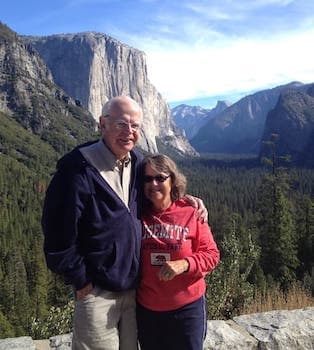
Curated with aloha by
Ted Mooney, P.E. RET
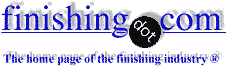
The authoritative public forum
for Metal Finishing 1989-2025
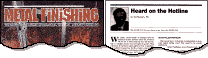
-----
Corrosion Resistance of Zinc Plating
Q. Hello guys,
Are my ideas correct about galvanized functions?
At the storehouse of the company I work, we got like 132 square G90 tubes with unappealing white rust, then I read a bit and understood the next:
Zinc coat needs to be oxidized slowly and in a certain non-aggressive environment to form through the time a stable oxide form to protect the tubes surfaces, but at the end of electroplating process (our process) we got the chromate passivation, that step just adds a temporary protection film of chromium insoluble oxides just to gain time to help zinc coating get oxidized in its stable form.
Is it correct?
Thanks for your answers in advance.
- México, Sinaloa
December 22, 2021
A. Hi Jorge. All of our theoretical understanding of processes like how corrosion proceeds, how zinc plating deters it, what chromate conversion coating does, etc., is a simplification. So I certainly hesitate to say that your understanding is incorrect :-)
But what I will say is that things gets very confusing when we try to simplify to such an extent that we consider hot-dip galvanizing of coils before fabrication, and zinc electroplating of coils before fabrication, and hot dip galvanizing of discrete parts after fabrication, and zinc electroplating of discrete parts after fabrication similar enough to generalize as if they were all the same thing. And it introduces semantic problems too: in the USA we don't call zinc electroplating "galvanizing", and no one should describe the thickness of the plating as "G90" (which is actually a measurement of the weight on both sides [inside & outside] put together.
Hot dip galvanizing of discrete components in always very thick and can often survive outdoors for 50 or more years. In this case you are certainly right that exposure to the atmosphere builds a glassy corrosion resistant skin, and the chromate quench wears off relatively rapidly. But zinc electroplating is a much thinner coating, is less suited to long outdoor exposure, and often involves a heavy chromate conversion coating that contributes substantially to its corrosion resistance; by the time the chromate wears away the life of the overall coating might be about half over.
"G90" means 0.9 oz/ft2 (counting both sides) and is equivalent to about 19 µm thickness, and it's a reasonably heavy coating for galvanizing of sheet metal, light for hot dip galvanization of fabricated parts, and pretty heavy for zinc electroplating. [plus rather meaningless]. In any case the 'white rust' is possibly "wet storage stain" which results from storage with too much dampness or not enough fresh air.
Luck & Regards,
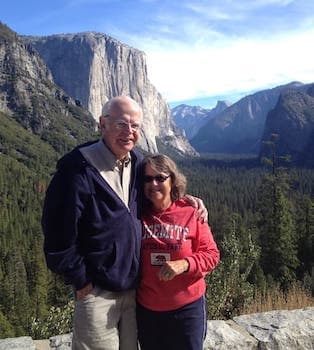
Ted Mooney, P.E. RET
Striving to live Aloha
finishing.com - Pine Beach, New Jersey
December 2021
Okay Ted thanks a lot for your answer!
Employee - Sinaloa, México
December 28, 2021
⇩ Related postings, oldest first ⇩
Q. I run a zinc plating operation. The question of corrosion resistance comes up often. In zinc plating, protection to white corrosion products is the function of the chromate. Protection to red rust is the function of the chromate plus the thickness of the zinc plate. ASTM B201-80 addresses corrosion resistance to white corrosion products. Is there any published information on corrosion resistance to red rust on zinc plate over ferrous metal with NO chromate post treatment?
Don P. [surname deleted for privacy by Editor]- Elkhart, Indiana
2000
A. Zinc and zinc alloy plating needs some sort of passivation, most often this is hex-chrome. I cannot imagine any part being zinc plated and NOT passivated after plating, so I do not think you will find that type of data around.
The zinc plate protects the base metal. The chromate protects the zinc plate. Once the chromate is overcome, the plating oxidizes resulting in white corrosion. Once the zinc plating is used up, the base metal oxidizes resulting in red rust.
There are different types of chromate passivates. Maybe you are wondering what the zinc plating's contribution alone and worry about the chromate's added benefit later. Well, this is not A + B = C. The chromate and the zinc plating act together to give more corrosion protection than either would achieve alone. You need to test the zinc WITH a chromate in order to yield useful information. This might mean trying out different combinations of chromate and plating, but that is the correct way to assess corrosion resistance.

