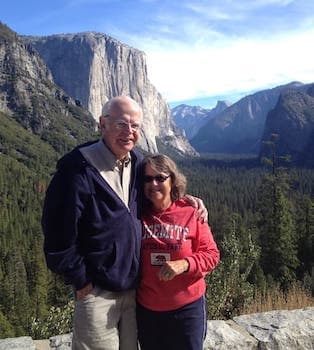
Curated with aloha by
Ted Mooney, P.E. RET
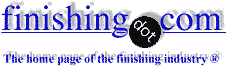
The authoritative public forum
for Metal Finishing 1989-2025
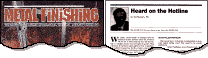
-----
A different Zinc/ Hydrogen Embrittlement question
February 25, 2009
Material: Normal Steel commercial grade (1.5 mm).
Machining: Formed by Press
Hardness: Heat Treated to 35/38 HRC.
Finish: Acid Zinc, barrel plated.
Post Treatment: Baked at 375 ± 25 degrees for 4 hours within 1 hour of plating.
My question is we have people here in my company that feel the best way to check for Hydrogen Embrittlement is to strike each part in a hand press prior to using.
I feel this may cause damage to the parts in the way of a stress riser that could actually fail at a later date.
Any ideas or thoughts would be greatly appreciated.
Sincerely,
Manufacture with In house zinc plating - San Diego, California, USA
Hi, Russ. After an auto company puts Buster the Dummy in the car on a rocket sled and smashes it into an anvil to test the airbags, I certainly hope they scrap the car :-)
I think I would agree that you don't ship parts that have been destructively tested :-)
Regards,
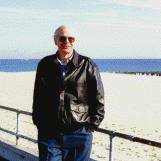
Ted Mooney, P.E.
Striving to live Aloha
finishing.com - Pine Beach, New Jersey
February 25, 2009
First of two simultaneous responses -- February 26, 2009
At that hardness, embrittlement is not normally a problem, especially with your bake. If you are really concerned, you can run notch bar testing (not cheap). If you want to add a bit of safety, cut back the time that you spend in the acid etch as that is where a major portion of your embrittlement will come from. Next, cut the plate to bake time to 1/2 an hour.
You may be able to find a lab that can do ultimate strength testing of a few samples of each plating lot.
Unless it is a specification requirement, I do not think that I would worry about it.
A cheap indicator test would be to double nut the bolt, clamp the bottom nut in a vice and use a big torque wrench to see if you can break the bolt. At least, you will know the torque that it broke at.
- Navarre, Florida
Second of two simultaneous responses --
Ted is right, you can't ship destructively tested parts, even if they pass. If you need to test for hydrogen embrittlement consider using test pieces and testing in accordance with ASTM F519.
Brian TerryAerospace - Yeovil, Somerset, UK
February 27, 2009
February 27, 2009
Hydrogen Embrittlement is premature failure under a tensile load. So to test the parts, just put them under a tensile load for 48 hours and see if any 'pop.' But if the article isn't going to be under tensile stress, this test would be sort of meaningless. By the way, why don't you use a non-embrittling process like mechanical plating or dip-spin painting? Baking isn't 100% foolproof. (See ASTM B849-02 & ASTM B850-98 ).
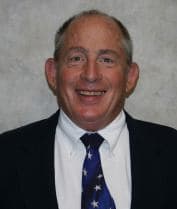
Tom Rochester
CTO - Jackson, Michigan, USA
Plating Systems & Technologies, Inc.

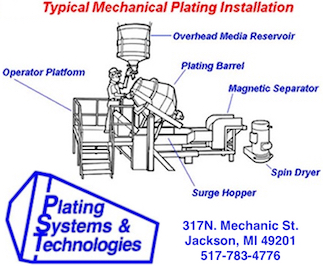

Q, A, or Comment on THIS thread -or- Start a NEW Thread