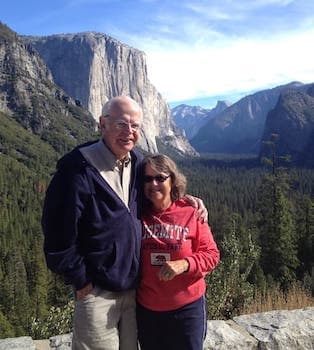
Curated with aloha by
Ted Mooney, P.E. RET
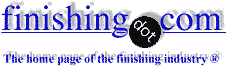
The authoritative public forum
for Metal Finishing 1989-2025
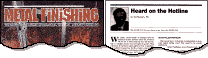
-----
Removing recast layer after EDM process on hardened A286 Nickel alloy
I understand that it is important to remove the recast layer after an EDM process on a hardened nickel based alloy like A286 steel since the recast layer is weaker than the base metals properties. Can anyone specify this process and how much material is and should be removed during this process.
James AlexanderProduct Designer - Schenectady, New York, USA
December 11, 2008
How much material should be removed will depend on the intensity of the cutting action (sparking amperage used), chemistry and microstructure of your substrate. Three to five thousands is common. An EDM surface though weaker from a standpoint, is indeed more resistant to chemical attack by many agents. A simple way to confirm the recast layer has been removed is to carefully wet the area of interest with a diluted solution of copper sulphate ⇦ this on eBay or Amazon [affil links] and sulfuric acid with the aid of a cotton tip. A bare surface should soon develop a copper color whereas any EDM will not. This process may damage delicate or polished adjacent surfaces. Good luck.
Guillermo MarrufoMonterrey, NL, Mexico
December 17, 2008
copper sulphate won't plate out on the iron based superalloy A286, so some other means of showing recast layer should be used. Metallography works well, when you can afford to be destructive.

Lee Gearhart
metallurgist - E. Aurora, New York
December 21, 2008
Q, A, or Comment on THIS thread -or- Start a NEW Thread