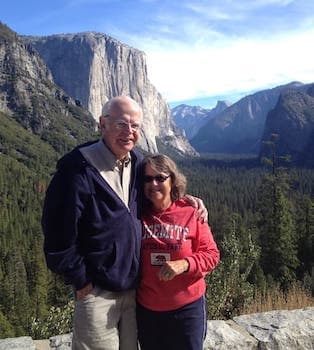
Curated with aloha by
Ted Mooney, P.E. RET
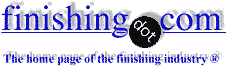
The authoritative public forum
for Metal Finishing 1989-2025
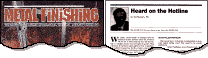
-----
Adherence problems with galvanizing
January 3, 2009
We are facing a very serious and particular case of peeling problem in our hot dip CGL.
It occurs only after the line is started up from a long shut down and lasts 2-3 days no matter what we do in the meantime. We set higher temperatures, more H2, reduction atmosphere, more HNX flow and lower speeds but still, we are losing A LOT of steel due to this problems.
The problem reveals in the adherence test and it peels only on the top surface operator side. There's an inspection windows in the radiant tube section of the vertical furnace from where we can see that the steel glows darker in the same area where it peels afterwards. So, we believe that its cause should be in the prior furnace sections (direct fire or pre-heating) but physical inspection shows us nothing. The CR strip has no stain in this same area.
Any help will be appreciated!
Employee - Curitiba - Brazil
January 11, 2009
Sir:
I normally do not comment on sheet galvanizing because I have extremely limited knowledge in this area. While doing chores (this is a ranch), I was thinking about your problem and remembering that some people think that aluminum segregates in the zinc toward the top. Thus I have seen literature that the aluminum percent is about double in the top one inch of zinc as compared with the rest of the kettle. Your problem lasting two or three days after a start-up makes me wonder if the problem could be aluminum. Also I have been told that in sheet galvanizing the aluminum percent is quite critical.
Regards,
Galvanizing Consultant - Hot Springs, South Dakota, USA

Q, A, or Comment on THIS thread -or- Start a NEW Thread