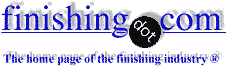
-----
Restoration of Civil War era iron cemetery fence
Readers who are more interested in the practical aspects of repainting/repainting their own wrought iron fence may prefer to start with letter 24101, "Painting/repairing a rusty wrought iron fence" . . .
March 2, 2009Q. Hello,
My name is Paul Waddell. I am an Intern Architect at a firm in Oxford, MS that does a good deal of historic preservation and restoration work. I have recently been charged with documenting the conditions of the perimeter walls at several Civil War era national cemeteries throughout the southeast, and making recommendations for repairing them. Some of these perimeter walls include some corroded iron fencing. One fence (at the Barrancas National Cemetery within the Naval Air Station in Pensacola, FL) is in particularly bad condition...
The easiest and seemingly most prudent thing to do would be to replace the severely corroded fence with a new wrought iron fence matching the profiles and details of the original, but my recommendations must be approved by the State Historic Preservation Official, who's primary concern is retaining as much original 'historic fabric' as possible... So, I have to come up with a way to save as much of the original fence as possible.
The fence panels are 9 to 10 feet wide and about 5 feet tall, and are bolted to concrete piers and intermediate 'I beam' posts. As you can see in the pictures, there is substantial pitting and material loss throughout.
Also, some of the fence is covered in lead paint, which will have to be removed. My initial thoughts are to unbolt and remove the fence panels and have them dipped in an acid bath, or 'acid pickled' to remove the lead paint and rust (as opposed to grit blasting, which would scatter lead paint dust and damage the original mill scale of the iron). Then, any pickets too corroded to repair would be cut out and replaced. Minor defects and small areas of material loss would be patched with Bondo
⇦ on
eBay
or
Amazon [affil links]
or other epoxy resin mixed with iron particles (to deal with the resin's different rate of expansion & contraction). The 'I beam' posts (which are in moderately better condition) would remain in place and be flame cleaned and wire brushed to remove the rust (acid pickling not being an option). Both fence panels and posts would then be primed with a zinc rich primer before being reinstalled and receiving an epoxy basecoat and two urethane finish coats (the most durable finish for iron in a marine environment, according to my research).
These initial recommendations were derived strictly from research, as I have no prior experience with acid pickling, spot patching, or refinishing corroded wrought iron such as this. I welcome any advice from anyone with hands on experience in this arena. Also, I am struggling to estimate the scope of work outlined above. My repair and remodeling cost data book does not include this kind of work. I don't even know what unit to use for 'acid pickling' (by the square foot, lineal foot,fence panel?). Could anyone give me any kind of unit cost for budgeting purposes, so I could come up with a ballpark figure?
Overall, the fence consists of about 70 panels (5 feet tall x 9 to 10 feet wide), two large vehicular gates, and two smaller pedestrian gates. I hope that I have provided enough information here. If I need to clarify anything, or provide additional information, including pictures, I'd be happy to do so. I hope this sparks some interest.
Thanks,
Intern Architect - Oxford, Mississippi, U.S.A.
Q. This is an amendment to a previous inquiry about restoration methods for a badly corroded wrought iron fence at a Civil War era National Cemetery. I won't repeat all my personal details or the details of my specific situation (as they were in my previous inquiry), but rather ask more pointed questions. Based on the conditions shown in the pictures I sent, what would be the most effective method of removing rust? And, once the rust has been removed, what method and material could be used to patch and fill-in areas of severe material section loss (that would likely stay in place under normal circumstances)?
Respectfully,
Intern Architect - Oxford, Mississippi, U.S.A.
March 3, 2009
A. Hi, Paul. There is a technique that I have heard of from time to time over the decades, but I have never seen it and never read an authoritative paper about it. It is called, I believe, electrolytic restoration or reverse hydrolysis. The theory is that the material has rusted due to electromotive forces and if you overcome them and reverse them, you can convert the rust back to metal. Theoretically and ideally, the metal forms again from the rust at the exact point where it originally was. For bronze artifacts in seawater it works great.
I'm sure that it can't really work well in your case because some of the rust has run down the drain, and mechanical forces and movement has displaced some of the corrosion products, but it is the only thing I can think of that has a prayer of partially restoring the fence. For a very light and non-scientific coverage of the process, Randy Wayne White's outstanding novel "Dark Light" includes scenes of the protagonist practicing this procedure on some artifacts.
Hopefully one of our readers can point you to a paper on the subject, and advise whether it has any merit on iron.
Regards,
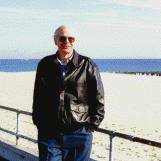
Ted Mooney, P.E.
