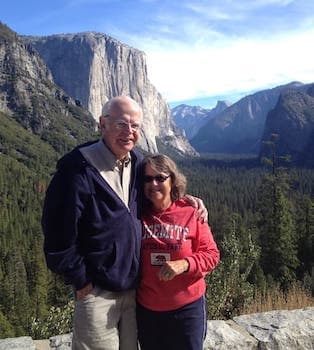
Curated with aloha by
Ted Mooney, P.E. RET
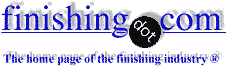
The authoritative public forum
for Metal Finishing 1989-2025
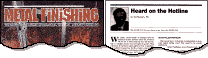
-----
Iridite 17P and RoHS compliance? Stop oxidation of copper & brass
Q. I am looking for the current process for chromate conversion coat over copper: either Iridite 17P Mix B or Iridite 8P Mix C-3. Is this still offered or is there an updated acceptable similar?
Mike Jones- Boston, Massachusetts
August 5, 2021
A. Hi Mike. I don't see any reason to believe that they are still available, but check with your Macdermid/Enthone rep.
As for 'acceptable similar', if it's your own product, it's up to you to decide what is sufficiently similar to be an accepted alternate; but if someone else specified it, you probably realize that you have to trace back to who that is, and have them sign off on a substitute -- no such thing as 'accepted alternate'.
A hard-on-the-eyes buy legible technical data sheet for Iridite 17P from 1954 is available from tmcHistory.org.
Luck & Regards,
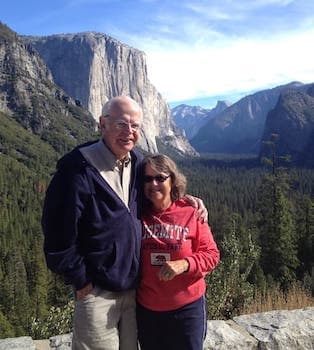
Ted Mooney, P.E. RET
Striving to live Aloha
finishing.com - Pine Beach, New Jersey
⇩ Related postings, oldest first ⇩
Stopping oxidization of brass plated steel wire
Q. We have a problem with oxidization on brass plated wire (diameter range from 1.48 to 2.20.)Brass plating is done in a cyanide solution with 3 subsequent demineralized water rinses. PH of the last rinse is controlled below 10.5. No known changes have been made to the process. Brass coating is in the range of 3.9 to 4.4 gr. per kg.
After a few days of storage, the colour changes from yellow to brownish with some spools even becoming strongly oxidized (black/brown). Some spools show even a very strange oxidization pattern with the turns near the right and left flanges of the metal spools (approximately 10 cm large on each side) being only slightly oxidized and the turns in the middle of the spool being very oxidized.
We encounter tremendous drawing problems(die wear & breaks) on those spool. We encounter also drawing problems on spools taken directly from the Plating Line to the Drawing.The 1.48 mm wire drawn to .250 mm is mostly affected.
There is no evidence that the problem is related to any changes of the atmosphere where the spools are stored as some spools plated weeks before and stored in the same area don't show any oxidization.
We suspect that the quality of the brass layer is different but we can't correlate it with any process parameter. (Cu, Zn, CO3, CN concentrations & temperature of the bathes and rinses controlled within the same specifications as before the problem was occurring. CO3 has recently however slightly increased from 100 g/l to 115 g/l. In the past, we didn't experience however similar oxidization problems with CO3 being at that level. Free Cyanide is normally controlled at 0 to -10 g/l
Has anybody experienced a similar problem and has found the cause or does somebody know what could cause this oxidization? We would highly appreciate your input.
