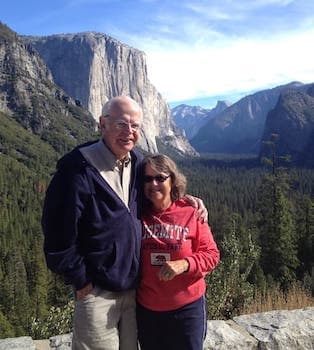
Curated with aloha by
Ted Mooney, P.E. RET
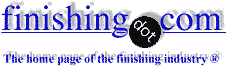
The authoritative public forum
for Metal Finishing 1989-2025
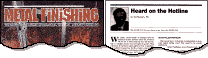
-----
Phosphating rinses. Allowable TDS levels in phosphatizing operations
Q. Hello readers,
I am a project manager trying to optimize a five stage metal phosphatizing operation. I cannot find in literature anywhere what recommended conditions are concerning the TDS levels for each tank. I want to save water but our tanks get dirty very fast and interferes with our ability to read concentrations, as we use conductivity probes.
Any suggestions? Thanks!
- Princeton, Minnesota
2000
A. Dissolved solids comes from many sources and all are not equal in the effect that it has on your process.
You will probably have to establish what you can live with by keeping records and using that to establish limits.
Small RO systems with proper pre-filtration and membrane selection would allow you to upgrade the quality of your rinses and allowing the reuse of a high % of the rinse water.
If you had the tank space for storage of water to be treated and another for treated water, a small unit could run all night and on the weekends, rather than a larger unit running in real time. I do not sell or install this type of equipment.
- Navarre, Florida
2000
A. Amanda,
Assuming you are operating a conventional 5-stage spray process with alkaline clean - rinse - phosphate - rinse - seal stages, a general guideline for maximum TDS levels in the rinses is, for stage two, 500 - 750 ppm and for stage four, 250 - 500 ppm. If you have relatively soft incoming water, of say 100 ppm, use the lower numbers stated, and if you have relatively hard water, of say 300 ppm, use the higher numbers.
If you are trying to save water, one way is to use a fresh water riser where the fresh rinse water is introduced through a riser in the vestibules after the rinses, about halfway between the end of the rinse stage and the peak of the drainboard. If you are running an immersion process, disregard the fresh water exit risers! By the way, you can also automatically control your rinse stages with conductivity (TDS). Good luck! Gary Nelson
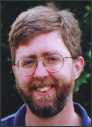
Gary Nelson
Berkeley Heights, New Jersey
2000
A. If you are talking about your rinse tanks, James and Gary have covered it fairly well. I would just add that if you are looking for a "spot-free" rinse you'll have to keep the final rinse water below around 50 ppm or use the rinse halo described above.
If you are using conductivity probes to control your chemical concentration you are working with a compromise. Conductivity measures everything in the solution, including the stuff you don't want, so your reading will not reflect the true concentration of chemical in the tank, nor will it tell you the amount of free acid. A line with a consistent work-flow and consistent usage, drag-out, and water TDS can be controlled using conductivity, but a titration should be done periodically to confirm that things are the way they should be. Conductivity readings are pretty on a control sheet but are not enough to run a quality phosphating system without constant calibration and backup checks.
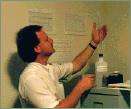
Jeff Watson
- Pearland, Texas
2000
A. Amanda
TDS / Conductivity ratios on various brands of meters can differ....make sure you understand your meters actual cross-linking ratio percent prior to calibrating or setting your total dissolved solids parameters for each tank.
My understanding is that you are curious on the iron phosphate stages TDS as well as the rinses. On your iron phosphate tank numerous other factors can figure in however best results I see usually fall in a range of 3,500-9,000 mmhos for CRS and HRS parts, approx. 4,500-7,500 for cast iron.
Wastewater concerns have a ceiling of 20,000 mmhos and you will pick up @ 10% more mmhos / TDS in a traditional hydroxide precipitation wastewater pretreatment ....this would make your bath ceiling closer to 17,000 if wastewater concerns could be a issue in your area / application. Prior answers on the rinse stages could be good starting points along with actual final results from finished parts analytical testing.
