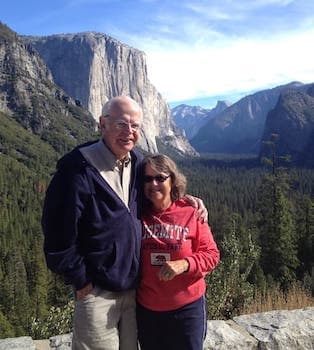
Curated with aloha by
Ted Mooney, P.E. RET
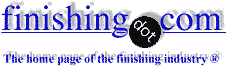
The authoritative public forum
for Metal Finishing 1989-2025
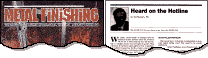
-----
White rust questions
I am having an assembly produced overseas. It calls for a 150 hr salt spray test, which supposedly it has passed. We noticed that one unit when exposed to salt water one day quickly developed white rust and dark gray spots within hours. Is this as feared, a poor plating job. or is there something going on that I don't understand?
buyer - Lexington, North Carolina, USA
February 23, 2009
First of two simultaneous responses --
Salt spray testing is a "fog" with a controlled salt content and amount as well as temperature. Salt water can have a lot more salt and if immersed, it will fail a lot quicker than the fog test. Yours looks sorry and I would have concerns as to when the salt spray testing was done in relation to when your part was plated. (as well as the quality of the test cabinet and conditions.)
James Watts- Navarre, Florida
February 25, 2009
Second of two simultaneous responses -- February 26, 2009
It will be helpful if you can provide answers to the following questions...
What type of plating did your equipment receive? I suppose probably zinc (maybe with our without passivation or chromate).
Is the salt spray testing 150 hours to red rust or 150 hours to white rust?
I can't remember for certain... bit I think you will get 12 hours protection to red rust for each 1 micron (40 microinches) of zinc plating thickness. Therefore, about 12 microns (480 microinches) might give you close to 150 hours to red rust.
BUT... if you don't have any passivate or chromate layer you will have no protection to white rust. Therefore... it is possible that they plated your equipment to 500 microinches... but did not apply a chromate or passivate ± a sealant.
For the white rust protection you need a chromate or passivate + sealer.
In the future you can specify something like 96 hours NO WHITE RUST in which the plating shop will need to apply a good passivate + sealant.
- Budapest, Hungary
As stated previously, salt spray testing is a fog exposure test. What it does is tell you how corrosion resistant the test object is for this test. The only real world meaning is generally the greater the protection to the test the greater the real world corrosion resistance. If you have a specific need you should contact the vendor and determine what needs to be done to meet that requirement and then specify a test procedure. It would be best if parts are random tested, not submitting specially prepared coupons. Further, if you are having the part manufactured off shore you should periodically have parts checked at random to verify that the parts do indeed meet your standard.
Gene Packmanprocess supplier - Great Neck, New York
February 26, 2009
March 1, 2009
Mr. Mark Lambros
Firstly I would apply a 25 % benchmark to the 150 Hours SST norm. I would ask my overseas supplier to work on 200 Hours to White rust.
Secondly I would prepare, or have prepared a detailed standard that includes process parameters, Plating specs and test norms including the name of an approved Neutral test house in the supplier's country that tests and approves periodically with test certificates the components from an overseas supplier.
I come from a country called India which is an overseas supplier to numerous countries . This is how things are done her to achieve consistent low failure rates.
Lastly a neutral inspection agency or a inspector to oversee and coordinate this activity and make sure the tests are done as ordained in the contract.
And I do believe some of the measures that I suggest could work for You. Its the system that makes the Chemistry work.
Technically speaking, a proven Trivalent Chromate and Topcoat applied over 15 - 18 microns of Alkaline Znc can work to the hours you need
.. 200 to white rust and 300 and more to RED rust.
Regards,
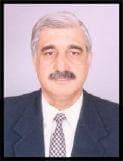
Asif Nurie [deceased]
- New Delhi, India
With deep regret we sadly advise that Asif passed away on Jan 24, 2016
Q, A, or Comment on THIS thread -or- Start a NEW Thread