Josy Blummfgr of tire cords - Hovelange, Luxembourg
2003
A. Dark spots indicate porosity in the brass. Plating solution is entrapped in the pores only to bleed out later. Hot and cold rinsing may help after plating, using a surfactant in the hot water. A hot water rinse before plating often helps by drawing the hot water into the pores preventing plating solution from entering. Also, a chromate conversion coating after plating is very helpful by neutralizing the cyanide and alkaline materials from the plating solution and providing a protective coating to prevent tarnishing. chromate processing solutions are available for copper from several suppliers, Macdermid,( Iridite 7, 7p or 17P,Atotech, and others. I have successfully used these chromates to solve spotting problems in brass and bronze items.
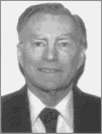
Don Baudrand
Consultant - Poulsbo, Washington
(Don is co-author of "Plating on Plastics" [on Amazon or AbeBooks affil links]
and "Plating ABS Plastics" [on Amazon or eBay or AbeBooks affil links])
Don,
Thank you very much for your effort to respond to my question. Your input has reassured us to focus all our efforts on the optimization of the brass plating process. We believe to have identified the main cause of the problem encountered : Neglect of brass solution turbulence in the bathes. We have optimized (increased) the turbulence in the bathes and we no longer see any oxidization on the plated wire. Wire is also again much brighter as compared to the dull surface we had seen before. Die-wear and breaks have been significantly reduced. But we might improve even further in the future and we will surely try some of the optimization ideas you have mentioned.
Thanks one more & best regards.
Josy Blum [returning]- Hovelange, Luxembourg
A. We produced about 130 t/week of caustic cyanide brass plated wire for hose reinforcement at National-Standard in Kidderminster, England. There are many factors to be considered in cyanide plating; wire cleanliness prior to plating, the plating operation, wire cleaning/washing after plating and wire storage.
If you were observing dark spots and rapid oxidation of the wire after plating there is a very good chance that not all of the cyanide is being removed.
Do you monitor CN contamination of the final washes. Are these hot washes. What type of water are you using. What is the turbulence in the washes like?
Regards......
Neil Beard- Stourport, Worc, England
Q. Is the chromate conversion coat used over silver plating, ASTM B700, RoHS compliant?
February 11, 2009Mark Schwan
product designer - Rochester, New York
A. Hi Mark. In the old days it surely wasn't. Sometime in the future it almost surely will be.
For the present I think you'll need to find out from your plating shop exactly what chromate conversion coating they are applying because both hexavalent and RoHS-compatible are probably available to them.
Luck & Regards,
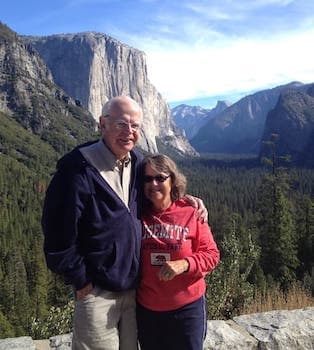
Ted Mooney, P.E. RET
Striving to live Aloha
finishing.com - Pine Beach, New Jersey
Q. Where or how can I get an MSDS or SDS for CHROMATE COMPOUND equivalent to IRIDITE 17P immersion solution?
Wilhelm GrevelJMC - McAlester, Oklahoma, USA
February 1, 2018
A. Hi Wilhelm. Iridite is a MacDermid-Enthone trade name, so you will have to start at macdermidenthone.com. Unfortunately, that info isn't available on the open www anymore. Macdermid, like many others, have moved to a system where you'll need to register before you can see stuff. Finishing.com was the first website in the world in the finishing industry, and it seems we're on track to become the last openly accessible one :-)
Regards,
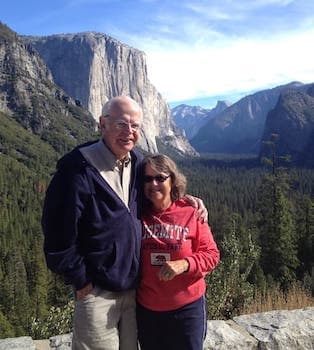
Ted Mooney, P.E. RET
Striving to live Aloha
finishing.com - Pine Beach, New Jersey
Q, A, or Comment on THIS thread -or- Start a NEW Thread