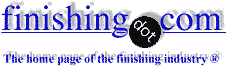
-----
Substitute chemical for sodium dichromate that can be used for the prevention of white rust formation
March 17, 2009Dear Sir,
I am a Trainee chemist working in a Hot-Dip Galvanizing plant in Sri Lanka.
I am interested in introducing a method to minimise white rust in galvanized steel to the company.
The most effective method is to dip the steel in sodium dichromate solution, which is very hazardous to health and environment.
Currently I am researching about Chrome free solutions that can be used instead of Dichromate.
Could you please advice if there is any chrome free solutions available that can be used instead of Dichromate and is just as effective in preventing white rust formation?
If there is what are the specifications of using it?
e.g.: Ph range? Temperature? Amount that should be used in a 19 m3 water tank?
Which is more cost effective? Having a separate bath of the solution or mixing it in the water quenching bath?
Currently we have a open water system, circulating the water between the tank and the pond to cool the water when the temperature rises to above 70 °C.
Will this temperature have an effect on the product?
Hope I will get an answer as soon as possible.
Thanks,
Trainee chemist - Sapugaskanda, Colombo, Sri Lanka.
March 21, 2009
Interesting that you say Sodium Dichromate is very hazardous to health and environment.
Surely its only bad for health if it comes into contact with a person when it's at a hazardous strength?
And how would it get into the environment, unless someone puts it there?
What I mean is that the hazard can be controlled if you want to.
But if you find a good substitute that really works, tell everyone, many want to know the answer to this question.
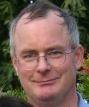
Geoff Crowley
Crithwood Ltd.
Westfield, Scotland, UK
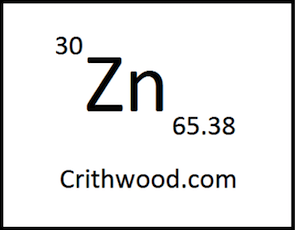
Hi, Geoff. There is a strange disconnect in the finishing world. Virtually every zinc electroplater, mechanical galvanizer, phosphatizer, and dip-spin coater in the world knows about RoHS standards and the carcinogeneity of chromates -- and the overwhelming majority have eliminated chromates in favor of trivalent or chrome-free variations. Yet galvanizers seem to still think it's okay to dip surfaces into hexavalent-bearing solutions. I don't quite get it :-)
Regards,
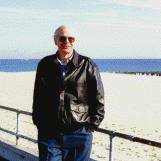
Ted Mooney, P.E.
Striving to live Aloha
finishing.com - Pine Beach, New Jersey
March 22, 2009
March 23, 2009
Sir:
Check this web site and the patent literature under trivalent chrome.
Regards,
Galvanizing Consultant - Hot Springs, South Dakota, USA
Ted,
it sure is strange isn't it! There are many galvanizers (not just UK) still using hex Cr, though some have moved to Tri Cr. I've not heard of any using non-chrome successfully. I guess the main problem is one of temperature. Any post zinc dip passivation is usually combined with quenching. That means the solution gets hot (approaches boiling). As a result, most use very low concentrations of Cr (typically 0.2% or lower). At these low strengths (and ambient passivation won't work at this low concentration), the hazard is much reduced. (Though still something to be avoided if a good substitute is found)
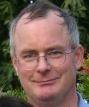
Geoff Crowley
Crithwood Ltd.
Westfield, Scotland, UK
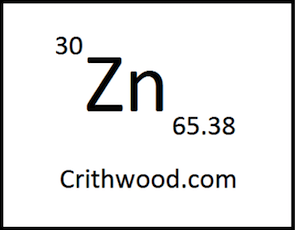
March 24, 2009
Q, A, or Comment on THIS thread -or- Start a NEW Thread