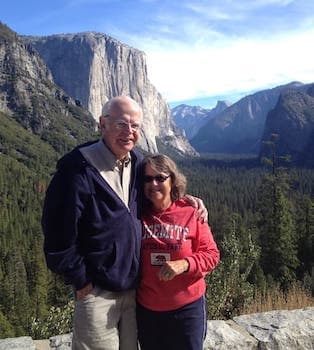
Curated with aloha by
Ted Mooney, P.E. RET
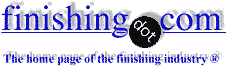
The authoritative public forum
for Metal Finishing 1989-2025
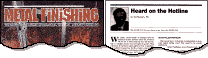
-----
Thickness of anodize coatings

Q. Hi,
I am starting an anodizing line and reading through the spec I have to get to 1000mg/ft2, but the spec doesn't tell me how to get that calculation. Also should I anodize the 3" x 3" test panels for Class 1 or Class 2 in order to hit the min required to follow MIL-A-8625? Any help would be greatly appreciated!!
Thanks,
David
Manager - Madison, Wisconsin
March 29, 2022
A. Generally, Type II anodizing to MIL-A-8625 gets .5-.7 of oxide. Type III 1.6 to 2.4 oxide. Are you working to Mil spec or a customer spec?
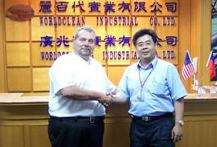
Drew Nosti, CEF
Anodize USA

Ladson, South Carolina
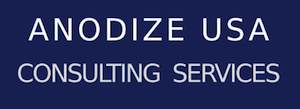
March 31, 2022
Q. Thanks for responding Drew, I appreciate it. I am trying to follow MIL-A-8625. I am using 3x3 panels so I am assuming to get my calculation of my coating weight I would need to take the difference of the two measurements (after anodizing and then the stripped weights) multiply it by 144 and then divide it by 18 to get my mg/ft2. But I wanted to confirm that with someone that has been in the industry longer than I have been.
David Franklin [returning]- Madison, Wisconsin
April 3, 2022
A. You can take the NADCAP auditor out of NADCAP but you cant take the NADCAP out of the auditor.
Here you go:
6.1 Measure the area of the coating. Do not include the area of cut edges or other uncoated surfaces
6.2 Weigh the test specimen before and after stripping the coating to the nearest 1mg
6.3 Immerse the specimen for 5 min in the phosphoric-chromic acid solution@ about 100C. Remove the specimen, wash in distilled or deionized water, dry, and weigh the specimen. Repeat this cycle until the coating is completely removed which is indicated by the weight of the specimen remaining constant.
Make sure you follow this "repeat part" or your results will be worthless
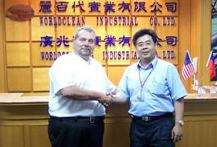
Drew Nosti, CEF
Anodize USA

Ladson, South Carolina
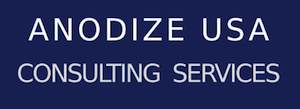
April 4, 2022
⇩ Related postings, oldest first ⇩
Q. We have a requirement to anodize parts that are pins per MIL-A-8625 / MIL-PRF-8625 [⇦ this spec on DLA] Type II Class I. The required pin diameter prior to anodize is .2459"-.2465". The required diameter after anodize and sealing is .2479"-.2485". Is this even possible to achieve? This is not a Hard Anodize process. Our specification also says "Anodic coatings, after sealing, shall weigh a minimum of 600 milligrams per square foot". How thick is this? Is this MIL spec, pin diameter prior to anodize, and coating thickness all consistent?
Bob LunnonMFG. ENGR. - Gainesville, Texas
January 8, 2009
![]() |
A. The difference is 0.0006 on the diameter, or 0.0003 on the side, which is very low for Type II and more like the newer IIB. If you will contact me I will read some of the ratios between coating weight and thickness from Sheasby/Pinner, which depends on alloy, time, current density, temperature, and acid concentration. The coating weight you call out does seem low for the thickness. 2024 at 0.00027 thickness and 0.00018 dimensional change shows 1104 mg, 6061 at 0.00028 which is 0.00019 dimensional change, shows 1758 mg, and 7075 at 0.00029 which is 0.00019 dimensional change shows 1594 mg. The difference between the thickness and the dimensional change is because the anodic film is approx. 1/2 under the original surface and approx. 1/2 above the original surface., again, depending on the parameters listed above. ![]() Robert H Probert Robert H Probert Technical Services ![]() Garner, North Carolina ![]() January 9, 2009 A. Bob - Colorado Springs, Colorado January 10, 2009 A. That's only a .002" coating, and while that's a bit thick for a type 2 coating, it certainly is achievable. I really can't comment intelligently about the weight of a type 2 coating at that thickness. ![]() Marc Green anodizer - Boise, Idaho January 12, 2009 |
A. Bob: Type II anodize (Sulfuric) requires a coating thickness of .0003-.0007 inches. Because the coating converts the aluminum surface to aluminum oxide, the coating penetrates the surface as well as expands, therefore the net change in a diameter is usually the same as the coating thickness. Take your finish dimensions and adjust accordingly.
Kent BackusFort Worth, Texas, USA
January 12, 2009
Hard Coat Anodizing Coat Weight Measurement
by Runge & Kaufman
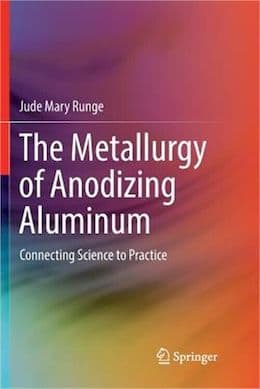
on AbeBooks
or eBay or
Amazon
(affil links)
Q. We have a plating line in house and since I'm still relatively new to the process, I am reviewing the MIL-A-8625 to clean up our paperwork. The spec for Type III is minimum coating weight of 4320 mg/ft^2 for every 0.001". According to a lab, the coating weight is measured from the before and after stripping of the panels. They take the thickness measurement with an eddy current tester for 1 side.The resulting number is to divide the coating weight by the one-sided measurement. Is this correct? I would think per the MIL-A-8625 that the coating weight, that was stripped from both sides, be divided by the total thickness? How is this MIL-A-8625 spec for type 3 interpreted?
Trung Lively- Black Mountain, North Carolina USA
October 14, 2019
A. Hi Trung,
Coating weight for Type III coatings is optional upon request from the procuring authority. So, if you can measure the thickness by eddy current, you don't need to do coating weight. Unless your customer requires the test to be done, I wouldn't bother, personally.
Aerospace - Yeovil, Somerset, UK
October 15, 2019
Q, A, or Comment on THIS thread -or- Start a NEW Thread