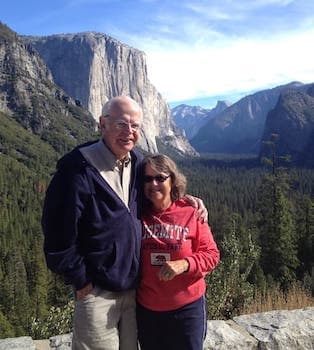
Curated with aloha by
Ted Mooney, P.E. RET
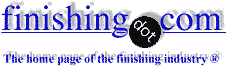
The authoritative public forum
for Metal Finishing 1989-2025
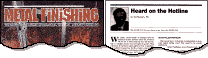
-----
Electroless nickel plating on steel
What kind precautions do we need to take to reach 96H salt spray on electroless nickel plated steel axles with a welded flange.
Preparation ?
layer thickness ?
% phosphorus ?
Others ?
Buyer, product designer - Belgium
February 10, 2009
Hi, Marc. I think the readers will be able to help you more effectively if we delimit the problem to your own situation rather than trying to address all possible hypothetical cases. Are you presently doing the operation? How many hours are the axles successfully enduring. Is there a problem in a particular area (the weld zone)? What type of steel? Does the problem appear to be porosity or peeling? Thanks!
If you have not attempted it before, I'd suggest starting your experiments with conventional electrocleaning and acid dipping followed by .0005" of mid phos electroless nickel. Good luck.
Regards,
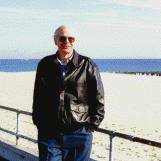
Ted Mooney, P.E.
Striving to live Aloha
finishing.com - Pine Beach, New Jersey
February 11, 2009
I think that you will end up using closer to 0.0015" of mid phos EN. I hope that the part will fit in the salt spray cabinet or you will have to use coupons and I sort of doubt if they will adequately represent the part, especially if it is large and would require turning during the process.
James Watts- Navarre, Florida
February 12, 2009
February 16, 2009
Hi Ted, thanks for your swift replay and your hints.
I'll try to be more precise, the corrosion problem appeared on electroless nickel plated axles with al welded flange and made out of steel 20CrMnTi , after a few days in open air.
De oxidation appears mostly on the welding but also on the axle itself. The oxidation problem appears to be porosity.
The layer thickness of the nickel is now about 0.00033"
- Belgium
Marc,
I am not personally aware of any major vendor of EN solutions that would say that 3 tenths is enough thickness to prevent rust. Most will say an absolute minimum of 1 thou and most will not agree that 1 is enough on welded areas.
- Navarre, Florida
February 16, 2009
Dear James, are you sure about a layer thickness of approx. 0.0015"? Ted is mentioning 0.0005"", that's 3 times lesser.
Marc Demeulemeester- Belgium
February 20, 2009
February 20, 2009
Hi, Marc. I suggested that you start your experiment with .0005" before you revealed that you were already doing electroless nickel plating at .00033". So .001", which is probably the most common thickness, would be a better 2nd try than a minimal bump from .00033 to .0005.
Regards,
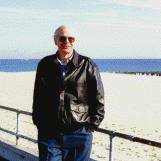
Ted Mooney, P.E.
Striving to live Aloha
finishing.com - Pine Beach, New Jersey
February 20, 2009
Hi Marc,
Over a number off years, I bought EN from 3 different vendors as well as a home brew. The figures that I used were recommendations from the vendors and tended to prove to be true when we did salt spray on actual parts when the customer insisted on 0.0005".
I used ironclad measurements and charged for the plate and the strip and the replate when it failed. I have had a few customers that did the measurements after plate and after strip in my shops. You can not argue with a failed salt spray and their own measurements.
- Navarre, Florida
Dear Ted, James, thanks a lot for your input. I believe this will be very useful for solving our problem.
- Belgium
February 27, 2009
March 2, 2009
For Mid phosphor you need at least 25 microns! But if it is heat treated after plating for hardness, forget about it!
I would recommend to try a high phosphor EN


Sara Michaeli
Tel-Aviv-Yafo, Israel
FOR 96 HRS SALT SPRAY I RECOMMEND TO USE A TWO LAYERS OF ELECTROLESS NICKEL 15 MICRONS OF HIGH PHOSPHORUS AND -15 MICRONS OF MEDIUM PHOSPHORUS AS OUTER LAYER.IF POSSIBLE YOU CAN ALSO PASSIVATE WITH SOME CHROMATIC SOLUTION
Ricardo BursteinBnei Berak, Israel
March 3, 2009

Q, A, or Comment on THIS thread -or- Start a NEW Thread