Tim Neveau
Rochester Hills, Michigan
2000
A. Hello Don. I don't know where to get data for zinc plating with and without chromate, but I do know of some dealing with tin/zinc. Shahin, G.E. " Alloys Are Promising as Chromium or Cadmium Substitutes" from Plating & Surface Finishing 85(8):8-14;1998. Where tin with 20% zinc has a 25 fold increase in time to white rust and a doubling of time to red rust, under salt spray test with the addition of a chromate coating.
There may be some data on straight zinc with and without passivation, however I don't have it handy.
I seen zinc with chromate compared to zinc with a zinc phosphate conversion coating, though these were not tested to white/red rust. The paper is on the web, www.aappso.com/hazmat/AMSSV2/techref.htm [Ed. note: URL no longer works] there are a few papers there, this one is called "Preliminary Evaluation...Ion Vapour Dep'...." by Cramer, Ault and Hartline. Tim is right that there is an interaction between the chromate and the plating: though the zinc might well be oxidising it does not display the white corrosion product as quickly when used in conjunction with a chromate coating. I haven't answered really what you asked but I hope this has been helpful.
university - Glasgow, Scotland
2000
Q. Using this plating spec. ASTM B633-98; Fe/Zn 12, SC 3, Type I (.0005" zinc, as plated without supplementary treatment), any Idea what the corrosion resistance to red rust would be per ASTM B117 procedures?
Don P [surname deleted for privacy by Editor]- Elkhart, Indiana
2000
A. Hi Don,
I am sure that if you contacted the "Zinc Development Association" they would be able to help.
Have a nice day.

John Tenison - Woods
- Victoria Australia
A. Hi Don. MFSA's Quality Metal Finishing Guide for Zinc Plating (www.nasf.org) has this info. It is suitable only for "Mild - Exposure to indoor atmospheres with rare condensation & subjected to minimum wear or abrasion". Good luck.
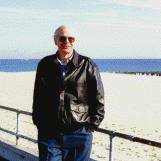
Ted Mooney, P.E.
Striving to live Aloha
finishing.com - Pine Beach, New Jersey
Q. Hi Don.
I too am suffering from a similar problem. Some authorities are debating that salt spray life of zinc plating (until white rust only) can be improved only by increasing the thickness of zinc layer. As you have studied more in this line, can you help me in this context. As far as I learned WHITE RUST LIFE can be increased only by changing the type of passivation and should be immaterial of thickness given. Please try to answer this. Thanks.
- Mumbai, India
2000
Q. Dear sirs:
I need to gather information on behavior of zinc plated parts regarding corrosion in different atmospheres. For example rate of zinc dissolution per year in marine and industrial atmospheres. Equivalency of neutral salt spray corrosion resistance in hours to years of life service. Corrosion behavior of zinc plated parts placed under potable water, etc. Is there somewhere I can access to obtain this kind of information?
Thanks in advance.
Oscar Infante- Santiago, Chile
2001
A. Hi Oscar. There are testing organizations which do extended outdoors testing of painting and plating for their clients, including NASA's "Corrosion Testing Laboratory" at Kennedy Space Center in Florida, and LaQue in Kure Beach, North Carolina. You might google those terms and either find the reports you need, or commission the necessary testing.
However, there is NO equivalency between neutral salt spray hours and years of service. Accelerated salt spray testing is a QA measure to help insure that a process has not gone out of control, but it bears little relationship to real life. Consider that there is no finish that outlasts hot dip galvanizing: in real life it can build an adherent, glassy, zinc carbonate skin with fabulous corrosion resistance; heavy galvanizing can last 75 years or more without maintenance ... but in a salt spray chamber the zinc just dissolves away as white rust. Trying to judge real life from salt spray endurance is like trying to guess an unseen person's weight from their height; there is the rough correlation that taller people will weigh more on average, but that's the whole extent of it :-)
Regards,
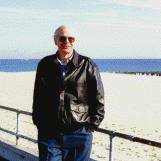
Ted Mooney, P.E.
Striving to live Aloha
finishing.com - Pine Beach, New Jersey
Q. I am in need of a detailed explanation about the following finish with the process data --
FINISH: ZINC CHROMATE PER ASTM B633, TYPE 3, SC3, CLEAR
service industry - India
2006
A. Hello, Karthik. ASTM B633 is a copyrighted specification, and you must start the process by obtaining a copy. You will see that we have hotlinked to one place on line where you can purchase and download it immediately. After you have the spec in hand, please get back to us with any specific questions. Thanks!
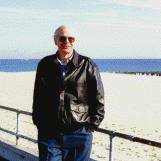
Ted Mooney, P.E.
