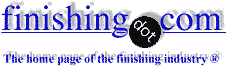
-----
Why is thickness of Manganese Phosphating varying?
March 3, 2009
Sir,
while processing the above process,we came across some variations in results . After a successful trial of few jobs . with the same process we found some jobs under size by 0.020 mm and then reworked and found oversize by 0.005 mm .we doubt for the over size is a dip in HCl acid and what can be the reason for undersize .
How many microns should be the coating on a particular job (
16mncr5).
What are the major reasons for the variation.
Process - Degreasing Above 60°c
Water rinse
HCl Acid dip 2-3 mins
Water RInse
Phosphating Temp - 60°-80°c , Duration - 30 mins
Drying
Oiling
process establishment (R&D) - Pune, India
March 6, 2009
Abhay,
Without witnessing your actual process it will be a little difficult to give you a definitive answer.
First of all, have you checked the dimensions on receipt? There may be variability right from the start.
Secondly, have you checked that all your bath chemistry is satisfactory? Phosphating needs tight control so if you are going out of your specification range you may be causing too much etching at times and at other times you will find you are etching half of nothing at all.
Third, have you considered tightening your process limits? This will reduce some of your process variability.
Finally, check that your final inspection is being carried out correctly. There is always a possibility that someone may be reading a gauge incorrectly.
If you still don't have an answer, try "walking the process", follow one of the problem jobs through the shop, from receipt to final packing. Make copious notes and see if there is any way you can improve the process.
If all else fails contact your phosphate chemistry supplier and see if they have any suggestions.
That should get you started at least.
Aerospace - Yeovil, Somerset, UK
Thanks for mentioning "walking the process", Brian. Before finishing.com made me too busy to continue with it, I was a plating consultant for 20 some years. And I can't tell you how many analysts of various sorts would sit in offices trying to determine the cause of defects by chemical analysis, by tracking defects vs. shifts, or 1001 other attempts at pattern recognition. Then we'd walk out to the line and see that one barrel didn't rotate in the chromate tank because of misalignment, or dirty contacts meant current would periodically not flow to the electroclean tank, or a low level in the acid tank meant some parts weren't activated, and on-and-on. Management strategies go in and out of favor, but "management by walking around" can't be replaced.
Regards,
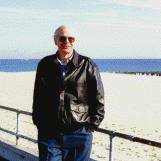
Ted Mooney, P.E.
Striving to live Aloha
finishing.com - Pine Beach, New Jersey
March 6, 2009
Ted,
You are so right, I often get queries from suppliers without them ever having left the comfort of their office actually see what the problem is. In my humble opinion you can't beat a good walk!
Aerospace - Yeovil, Somerset, UK
March 9, 2009
April 24, 2009
Dear Abhay Jadhav,
Always it is possible for variation in thickness for Phosphating.
Normally for Phosphating we will follow only the weight difference.If you refer ISO standards also, they are recommending only the Weight Difference.
- Salem,Tamil Nadu
April 24, 2009
I always like the confusion caused by the operator topping off the phosphate tank with water, then not stirring it and then immediately putting the parts in the tank. First the temp is low. Second the tank is stratified in both temp and in concentration.
Phosphate is a needle like structure. The exact chemistry that day will also control if it is near vertical or more like a flat haystack. This affects the dimensional measurement even when the weight loss is the same.
To me, Mn phosphate is a poor choice if you are going to have tight dimensions. It is a relatively coarse and open material normally used to hold lubrication during break in.
The thicker the coating, the more variation you will see when you think all of the variables are the same. Tank control has to be very tight, not just in the range, if you expect tight results.
- Navarre, Florida
Q, A, or Comment on THIS thread -or- Start a NEW Thread