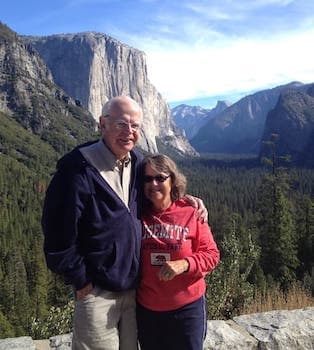
Curated with aloha by
Ted Mooney, P.E. RET
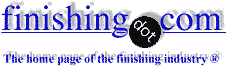
The authoritative public forum
for Metal Finishing 1989-2025
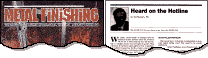
-----
Preparing a 1940 truck grill for chrome
I have a 1954 F100 that I am trying to restore. The grille was in decent shape but I had to fill a few holes where emblems where that I do not want to use. I have been told that pinholes in my welds will show and I am wondering if there is anything that can be used to fill them. I have been told brass won't work and I don't want to try and fill with steel as the metal is thin. Two chromers have passed on the work because the grille is rare and virtually irreplaceable. I don't know if this means it can't be done or they are just scared. Please help.
Ty Silvahobbyist - Ca
December 9, 2008
First of two simultaneous responses -- December 12, 2008
I have a number of clients who refinish parts so I will repeat what I hear them tell their clients.
1. If you do repairs to the part then we can not be responsible for how the finish turns out.
2. It is going to cost extra to undo and correct your "repair"
3. The reason the finish is blistered is that it was not properly prepped when you repaired it.
These go on and on. The best advise I can give you is to determine where you want to have the part refinished and talk to them before you do anything else.
process supplier - Great Neck, New York
Second of two simultaneous responses -- December 13, 2008
If you have not tried welding the holes that is good. The only way I know of to fill holes, particularly in steel, is to strip the parts down to clean bare steel using chemical paint strippers and a gentle low pressure fine bead blasting. Then polish down to a 400 to 600 grit sanded finish. Then put a nice heavy copper plating on it so that the holes can be soldered in. Then polish the solder down to an even flush finish using an orbital sander with about 320 grit sanding pad. In most cases the solder may not fill in evenly. So then you have to put more copper plating on it and sand again. This process may have to be done several times to reach the desired smooth finish.
The idea is to get the whole part down to a smooth even copper finish all over by soldering , copper plating and smoothing out.
You want the part to end up with an even smooth copper finish all over. Then you buff it out to a bright copper finish all over with only copper showing. Then you can put the final nickel and chrome on.
If you try welding or brazing in the hole you will only end up making it more difficult to do since the brazing and welding usually leaves pits and gaps and have different hardnesses than the part you are working on which causes the softer metals to scallop out making larger areas that need to be soldered and sanded evenly out causing a lot more work.,
If you do not have access to cyanide and acid copper plating tanks to do the repair it would be very impractical to try and do this yourself. Plus it takes an experienced eye to know when to stop soldering and start copper plating again.
I have done this type of work on many types of jobs where either drilled or rust holes have to be filled in then made to look like they where never there.
You end up spending a lot of time soldering and copper plating. So the job can get pricey.
I took a look at a '54 Ford grill and it looks like it uses rivets or tack welds to hold it together. These would all have to be drilled out by the customer preferably before anything can be done. My customers usually put their grills back together with stainless screws and locking nuts. I can do this part of the operation too, but most of my customers like to do this themselves just to save a few bucks. Of course drilling spotwelds out can be a bit tricky because you do not want to rip the metal.
I suggest you find someone who has experience with what you want done. They won't be cheap but at least you will get a good job done.
Good Luck, Frank
- St. Louis, Missouri, USA
Q, A, or Comment on THIS thread -or- Start a NEW Thread