Striving to live Aloha
finishing.com - Pine Beach, New Jersey
March 4, 2009
A. Don't use acid. It will remove the rust but the rust will start in again within three minutes of removing it from the acid bath.
Unbolt the corroded fence panels, and strip the paint, using a gel type/methylene chloride stripper. Wire brush off the loose rust. Then, do your bondo work.
Now, give it a treatment with a nice phosphate wash primer, and repaint.
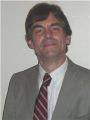
Dave Wichern
Consultant - The Bronx, New York
March 4, 2009
A. One answer is to contact an on-site powder coating company. As this new process is used more in the USA than most other countries you should have no problems in locating one.
They should be able to offer shot blasting to remove the rust, fill with polyester filler damaged areas and then coat using either a thermoplastic or thermosetting (new) primer followed by powder top coat. The principle is to apply the powder using flame technology. The finish is not as smooth as standard powder coating but is ideal for your situation. It could be quite costly as it is very slow application process, but should offer another >20 years life span.
Birmingham, United Kingdom
March 5, 2009
A. The rules concerning lead are strict and just became tighter. I would have a paint shop that knows the procedure do the work. Removing to their shop makes sense.
Consider Chloride removal because the surface must be contaminated.
No need to mix metal into the epoxy. Today's epoxy will expand/contract with the iron.
Let me know if I can advise more.
Regards
- Concord, California, USA
March 5, 2009
Q. Ted and Dave, Thank you very much for your responses.
Ted, I had not heard of the electroytic rust removal process, but am intrigued... I managed to find some information (no authoritative papers, but more DIY) and a couple of examples of its successful utilization. Results were impressive, but all were on a very small scale (i.e.-small cultural artifacts for museum display). Do you know if this process is used commercially for larger scale restoration projects?
And, Dave- Could factors such as the type of acid, the concentration of the solution, or environmental factors such as relative humidity in the workspace possibly delay the immediate re-rusting of the iron long enough to brush on a good coat of primer? My concern is that wire brushing alone might not remove ALL the corrosion. Also, what is the relative cost difference (ballpark) between wire brushing and acid pickling? Seems like wire brushing would require quite a bit of labor.
Respectfully,
Paul Waddell
- Oxford, Mississippi, U.S.A.
March 5, 2009
A. Sorry, Paul, all I have on this is heresay and one or two lines from Charles Faust's ASM "Electroplating Course". I agree that it sounds like it would work better on small items than large. I also assume it would work better on non-ferrous items, where the corrosion products are relatively stable, than for an iron fence where some of the rust has washed away. I only mention it because if you are determined enough to restore it that you are willing to experiment, that's one area for experimentation. Good luck.
Regards,
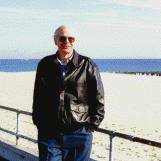
Ted Mooney, P.E.
Striving to live Aloha
finishing.com - Pine Beach, New Jersey
March 5, 2009
Q. Does anyone have any prior experience with OSHA and EPA requirements for worker protection and hazardous waste disposal associated with using methylene chloride to strip lead paint (on-site application and/or off-site submersion in vats)? If so, how would you estimate a budget for this?
It seems like the methylene chloride stripper is viewed by government agencies as being just as hazardous, if not more so, than the lead paint waste...
- Oxford, Mississippi, U.S.A.
March 11, 2009
A. OSHA says:
http://www.osha.gov/SLTC/methylenechloride/
MSDS:
http://www.jtbaker.com/msds/englishhtml/M4420.htm
Regards
- Concord, California, US
March 16, 2009
A. That is a job for a professional metal conservator -- try AIC (American Institute of Conservation) website; there you can you find a list of certified metal conservators. Hope it helps and good luck!
Goran Budija- Cerovski vrh Croatia
March 17, 2009
A. You could also try a product called Peel Away
[affil links]
It's a Mg(OH)2/Ca(OH)2/NaOH paste. It is caustic, but gives off no fumes. You apply it, cover it with a paper that they provide, leave it for 12 - 24 hours, then scrape it, and the removed paint, off.
It's lots more labor intensive than methylene chloride type products but more environmentally friendly.
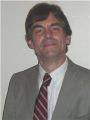
Dave Wichern
Consultant - The Bronx, New York
March 17, 2009
March 18, 2009
A. The most simple process is to take the fence sections to a company which does stripping of auto bodies for restoration. They use alkaline processes which remove all rust and old paint, but which do not attack sound metal. This will give you nice clean metal ready for priming and paint.
Bondo on an historic restoration? Horrors! After stripping, have the badly rusted sections cut out and new metal welded in, then a coat of good quality primer and several coats of good quality color.
Done right, and with proper maintenance, your restoration will last another 100 years.
