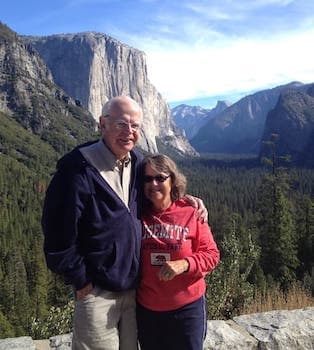
Curated with aloha by
Ted Mooney, P.E. RET
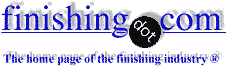
The authoritative public forum
for Metal Finishing 1989-2025
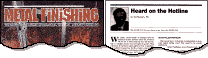
-----
Etching Inconel 600 with ferric chloride
February 24, 2009
Q. Hi, my name is Chris and I work as a Process Engineer among which some of my responsibility involves an etching process. We etch Inconel 600 using ferric chloride
⇦ this on
eBay or
Amazon [affil links] . I've learned that etching Inconel is not real common so most of what I've learned has been from my own experience.
Inconel 600 primarily consists of nickel, chromium and iron. Up to this point, the only chemistry control that we've had is ORP, baumé and temperature. I'm experimenting with measuring the HCl and the pH of the bath. Our ORP, baumé and temperature are automatically controlled. After a fresh bath change our etching speeds are very good, but then they begin to deteriorate over time. We know that the ORP drops and then sustains a certain level but the bath continues to deteriorate. The ORP controls call for fresh ferric and HCl to be added, but we also sometimes pump HCl into the bath manually. Our experience tells us how often we should dump the bath and start with fresh ferric, but I'm trying to look at this more scientifically. I've been told that the ORP is basically meaningless since we aren't etching something with a high iron content.
1) Is this accurate?
2) When our etching speeds get slow we do a complete dump and cleaning and then recharge the bath with fresh ferric. This is about a 6 hour process to do it well. I'm toying with the idea of having more frequent dumps, in which case I would replenish with new ferric. I wouldn't do a complete cleaning every time, but at the same frequency that we currently dump and clean. The intermediate dumps would only involve removing the existing ferric and pumping in new which would take about 1.5 hours. I've calculated the costs of doing this and I think that it would be worth a try since our productivity would improve (faster etching speeds) if we had fresh ferric. I've estimated that we would basically use the same amount of ferric because under the current scenario ferric is fed into the etcher based on the ORP reading, which is not completely relevant for our case, at least I think. Does this seem to be a good approach since the ORP isn't a good indicator?
3) When we do a bath change, we often times find little black crusty chips of material in the etcher. I'm thinking that they are one of the metals that didn't go into solution. Is there a way that I can determine what these chips are made of? When we do a bath change, the chips break loose and many time wind up clogging the nozzles for the first couple of days after the bath change.
4) I've been etching samples each time I check the HCl level to check for the quality of the etched product. In our process we see quite a bit of variation in the quality of the etched traces and I'm wondering if it's a function of the HCl level or the quality of the ferric, both or something else. Any ideas?
Thanks and I appreciate you taking the time to read this and responding.
Engineer - Columbia, Missouri USA
A. Chris
ferric chloride
⇦ this on
eBay or
Amazon [affil links] is a great etchant fore Ni, Cr and Fe. It is not a good etchant for their oxides. So you need a fairly high HCl concentration to get through the oxides so that ferric chloride
⇦ this on
eBay or
Amazon [affil links] can do its work.
The best etching systems maintain constant etching rates by bleeding in fresh ferric chloride
⇦ this on
eBay or
Amazon [affil links] and overflowing spent ferric to control the Cr and Ni concentrations in the etchant. Continuous regeneration of ferrous to ferric is also necessary to get a consistent etch rate.
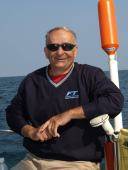
Pat Mentone
St Paul, Minnesota
February 27, 2009
Q. Dear Mr. Pat Mentone,
As suggested that we need a fairly high HCl concentration to get through the oxides so that ferric chloride
⇦ this on
eBay or
Amazon [affil links] can do its work. Could you just elaborate that what should be the appropriate % of HCl to mix in FeCl3 solution and how much HCl to be added in ferric chloride
⇦ this on
eBay or
Amazon [affil links] .
I am asking this question, as we are facing problem of fast deterioration of ferric chloride
⇦ this on
eBay or
Amazon [affil links] solution. As we change supplier of solution and getting new solution of about 950+ redox value, but after using for about 3 hours we found Redox value is 625. What could be the probable reason for that?
I will be grateful for your answer.
Production - Dubai, UAE
September 9, 2010
Q. Dear Sir
This is Anand I would like to prepare etching of Incoloy materials. In what am research on, chemical mixing is used.
Regards,
professor - Trichy, Tamilnadu, India
March 25, 2013
A. Hi Anand. Sorry I can't quite follow the question. Can you phrase it in terms of what Pat Mantone has already said, or what he has left out that you are interested in?
Regards,
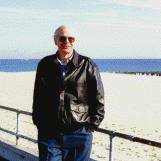
Ted Mooney, P.E.
Striving to live Aloha
finishing.com - Pine Beach, New Jersey
March , 2013
Q. What is the etchant for inconel 693?
Nagaarjhuna Arumugakani- coimbatore, TN, India
May 20, 2014
Q. Hi, I want to etch a weld specimen, which is inconel 600. I want to see the microstructure totally -- and whatever it has such as carbides and liquation cracking which may have occured during welding. Thanks if anyone can help me.
zana naz- Turkey
June 6, 2014
Q, A, or Comment on THIS thread -or- Start a NEW Thread