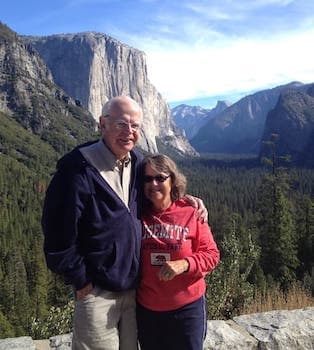
Curated with aloha by
Ted Mooney, P.E. RET
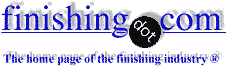
The authoritative public forum
for Metal Finishing 1989-2025
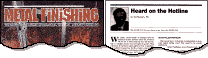
-----
What type of barrel do you use to Cadmium plate washers to prevent them sticking together
Is there some special Tumbler to use that prevents washers from sticking together in Cadmium
Kevin Huygheproduction manager - Warren, Michigan
February 11, 2009
First of two simultaneous responses -- February 12, 2009
You have definitely found the most common problem when plating washers in any electrolyte. Most platers prefer the "dimpled" polypro barrel or similar. This means that the inside of the barrel panels have small raised areas/recessed areas - they are not totally flat. One manufacturer makes a round cylinder barrel with "breaker bars" welded to the inside. Some platers will mix parts so that the non flat parts inhibit the tendency of the washers to stick together. If you have different production lines with different size barrels you may find that some sizes work better than others (my experience has been that 16" dia is better but this is not really proven). You may also want to try varying load sizes to increase the tumbling action in the barrel.
An old trick was to put a broomstick diagonally in the barrel to break up the mass as the cylinder rotated. Nowadays some people do this with polypro rod.
One further note - if your cad process does not use a surfactant ask your supplier for one. The reduced surface tension may help.
process supplier - Great Neck, New York
Second of two simultaneous responses --
Kevin,
You could use a media or what we call shot. I don't know the size of the washers so I couldn't say what size shot. The round "BB" like balls help keep the washers from sticking together. You can get them in metal or a plating on plastic type. A poly pro separating screen can be used at the end of the plating or drying cycle. When the shot plates up too high (increased surface area), they can be stripped and used again. Of course you will have to add the shot in figuring total plating surface area, and your production load will be cut some. Good Luck!
Fellow Plater - Syracuse, N.Y.
February 12, 2009
Cadmium can be mechanically plated; in that process the glass beads (impact media) prevents part-to-part contact. The deposit is matte and the plating process is free from hydrogen embrittlement.
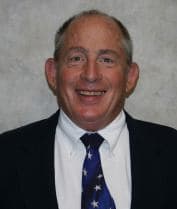
Tom Rochester
CTO - Jackson, Michigan, USA
Plating Systems & Technologies, Inc.

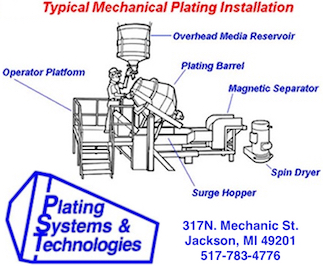
February 13, 2009

Q, A, or Comment on THIS thread -or- Start a NEW Thread