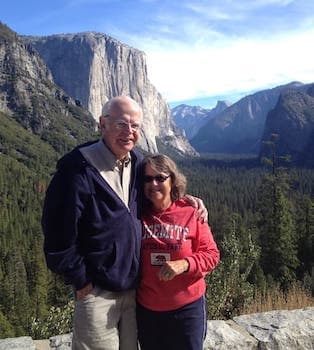
Curated with aloha by
Ted Mooney, P.E. RET
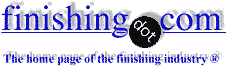
The authoritative public forum
for Metal Finishing 1989-2025
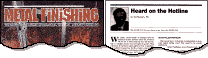
-----
Powder Coating Failed Salt Spray Test
Quickstart: Powder coating can fail salt spray testing for various reasons, but a common cause is inadequate pretreatment. The traditional pretreatment for aluminum is cleaning & chromating; for steel it is phosphating. Due to environmental pressures (shortsighted?), alternate pretreatments based on silanes and other technologies are often implemented these days; the pretreatment chemistry supplier should be consulted regarding their idiosyncrasies.
Q. Actually we have done powder coating for a part which has both aluminum casting sub part and aluminum sheet metal sub part for which we carried out 7 stage Pretreatment process (Degreasing - 3 stages, raw water rinse, DM water rinse, Oxsilan treatment, DM rinse) and we have used TGIC-free polyester powder. As for curing, travel time mentioned in TDS [technical data sheet] is followed but with a excess of 6 minutes of travel time. But the part passes the color test. Could you please provide me potential cause of failure for the part in Salt fog test for 720 hours?
Sarath Raj- Tamilnadu India
December 8, 2023
by Raj & Ali
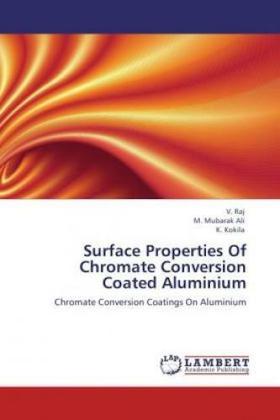
on AbeBooks
or eBay or
Amazon
(affil links)
A. Hi Sareth. Your proprietary thin-film silane pretreatment for aluminum is not the same thing as a chromate pretreatment but may certainly be more than adequate. However, if its TDS states that a maximum travel time is important and you are exceeding it, certainly you need to get from your vendor their take on why travel time is important and what impact should be expected if it's exceeded. Sorry, but I wouldn't know whether this is a problem or not.
You apparently converted a 7-stage phosphate line to the needs of the new chemistry by preserving the tankage and adding additional degreasing -- that sounds like a smart move towards more robust pretreatment :-)
If you are not able to get good and quick suggestions from your vendor, you might try scrubbing one part with pumice before putting it in the pretreatment line, just to rule out the possibility of the cleaning still being inadequate.
Usually, salt spray testing is supposed to be done or individual components before assembly. Are you sure you are required to pass 700 hours on assemblies consisting of two different metals?
Luck & Regards,
Ted Mooney, P.E. RET
Striving to live Aloha
finishing.com - Pine Beach, New Jersey
⇩ Related postings, oldest first ⇩
Q. We perform powder coating on two-wheelers fabricated components. I have tested those components for neutral salt spray & for humidity test. Most of the time salt spray test fails at welded & drain hole areas in 200 hrs whereas my required range is 700 hrs. The same components pass humidity 168 hours.
What will be the measures to pass salt spray test over such areas?
Powder coating plant employee - Aurangabad, Maharashtra, India
February 18, 2009
? Bit more info required here.
What metal is the substrate?
What pretreatment are you using?
What type of powder?
Curing parameters?
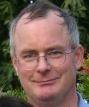
Geoff Crowley
Crithwood Ltd.
Westfield, Scotland, UK
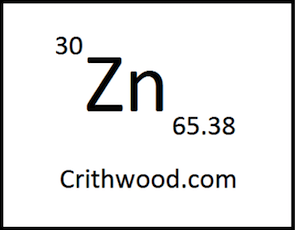
A. I can only presume no pre-treatment is carried out... because you don't state that it is, in your post.
Normally, to carry out the salt spray resistance testing of a coating requires that the coating is scribed (cut) down to the substrate.
As for powder ... again we have to guess that it's a polyester, has no resistance to rust creep once it is damaged and the substrate exposed. For examples of the damage caused to an untreated substrate and those correctly treated (if corrosion resistance is desired) see the page in ASTM B117 that illustrates this.
Birmingham, United Kingdom
Q, A, or Comment on THIS thread -or- Start a NEW Thread