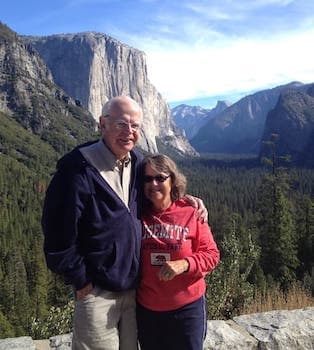
Curated with aloha by
Ted Mooney, P.E. RET
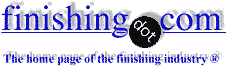
The authoritative public forum
for Metal Finishing 1989-2025
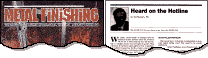
-----
Most resilient/suitable finishing for outdoor steel benches?
Hi everyone!
We are a young design studio in based in Nottingham, we have been asked to design some benches for outdoor use. We have worked with metal powder coating before on other pieces that were for interior use.
So we are considering what finishing would be the most suitable for outdoor use. Resilient to weathering , scratching etc.... Will a thick layer of powder coating be good enough or Nylon coating perhaps?
Would really appreciate the help of someone with experience on finishing outdoor metal pieces or especially benches.
Regards,
product designer - Nottigham, UK
March 19, 2009
First of two simultaneous responses --
You're probably better off asking a paint supplier to provide something based on your requirements. You're probably looking for something that won't chalk or fade, is relatively wear resistant, and has the right surface appearance (glossy, matte, texture, etc.) that you want. If this will be near the ocean, you'd also want better corrosion resistance.
Bear in mind that no one paint can do it all and do it all cheaply. You have to determine what the most important characteristics are and go from there.
- Pittsburgh, Pennsylvania
March 23, 2009
Second of two simultaneous responses -- March 23, 2009
Powdercoating is probably the best thing for a hard resilient coating, and being outdoor use, you'll want polyester powdercoating.
But powdercoating is only effective as a barrier in corrosion protection, so you'll want to do something about that, and you need to have it galvanized first.
Best if you can find a powdercoater and galvanizer in one shop, as those that do these two processes separately sometimes disagree.
And powdercoating on galv is difficult if not done right. The key is in the pretreatment. A competent chromate, zinc phosphate or silane based pretreatment preceeded by adequate degreasing and acid etching is a must.
Get all this done right and you'll have a coating that's maintenance free for 25-30 years and corrosion free for 75 years.
And that should not cost you any more than to shotblast and apply a competent solvent based paint system of probably 3 coats, but such a paint system will last perhaps 5-7 years then need repainting. But if you scratch the paint, you'll get rust eating away under the paint.
With the galv and PC option, even a score through the PC, you'll not get rust.
Good luck. Don't compromise thinking you'll save money. You won't.
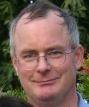
Geoff Crowley
Crithwood Ltd.
Westfield, Scotland, UK
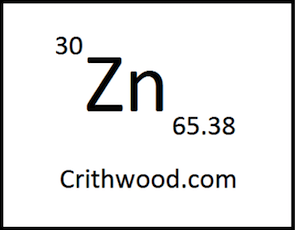
I agree with Geoff on the Galvanized metal and would add that "Super Durable" powdercoat will increase your cosmetic and performance longevity markedly. There has been tests done in South Florida sun and humidity and the outcome was 5 times that of standard powdercoat. I have seen Super Durables used on playground equipment where the warranty is lifetime for paint.
![]() Bob Utech Benson, Minnesota |
![]() Ed. note: Bob is the author of: "High Performance powder Coating" on eBay or AbeBooks or Amazon [affil links] |
I would agree with both Geoff and Bob that for your particular item, PC and galv would be ideal combination. The reason for my input is that yesterday I had the occasion to visit a client with a technical problem¨ our powder was coming of the substrate in large sheets. The galvanized substrate had been pre-treated in what is claimed by the supplier to be the "The millennium's new, all metal, pre-treatment for the PC trade", Zirconium Phosphate. My previous information for this product was¨ very good for aluminium but should not be used on ferrous metal¨ is this true or is Zirconium Phosphate the pot of gold the trade has been looking for? Unfortunately, although I was able to demonstrate that their problem was not due to the powder, I am not sure if this defect is due to poor galvanizing, ill advised pre-treatment or a combination of both? Anyway, on investigation the powder had completely disbonded from the galvanized substrate. However, on the reverse side of the powder I discovered silver like specks. Running a copper coin over the substrate and also my finger nail I was able to remove a similar portion of this bright silver like dust/powder. The substrate varied in appearance from areas of this, to areas one would associate with good galvanising. My next call that day our client also coated galvanised metal but used T-wash (or some may call Mordant wash) which turned the substrate from grey to a black colour and he has never had a problem. This should enforce Geoff's point to use a PC who can prove he understands the coating of galvanized substrates.
Terry HicklingBirmingham, United Kingdom
March 25, 2009
First of two simultaneous responses -- March 26, 2009
We've done some testing on T Wash (or mordant wash), a phosphoric
/ copper wash that etches the surface. (This material has been used extensively as a preparation for wet painting galvanized substrates in the past), and we've not found it so good. Adhesion is the problem. One issue with T wash, is that its normally hand applied, and as a result there are patches over thick (even though its the consistency of water), with thick black deposits, or missed parts.
(Hand application uses humans, and we make mistakes)
I've not heard of Zirconium phosphate as a pretreatment.
We once changed pretreatments, but we tested the new material for over a year in various test phases from bucket up to full production, before moving from a known and trusted material.
Galvanized steel must be the most demanding substrate to powdercoat, and there are no shortcuts.
Thats probably why the list of "Approved applicators" on a large (but not named here)powder manufacturer's website is so short for galv, but so long for aluminium.
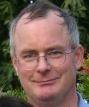
Geoff Crowley
Crithwood Ltd.
Westfield, Scotland, UK
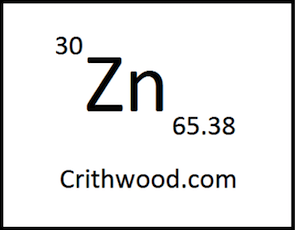
Second of two simultaneous responses --
Dear Panos,
Maybe electropolished stainless steel is a good alternative for the making of your outdoor furniture.
The final product will have more "chique" and cost/price will be competitive with coated steel.
Wish you success.
Regards,
Marc.
- Brugge, Belgium
March 26, 2009
March 27, 2009
Thank you all very much for your advice! It seems that galv + powder coating would be ideal option...since even it by any chance it get scratched at least it won't rust.
I would find the suitable company to speak with now that I know what am looking for. I hope I find that super strong powder coating as well that you have mentioned...
Thanks again for your help.
Regards,
- Nottingham , UK
Q, A, or Comment on THIS thread -or- Start a NEW Thread