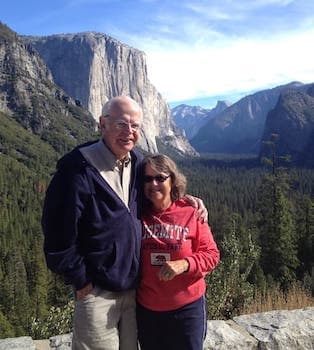
Curated with aloha by
Ted Mooney, P.E. RET
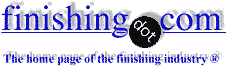
The authoritative public forum
for Metal Finishing 1989-2025
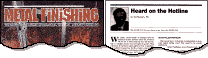
-----
HR1095 scale removal prior to plating
March 23, 2009
I own a small musical instrument company in Neptune NJ that manufactures orchestra bells and glockenspiels which use HR1095 steel as the tone bar. We have been sending out this material for sand blasting to remove the scale, but after nickel plating the finished parts, there are still some black spots that don't take the plating properly. I just chanced upon your site and see that there is a finishing expert right here in NJ that might be able to help us do this by a better method.
We recently tried using a disk grinder and while this "works" it is not pretty and the stock (1-1/4 wide by 3/8 thick) still has to be sand blasted to even it out, prior to plating. We also bought a little drum sander but all we managed to do was melt the belt that feeds the material
Would we be better off with wire brushes or some other method? Having drums of the acid you mention doesn't sound very appealing either. We can't invest in anything expensive since we only process about 200 feet of this material every 3 months or so.
Ideas? Thanks for anything that you can offer.
owner of small musical instrument co. - Neptune, New Jersey, USA
Hi, Leigh. Personally, I think you got it right the first time: blasting. More attention, or a different media may be required. And it's hard to say what the cost would be. But for some critical and hardened aircraft parts you can use only blasting, no acids, so I'm pretty confident that you can achieve freedom from the black spots with blasting alone. Second opinions are welcome.
Regards,
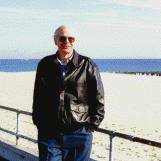
Ted Mooney, P.E.
Striving to live Aloha
finishing.com - Pine Beach, New Jersey
March 24, 2009
Good afternoon:
Have you looked into whether its cheaper to buy your 1095 as hot rolled pickled and oiled (HRPO), instead of descaling after making parts?
- St Louis, Missouri
March 25, 2009
April 2, 2009
I didn't know we could get it pickled but next time we order the material (2017!) we will look into that. The "sound" of this material is what is so critical and we were told that the details of the HR1095 formula is what gives it the long ring time and crystalline tone. We were warned that even the way the steel cooled could change it's sound performance characteristics.
In any case, thank you for the idea.
Leigh
Owner of small musical instrument co. - Neptune, New Jersey, USA
The way it is quenched and or the way it is tempered might make a difference.
Try finding a friend with a small (3" wide) belt sander and do not get in a rush with it. Using several different grits will also help. Since everybody can use one, check out Harbor Freight or Northern tool for inexpensive imported ones.
You can also buy small grit blast cabinets at a reasonable price, but they do use a lot of compressed air, so that may not be worth it for a once in a while job.
Personally, I would buy into what Ted said, let your blaster know that the job is not quite satisfactory and ask him for his help. If he knows what you want and why you need it, he should be able to give you what you need.
If not, consider finding another blaster. Also check with your plater as he might have a
bead blaster
⇦ this on
eBay or
Amazon [affil links]
that he could touch it up with before plate.
- Navarre, Florida
April 4, 2009
Q, A, or Comment on THIS thread -or- Start a NEW Thread