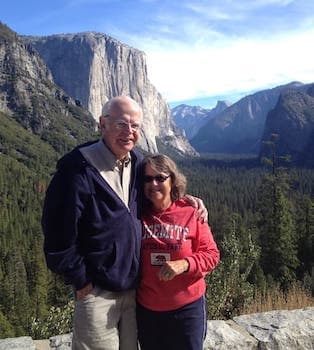
Curated with aloha by
Ted Mooney, P.E. RET
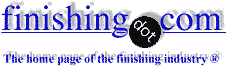
The authoritative public forum
for Metal Finishing 1989-2025
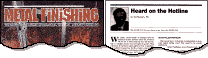
-----
Friction material for spoon brake on rubber wheels
I am old guy (retired Biochemist, freelance watch and clock journalist and Birdwatcher) with a mobility scooter. It's a great scooter but the brakes scare me. They are an aluminium pad, tangential to the tread pulled on with a cable. The usual bicycle arrangement at the hand end and 1:1 leverage at the tire. Views of rear wheel brake of mobility scooter taken from below.
With the wheel in place shows the cable which pulls on the aluminum brake shoe (about an inch wide). In the other picture the wheel has been removed and the entire brake shoe is seen.
After very little use it is already abraded by grit. I can redesign to double the leverage but would like to introduce a friction material. It is hard to keep control on even gentle slopes when the tires are wet. I have access to a machine shop and a competent engineer.
Timothy Treffryhobbyist - Sheffield, UK
February 12, 2009
Spoon brakes are perhaps the oldest form of friction brakes and were supposedly invented by a Scottish blacksmith by the name of MacMillan.
So much for the history lesson.
Regarding a friction material producer, many of the large scale producers are not interested in low volume niche applications; however, you have a company in Sheffield that may be of interest. The company is able to bond thin layers of friction material to various metal surfaces; I would suggest searching for friction marketing.
Another option would be to investigate mail order friction materials. Here in the states, McMaster-Carr supplies sheets of different materials that could be purchased and bonded using conventional epoxy adhesive
⇦ this on
eBay
or
Amazon [affil links] s. (Loc-tite materials are very effective.) Try to specify an adhesive that is suited for phenolic to metal combinations.
Best of luck,
[last name & city deleted for privacy at request] North Carolina
April 8, 2009
April 13, 2009
Thanks.
I'll follow up this suggestion - but you don't suggest a material. I have wondered if a glass-hard steel bar, 10mm triangular in section applied across the tread (corner rounded off) would work - relying on distortion of the wheel to act to assist the breaking force.
Best wishes
Timothy Treffry
hobbyist - Sheffield, UK
April 14, 2009
Timothy,
Sorry for the confusion.
The use of a conventional friction material would provide a means for a sacrificial element (i.e. the friction pad would wear more readily than the tire (oops, tyre.))
By using hardened steel, the wear resistance would be vastly improved over aluminum (oops, aluminium.) One point of merit is that wet friction between rubber surfaces and metallic surfaces is often not exemplary. In many cases, the use of any fluid will prevent effective contact and thus the braking forces will be dramatically reduced.
A suggestion might be to provide a transverse channel (edges smoothed / rounded) in the center of the steel friction surface. This would allow a transport pathway for any thin film of fluid or debris that may be present at the metallic friction surface to flow away from the interface. (As you have mentioned, any sharp edges will function as a knife edge and effectively shave the surfaces of the tyre.)
Good luck,
With kindest regards,
[last name & city deleted for privacy at request] North Carolina
Q, A, or Comment on THIS thread -or- Start a NEW Thread