Ideally you should be "turning over" your rinse stages once every eight production hours. Alkaline stages will sometimes have readings that can skyrocket and various filtration and adjustments / changes in nozzle size, psi and spray pattern can help you avoid "souping" up this bath stage with unnecessary high amounts of alkaline cleaners that could be hard to rinse off or contribute to excessive carryover into your rinse stage. Check direction of your vestibule misters and check daily additions and times / causes for additional water going into the each stage. Could you have some racking or inadvertent spray issues, parts being trapped in stages on breaks, etc. ?
- Sioux Falls, South Dakota
2000
DI rinse bath recycling
Q. We have a tri-cationic phosphatizing line with non-chromic sealing. I have my phosphatizing on step #4 , DI rinse on step #5, non-chromic sealing on step #6 and finally a DI rinse on step #7.
I need to keep my #5 and #7 DI rinse bath below 30 microS ... is it possible to recycle some of the water? if so, what method is best suited?
My incoming DI water is approx. 5 microS. Trials we've performed, we were able to maintain such quality by dumping 2-4 gpm on step #7 and 6-8 gpm on step #5 ... main goal is to maintain DI rinse bath below 30 microS while recycling some of the water.
The process is done in spray booths/cabins.
Any help, info, tips would be greatly appreciated.
water treatment - Mexico
February 25, 2016
A. Hi Gonzalo. Usually, DI water is used in rinsing to minimize cross-contamination and to improve the quality & finish beyond what is obtainable with city/well water. For example, DI water is often used as a final rinse to reduce the salt stains that occur from city/well water drying on the parts.
If I am understanding you correctly, your DI systems are delivering 5 microS water, which is being mixed with a reservoir of recycled water until the contamination reaches 30 microS, 6x the TDS of the incoming DI water. You are able to hold this level by dumping 2-4 GPM and 6-8 GPM in the rinse stages.
I don't think I'd do it that way because you're not getting the benefit of rinsing with 5 microS water (you're rinsing with 30 microS water), and you're also dumping water of only 30 microS. Rather, I'd continually pass all of the reservoir water through the DI cylinders. If they can't take the flow rate, then you can pass a slipstream through them instead. Then, when you regenerate and backwash them, that effluent will be far more concentrated than 30 microS, so you'll be using far less water.
The red flag to be heeded, however, is that while you may presently be able to regenerate DI cylinders without a permit, or ship them offsite without a permit, because they were only used for city/well water, now you'll be using them on what may be classified as hazardous waste.
Regards,
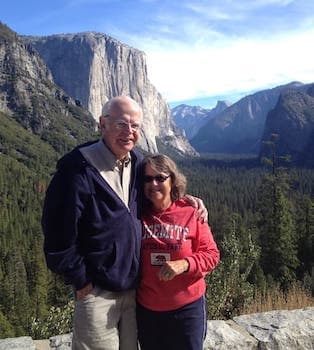
Ted Mooney, P.E. RET
Striving to live Aloha
finishing.com - Pine Beach, New Jersey
February 2016
![]() |
A. With rinse conductivity at 30 uS, DI recycling is the preferred way to recycle this water. There are probably over 100 facilities doing this today. Consultant - Cleveland, Ohio USA March 9, 2016 Q. Actually I have an incoming DI water line coming into the spray tanks, and water is recirculated in those tanks. We are thinking of putting an ion exchange system to recirculate water in those tanks in order to keep the conductivity below 30 microS but at the same time to avoid dumping those 10-12 gpm coming from the original DI water line. - Mexico March 2, 2016 |
A. There is no problem in recirculating a mix of new and recycled DI water. This can be done with mixed bed IX tanks or with a system that regenerates on site with simple conductivity control. The regenerations should be treated due to the elevated concentrations of heavy metals.
Lyle Kirmanconsultant - Cleveland Heights, Ohio
March 23, 2016
Q, A, or Comment on THIS thread -or- Start a NEW Thread