If you use Bondo, It'll be junk in 25.
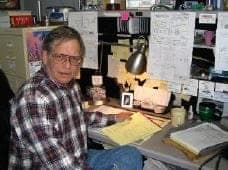
Jeffrey Holmes, CEF
Spartanburg, South Carolina
March 24, 2009
i. This is not an answer to your inquiry, Paul. But since I dropped one shoe that will be found in search engines, here is the citation from Faust's ASM Electroplating Course:
"A particularly valuable process to restore artifacts might be referred to as electrolytic scale reduction. Over the centuries, bronze and silver items have been changed by exposure to the environment to almost solid masses of corrosion product. This change took place at a very slow rate. By cathodic treatment at a very slow rate in a dilute alkaline solution, the corrosion process is reversed. The corroded artifact of unrecognizable shape is converted back nearly to its original form and design."
Here is a video reputedly showing reverse electrolysis for the recovery of silver coins:
[Update Oct. 2014: sorry, that video is now gone].
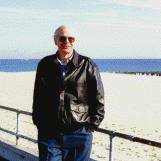
Ted Mooney, P.E.
Striving to live Aloha
finishing.com - Pine Beach, New Jersey
March 29, 2009
A. Try
cool-palimpsest.stanford.edu/byform/mailing-lists/cdl/2002/1478.html
For conservation.
Then a good quality paint job
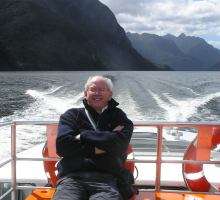
Geoff Smith
Hampshire, England
I'm glad to see all the responses since I last checked this thread. I just wanted to thank everyone who posted a response. All of the advice has been a great help to me. Thanks, again.
- Oxford, Mississippi, U.S.A.
May 8, 2009
September 28, 2009
A. As a custom ornamental metal fabricator I have researched this matter in an attempt to win some of this restoration work.
The lead is the greatest concern initially. The awarded firm must engage a Certified Industrial Hygienist (CIH) up front and submit to them for approval a comprehensive plan for eliminating the lead based paint hazards from start to finish.
Soil testing must occur prior to doing any work to establish a benchmark level to measure the amount of existing lead, and the remaining lead paint which still hangs on the fence must be encapsulated. A painting contractor needs to seal coat it in a shellac or sprayed wax or other simple sticky coating before the fence is handled.
Then the panels can be removed to a location where they can be dipped into a chemical stripper. The waste from this process has to be documented and disposed of with manifest provided to a federally controlled Hazardous waste dump site. (Federal Regulations on this too but your consultant will help you) FYI, it costs about $550 per 55 gal. drum to dispose of this kind of waste.
Finally, now with the paint, stripper, tainted gloves and rags and lead gone (and the consultant now too), the restoration work and refinishing work can begin. Follow standard finishing practices here (epoxies and urethanes etc). Galvanizing may be possible and especially helpful in humid and or salt air environments.
The posts which remain on site must be stripped on site and waste disposed of properly. Do everything possible NOT to atomize or disrupt a crusty finish which contains lead. Blasting is the LAST thing you want to do. Once stripped they should be primed immediately if not painted.
There is more to be discussed in terms of restoration or replication, when is the product too corroded to repair, how joinery affects the final finish, (welding vs bolting) handling the product in the field and in transit and touch up on site (paint vs. powder) not to mention what the problems are associated with using modern steel in place of wrought iron which are two different alloys and wrought iron weathers better but that starts to have less to do with finishing and more to do with fabrication.
Thanks,
- Tulsa, Oklahoma USA
Hi Doug. Thanks for the exposition proving that when we demand zero risk, zero can be produced.
We may fool ourselves that we can do it if we just spend enough money on it -- but then we remember that actual money is the product of production, so society can't buy its way out of such knots :-)
Regards,
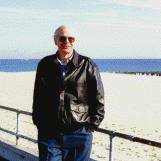
Ted Mooney, P.E.
Striving to live Aloha
finishing.com - Pine Beach, New Jersey
A. Go to vintage metal, inc. website and you can learn a lot from this company. Call people who have already done historical restoration work and "pick" their brains.
Beverly Smetko- Newport Coast, California USA
November 9, 2009
Hi folks. I now see this book on Amazon .
I don't have a copy and haven't read it, but Amazon's "Look Inside" feature reveals that it seems to cover the subject in exhaustive depth. Good luck.
Regards,
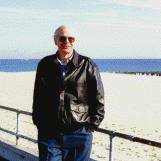
Ted Mooney, P.E.
Striving to live Aloha
finishing.com - Pine Beach, New Jersey
November 2014
Q, A, or Comment on THIS thread -or- Start a NEW Thread