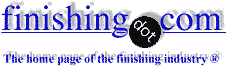
-----
Blisters in Anodic Coating
Aluminum alloy 7075 parts with about 0.003 in. thick anodized coating have small blisters in the coating after sulfuric acid anodizing . The blisters appear to be randomly located on areas with flat surface topography and are about 0.008in. in diameter.
Microscopic examination and cross sections show a fracture in the coating propagating from near the substrate surface at an angle out through the coating. The fractures appear to start from a small bump remaining on the substrate surface.
I suspect residual stresses in the coating are a factor, with local stressed areas due to anomalies in the coating from the intermetallic inclusions in the aluminum. Likely? Unlikely? Any suggestions for possible causes for these blisters would be greatly appreciated?
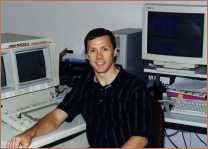
Larry Hanke
Minneapolis, Minnesota
2000
Hi Larry, I had a gentleman from Lockheed-Martin contact me about this same problem. I asked for pictures of the bad areas and I could have figured it out. It basically ended up being that the coating would "bubble up" in areas. I basically have to agree with you on that aspect because they said the parts were very clean surface wise.
If that was not it my only other guess without seeing the parts was some sort of localized burning. I get this sometimes with smaller 7075 (smaller than a fingernail) and trying to "stuff to much current into their little throats :-)". Its a blistering that has to be mechanically polished away because just stripping the parts does not solve this and it could be attributed to the constituents moving closer to the surface and causing this problem. Because actually now that I think about it, 2 guys do this same part, one company has this problem, the other doesn't and it has to do with the way they polish the surface to a shine.
- Toledo, Ohio
2000
Larry, The microscopic examination you performed on the cross sections showed a fracture in the coating propagating from near the substrate surface at an angle out through the coating. This fracture may have been caused by corrosion beneath the substrate or on its surface. A few questions for you, was the material used certified? where was it stored and for what length of time? are your rinse tanks clean? i.e., pH's neutral. What amperage was used and was it stepped up slowly? What is the concentration of your Sulfuric bath? Do you use any additives?
Michael A. Von Rembow- Auburn, California
2000
Q, A, or Comment on THIS thread -or- Start a NEW Thread