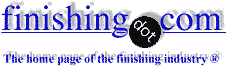
-----
Black Hardcoat problems
January 23, 2009
I am processing hard black on cylinder type which is A5052 series sanded by sandpaper (#1000).
Flow of process
1. oil off = 20~40 mins = 60 degrees
soaked in wash tank then spray it with cleanse salted water
2. caustic etch = 1~3 mins = 45 degrees
soaked in wash tank then spray it with cleanse salted water
3. de-smut = 5 sec. = room temperature
soaked in wash tank then spray it with cleanse salted water
4. anodizing tank = 45 mins = 10 degrees = 10 volts = 1.200 baumé
soaked in wash tank then spray it with cleanse salted water
5. Black tank (made by Clariant) Aluminum black BMW = 20 mins. = 60 degree = 5.4~5.5 ph
soaked in wash tank then spray it with cleanse salted water
6. Sealing = 20 mins = 70~90 degree = 5.1~5.2 ph
soaked in wash tank then spray it with cleanse salted water
7. dry by electric compressor air
finish
after anodized on sulfuric the color seem to be nothing happens still looks like a bare aluminum material not the others really looks different Goldish or greyish.
then black processed is next.after soaking for about 20 minutes the cylinder type material on its surfaces become rough and looks like a bubbles not quite the same output when am processing normal black process which is 20 degree = 60 mins. = 11 volts and on black
20 minutes = 60 degree = 5.4~5.5 ph reading.i have been testing it for several times to solve this problem but seem to be am missing some point......
Please..if you have some advices that I can maybe use please don't hesitate.
Anodizer - Philippines
First of two simultaneous responses -- January 27, 2009
First, hard anodizing is done at 32F and at a much higher voltage.
You are fortunate to get any anodizing at 10 volts. Even 12 or 13 volts will not perform well. I like 18V as this allows you to put on the coating faster so the acid solution is not eating as much of the anodize off because it is in the tank a shorter period of time. I did not use your dye, but the pH seems to be a bit low, but if that is what is called for, that is what you need.
Basically, you need a thicker anodize coating, which equals a higher voltage.
- Navarre, Florida
Second of two simultaneous responses --
What is "salted water". If is is sodium chloride, that pits aluminum, especially the 5000 alloys. The anodizing solution has what free acid (baumé does not work) we need to know the titrated free acid AND the dissolved aluminum. 10 volts is too low, forget the voltage, we want 24 amps per square foot. the voltage has to go up to hold the current against the building resistant coating, about 30 volts for 0.0015 and 60 volts for 0.002. What is the dye tank made of: stainless steel or plastic? Are you racked on titanium or aluminum.
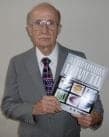
Robert H Probert
Robert H Probert Technical Services

Garner, North Carolina
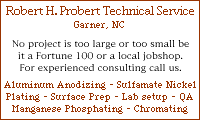
January 27, 2009

Q, A, or Comment on THIS thread -or- Start a NEW Thread