasting has is to increase the surface area of the aluminium (on a very microscopic scale) and so your trivalent chrome is denser as well, helping to increase corrosion resistance.
Aerospace - Yeovil, Somerset, UK
Q, A, or Comment on THIS thread -or- Start a NEW Thread