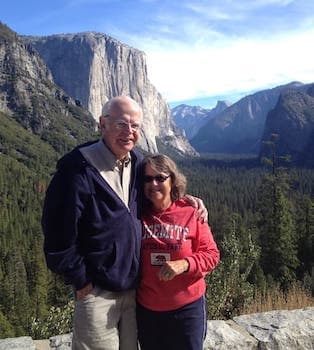
Curated with aloha by
Ted Mooney, P.E. RET
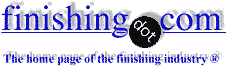
The authoritative public forum
for Metal Finishing 1989-2025
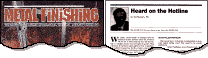
-----
Differences between nickel plating, zinc plating, and dip-spin coatings
Can you please advise me what are the difference of 3 types of plating, which are nickel, blue zinc and rainbow zinc.
What we know is that nickel is the best among these 3, in terms of anti-corrosion, but how do we measure. Is it by using salt spray test to ISO9227, or is there any other method that we can measure? Is there a common unit to tell the differences, i.e., can withstand 500 hrs salt spray test, etc.
Product Designer - Penang, Malaysia
January 8, 2009
Hi, Ang. Blue zinc vs. rainbow zinc is more a simple question of color than a question of "better". Zinc plated fasteners must receive a subsequent chromate conversion coating; in the old days the darker, yellower, coatings were thicker and more protective -- but the color doesn't imply much in these days of RoHS-mandated trivalent chromates.
Nickel plating is more expensive than zinc plating, and usually more aesthetically pleasing, but I don't think I'd call it "better" because zinc plating provides cathodic protection whereas nickel plating does not.
I doubt that any of the three will provide 500 hours of salt spray protection, and it wouldn't mean anything if they did. You may wish to consider an alloy plating like tin-zinc, zinc-iron, zinc-cobalt, or zinc-nickel, or another alternative like mechanical plating or zinc-rich dip-spin coatings. Good luck.
Regards,
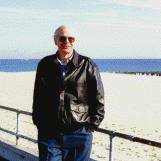
Ted Mooney, P.E.
Striving to live Aloha
finishing.com - Pine Beach, New Jersey
January 9, 2009
I have to select different type of fasteners with different type of passivations for the industrial machines e.g. screening machines. What is the difference between Dacromet and passivated fasteners. Describe the environment where Dacromet are preferred over passivated fasteners? What is clear zinc passivation. Also describe difference between clear, black and yellow zinc passivated fasteners and where particular type can be used? Also give cost comparison of different type of treatments? What should be the deciding factors among all the surface treatment?
Thanks & Regards
Product Designer - Lahore, Punjab, Paksitan
January 20, 2009
January 20, 2009
Hi, Anser. In the "old days", say 5 years ago, the color of the hexavalent chromate conversion coating (passivation) had significance: darker yellows indicated a thicker coating and hence more protection. As the world moves towards RoHS-compliant trivalent conversion coating, however, the color no longer means anything -- in many cases it's just dye.
These chromate conversion coatings (passivation) are applied to zinc electroplated finishes; and to various zinc alloy platings like zinc-iron, zinc-cobalt, zinc-nickel, and tin-zinc; and to zinc-rich dip-spin coatings like Dacromet.
Plain zinc electroplated finishes with chromate conversion coatings are among the least expensive finishes, but even there the cost is proportional to the specified thickness of the deposit. Alloy electroplatings cost more, as do dip-spin coatings. Generally, all of these are non-decorative, functional, corrosion-fighting finishes where you get about what you pay for, i.e., the inexpensive plain zinc plating is the least robust.
The answers to generalized questions fill whole shelves in technical libraries, so it is impossible to condense them to a couple of paragraphs. But you can get better help if you can describe the particulars of your own situation :-)
Good luck.
Regards,
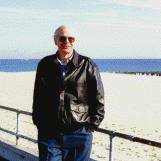
Ted Mooney, P.E.
Striving to live Aloha
finishing.com - Pine Beach, New Jersey
Q, A, or Comment on THIS thread -or- Start a NEW Thread