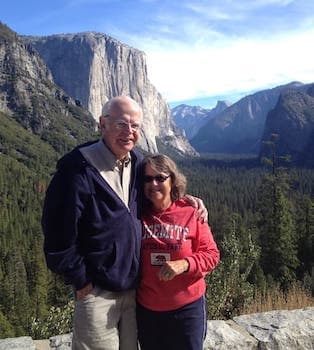
Curated with aloha by
Ted Mooney, P.E. RET
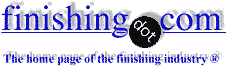
The authoritative public forum
for Metal Finishing 1989-2025
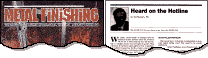
-----
Silver hard soldering on nickel electroforms - crack problem
February 28, 2009
Dear colleagues;
We produce nickel electroforms in a sulfamate based bath.
Our bath is set up for slightly compressive deposits to produce harder electroforms.
We don't have any stress problems and we can easily machine (turn or mill) the parts without any cracks and other failures.
Some electroforms have to be completed with machined inserts, which we have to hard solder in our electroforms. We use 40% Ag 1.0mm soldering wire which has a melting temperature of 550 °C. This is the grade which has the lowest melting temperature available in the market to make strong solders. We can easily weld steel parts on electroforms by using a propane torch. We use the appropriate soldering flux for Ag based soldering wires.
Here the problem comes; After the soldering, when try to mill or turn the parts, the machined sections, especially the corners or thin walls crack like they do in over compressively stressed electroforms. We tried a way to get rid of this problem. The thing we observed is, after the soldering operation, the parts should not be exposed to sudden cooling. For this, after the soldering, while the parts are still hot, we immediately put the parts in an annealing oven and kept there at 350 degrees C for tempering for about 1 hours.
But it didn't work. What can be the solution for this problem?
Also, for the electroformed parts, we use ZAMAK alloy for backfilling. It's melting temperature is around 350 degree C. When we cast the alloy on electroforms which don't require any soldering work, this casting operation has very good stress relieving effects. The electroforms soften a little more to help machining.
Alloy casting on solder applied electroforms have no effect by means of stress relieving.
Any reply to this post will be highly helpful.
Looking forward to receive your posts.
Best Regards
Plating shop employee - Delhi, India
March 12, 2009
This problem has nothing to do with deposit stress.
Your nickel deposit is contaminated with sulfur caused by the decomposition of sulfamate. On heating nickel sulfide is formed. As the problem gets worse from continued decomposition of sulfamate the nickel deposit will crumble on heating.
There is no way to purify the bath; it must be replaced.
In the future you should maximize anode area, minimize current density and lower temperature to avoid sulfamate decomposition. You should also eliminate organic additives, especially saccharin and coumarin. There is no need for stress reducers in a properly operated sulfamate bath.
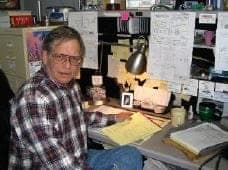
Jeffrey Holmes, CEF
Spartanburg, South Carolina
Q, A, or Comment on THIS thread -or- Start a NEW Thread