Striving to live Aloha
finishing.com - Pine Beach, New Jersey
2006
How to prove our zinc plating was not passivated
Q. Hi! We ordered steel brackets with electroplated zinc and with no passivation! But the problem is that color changes from silver to yellowish! What could be the reason? How could I easy check whether they did passivation or no? maybe a I can induce white rust formation?
Inga NarkevicaMikrotik - Riga, Latvia
March 12, 2018
A. Hi Inga. Can you satisfy my curiosity, and tell us what application these parts will be used for and why you want them passivation free? As Tim says in the first response "zinc plating ... needs some passivation"; in my own experience, I don't recall ever seeing unpassivated zinc electroplating; and the MFSA Quality Metal Finishing Guide claims "practically all zinc coated steel is given a chromate conversion".
There are so many potential passivation possibilities, from hexavalent chrome to trivalent chrome to chrome-free proprietaries to water-soluble lacquers, that it might be difficult to verify the absence of every possibility. Which brings us back around to why they must be passivation-free ... because if you can tell us what the finish must achieve, it may be easier to prove that it achieves it than to prove that no type of passivation treatment of any sort was ever applied. Good luck.
Regards,
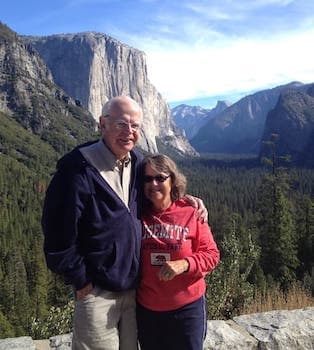
Ted Mooney, P.E. RET
Striving to live Aloha
finishing.com - Pine Beach, New Jersey
March 2018
A. I'd recommend that you take a look at ASTM B201-80. If a drop of lead acetate solution is placed on the substrate and it IMMEDIATELY forms a dark spot (finely divided lead metal formed by the reduction of lead in solution by zinc metal) there is no passivate present.
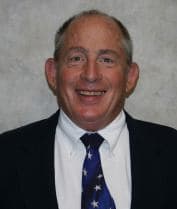
Tom Rochester
CTO - Jackson, Michigan, USA
Plating Systems & Technologies, Inc.

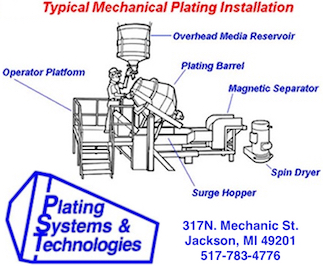
March 15, 2018
These are brackets for mounting wireless devices on the house walls, thus there is no special need for high corrosion resistance. But they should be RoHS compliant, so they cannot contain hexavalent chrome. However the colour of brackets changes from silver to yellowish. What could be the reason of colour change of the zinc. Is it some contamination of plating bath that affects Zn appearance?
We asked supplier why there is such colour change, but they said that is typical in Zn plating, they cannot control the colour in plating process. Also they have not done passivation of the brackets.
I did CuSo4 test and it turned black immediately, and after some time it turned red/brown - confirming Cu formation. It means that CuSo4 reacted with Fe. So it could mean that no passivation have been done!
- Riga, Latvia
March 19, 2018
We want to zinc plate but not do passivation
Q. Sir, we are giving Zinc plating and yellow passivation coating for suspension rod in load carrying application and what will affect if we remove yellow passivation and do only zinc plating, for salt spray of 168 Hrs
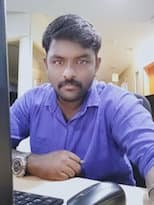
Manikandaprabu Janarthanam
- Neyveli T.S, India
August 27, 2019
A. Hi Manikandaprabu. You will not obtain even 12 hours salt spray resistance without chromate conversion coating. You can switch from yellow to clear without penalty, but you cannot skip the chromating.
Regards,
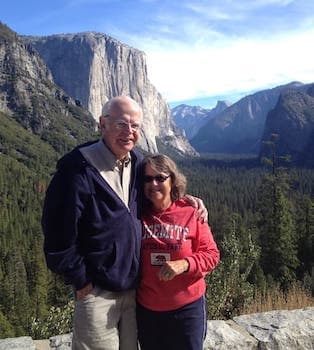
Ted Mooney, P.E. RET
Striving to live Aloha
finishing.com - Pine Beach, New Jersey
August 2019
![]() |
! Wow this thread was started in 2000; that was even before I was born.. Bob WillStudent - New York October 11, 2021 A. Hi. The first question on the site was posted on the Finishing Technology Hotline BBS in 1989 -- maybe before your teacher was born :-)
![]() Ted Mooney, P.E. RET Striving to live Aloha finishing.com - Pine Beach, New Jersey October 2021 |
Q, A, or Comment on THIS thread -or- Start a NEW Thread