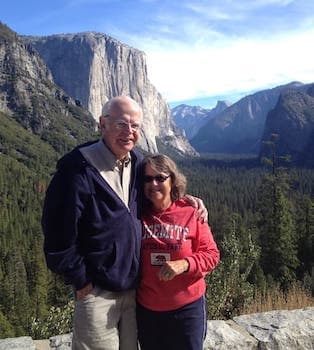
Curated with aloha by
Ted Mooney, P.E. RET
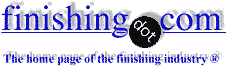
The authoritative public forum
for Metal Finishing 1989-2025
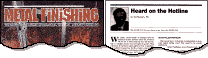
-----
Stainless Steel Pipes Used in drencher systems for passenger ships
am mechanical engineer working n marine service company, my company have been told to build up a new lines for drenchers using Stainless steel pipes 316 L , but after installed the pipes I had problem which is the pitting corrosion in the pipes in less than one month and the drenchers are using the seawater in normal temperature ......my question is which type of Stainless Steel will be more suitable for this job ? will resist the pitting corrosion ?
Samer Shoukinimarine service - AQABA Jordan
February 22, 2009
September 20, 2009
You can have the pipes electropolished inside and out to increase the corrosion resistance significantly. T316L is a good choice. There are many tests/reports that show and prove corrosion resistance is increased by electropolishing, more so even, then just passivating.
You can also look into duplex stainless steels. They have a higher nickel/chromium content and will be proportionately higher in price. Below is some info on duplexes
"Duplex stainless steels have a mixed microstructure of austenite and ferrite, the aim being to produce a 50/50 mix, although in commercial alloys, the mix may be 40/60 respectively. Duplex steels have improved strength over austenitic stainless steels and also improved resistance to localised corrosion, particularly pitting, crevice corrosion and stress corrosion cracking. They are characterised by high chromium (19ù28%) and molybdenum (up to 5%) and lower nickel contents than austenitic stainless steels. The most used Duplex Stainless Steel are the 2205 (22% Chromium, 5% Nickel) and 2507 (25% Chromium, 7% Nickel); the 2507 is also known as "SuperDuplex" due to its higher corrosion resistance. Duplex stainless steels properties are achieved with an overall lower alloy content than similar performing super austenitic grades making their selection and use cost effective for many applications"
electropolishing shop - North Vancouver, British Columbia, Canada
Q, A, or Comment on THIS thread -or- Start a NEW Thread