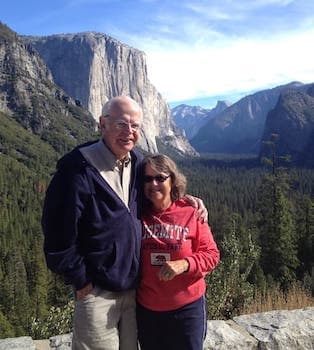
Curated with aloha by
Ted Mooney, P.E. RET
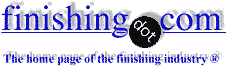
The authoritative public forum
for Metal Finishing 1989-2025
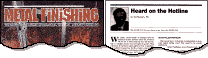
-----
Shadows in nickel electroforming
Q. While forming nickel plates (about 24" x 24" x 0.005") we get an irregular shadow on the surface. We can associate this with the pattern of the spray nozzles. Is there an off the shelf oscillating sprayer available? This should resolve the problem.
Fred Coxelectroforming shop - Lumberton, New Jersey, USA
January 14, 2009
A. I presume you are using sprays to rinse down your workpiece as it comes out of the nickel bath. There are oscillating sprays available, but whether they can be retro-fitted to your line I don't know. I suggest you talk with the plant manufacturer. I also presume that manual spraying is out of the question?
On the other hand, if you are using spray jets to agitate the nickel bath, then you have another problem; the jets are too aggressive, so just run down the electrolyte flow rate. You can also try using adductors - they are quite good now.
My next thought is why is marking the nickel - are you using pure water or is it contaminated? All rinsing should be done with pure water, never tap water. There is a lot of knowledge in rinsing technology, but not enough room here to give it all! Maybe your rinse water is too low or too high pH?
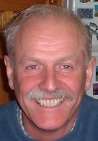
Trevor Crichton
R&D practical scientist
Chesham, Bucks, UK
January 29, 2009
Q. Dear Trevor, Thanks for your input. The problem is in the nickel bath. I am going to reduce the spray volume and will let you know the results. If this is the issue, why is it inconsistent. Appears for a while, then goes away, then reappears. Related to our adding NTSA? or other chemicals required?
Fred Cox- Lumberton, New Jersey, USA
February 2, 2009
What is the function of the spray nozzles and why are they used during electroforming? Normal solution agitation, mechanical, pump or air should provide all of the solution movement required for good uniformity of deposit
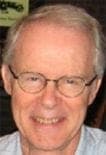
supplier
- Lake Zurich, Illinois USA
January 30, 2009
Try a cathode bar agitator to move the part back and forth while electroforming is in process.
Russell Richter- Danbury, Connecticut, USA
February 2, 2009
February 2, 2009
To answer both points above:
Dayton, there are two types of spray nozzles. The first is used to rinse off the parts as they leave the plating bath and puts the rinse water back into the plating tank, thereby minimising the loss of chemicals through dragout. Using these nozzles for rinsing requires the use of pure water as the rinsing medium.
The second type is also known as an eductor and is used to agitate the bath where conventional carrier bar movements are either not practicable or are insufficient. The use of adductors also removes the need to move the carrier bar. They work by having both the inlet and outlet to the filter pump submerged in the plating bath; they are analogous to a submersible filter pump in a tropical fish tank. Since the bath is moved around without the surface being broken, you can use foamable wetting agents and not produce buckets of foam! The down side adductors is that they need to be set up properly or you will get over-agitation is some parts of the tank and stagnation in others. The technology has been very well researched by a guy called Professor David Gabe - look in the technical literature for his works.
Fred; additives work by altering the chemistry in the Helmholz double layer; this zone controls the transfer of metal ions to the cathode surface where they are reduced to metals. The thickness of the double layer is important in allowing the additives to do their intended job (brightener, leveler, hardener etc). If the double layer is disrupted, the additive cannot do its job. Hence if you have the electrolyte being squirted at the workpiece at a (relatively) high velocity, the double layer is broken down. This has two major effects, firstly it allows greater metal deposition rates because the cathodic surface does not get depleted of metal ions, which can be an advantage, as in jet plating, but it also stops any additives doing their job, which can be a disadvantage.
The term "shadowing" suggests to me a discoloration that could be caused by a change in the structure of the deposit and be the result of additives (say brighteners) not doing their job. This effect would be almost random, depending on where in the tank, relative to the adductors, the workpiece is and at what velocity the solution hits the workpiece. Obviously the effects of screening (either accidental or deliberate) will affect the impact velocity of the electrolyte and its subsequent effect on the deposit. Hope this helps.
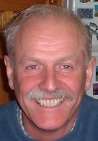
Trevor Crichton
R&D practical scientist
Chesham, Bucks, UK
Q, A, or Comment on THIS thread -or- Start a NEW Thread