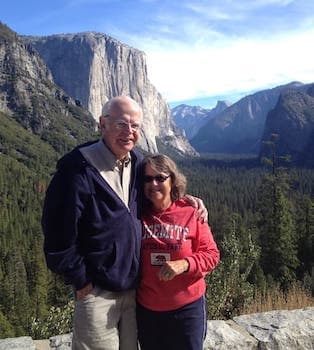
Curated with aloha by
Ted Mooney, P.E. RET
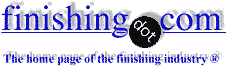
The authoritative public forum
for Metal Finishing 1989-2025
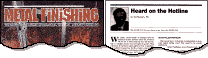
-----
Effect of porosity in metal finishing
Dear sir,
I want to know that how does porosity effect in plating/phosphating
technical service - Jaipur, Rajasthan, INDIA
March 23, 2009
Hi, Suresh. As a matter of semantics, a porous coating means that there are holes in it which expose the next layer or the substrate to the environment. Your question is too broad for a thorough answer but, briefly, the substrate will probably corrode. And, depending upon the type of plating, porosity can mean that the plating will actually accelerate the corrosion of the substrate due to galvanic potentials. For example, a porous nickel plating on aluminum will cause very rapid corrosion of the substrate.
Regards,
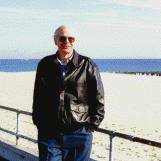
Ted Mooney, P.E.
Striving to live Aloha
finishing.com - Pine Beach, New Jersey
March 24, 2009
Of course, if you mean porosity in the casting base material you will have a different set of effects, some of them just as devastating as having porous plating.
You need to be a little less abstract about what you are trying to do.
Aerospace - Yeovil, Somerset, UK
March 26, 2009
Exfoliation of copper carbonate
⇦ this on
eBay
or
Amazon [affil links]
occurring on porous tin plating over copper substrate is an example for the destructive effects of porous plating.Porous gold plating increases the contact resistance due to corrosion products of the substrate copper or nickel.Porosity affects both functional purposes as well as corrosion protection.One way of overcoming this problem is to have sufficient thickness of the coating to minimise or eliminate the porosity.
In the case of phosphate coating like zinc phosphating and Manganese phosphating which are subsequently dipped in rust preventive oil for corrosion protection ,porosity may help.
S.Ramajayam
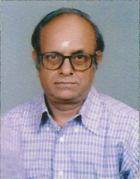
Subramanian Ramajayam
consultant - Bangalore, India
May 2, 2009
May 7, 2009
HI Suresh,
if the parts are porous, more possibilities for corrosion.
to avoid that only we are doing sealant or passivation. if you are not sealing the porous it will get corrode. simple example if you using the parts with out passivation/sealent it will get rust easily.if you are using the parts after passivation, parts will give better life.
- Salem,Tamil Nadu
Q, A, or Comment on THIS thread -or- Start a NEW Thread