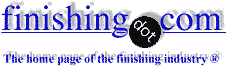
-----
Can bronze similar to SAE62 be TiN coated or is the process temperature a concern?
One customer has many thin-walled sleeve-shaped ejectors for all of his plastic injection molds that are made out of bronze (similar to SAE63) and hard coated. They constantly slide against other hard steel parts. Lubrication is not possible and tolerances are tight. Bronze is selected due to its softness and lubricity in order to keep sliding even when its coating is lost. It also will break preferentially in case of a dismal accident with minimum damage to other expensive components. The actual coating is a proprietary thin chrome deposit which is expensive and not locally available. They are looking for suitable alternatives that will exhibit good wear and do not produce excess lose particles which would contaminate the product. Plain EN is not good enough and heat treatment could compromise tight tolerances. I know composite EN+PTFE but am afraid it will lose an unacceptable level of residue. I was thinking about TiN or TIAlN but was told that the bronze would soften or melt at processing temperatures. Is it so? Isn't there a low temperature PVD available? Thanks.
Guillermo MarrufoMonterrey, NL, Mexico
February 16, 2009
We've been able to coat bronze with TiN and ZrN. We tried TiAlN, but it wouldn't stick at all. You have to lower the deposition temperature to do it, and this added too much stress to the TiAlN.
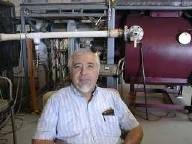
Jim Treglio - scwineryreview.com
PVD Consultant & Wine Lover
San Diego, California
February 18, 2009
Thanks, Jim,
I'll call back my local vendor to try to make them change their mind. By the way, how thick were those TiN and ZrN layers?
Monterrey, NL, Mexico
February 23, 2009
We were in the normal range -- 2 to 4 microns. One issue we did see was bubbling on cast brass parts. When they cast the brass, they sometimes wind up with voids. During the deposition process, the gases expand. If the void is near the surface, it will leave a bubble.
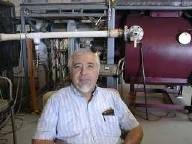
Jim Treglio - scwineryreview.com
PVD Consultant & Wine Lover
San Diego, California
February 25, 2009
Q, A, or Comment on THIS thread -or- Start a NEW Thread