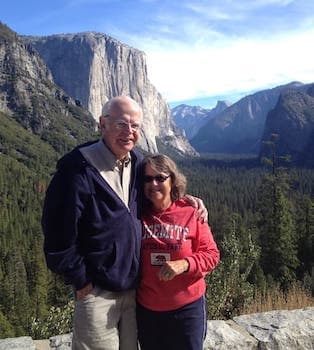
Curated with aloha by
Ted Mooney, P.E. RET
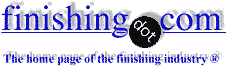
The authoritative public forum
for Metal Finishing 1989-2025
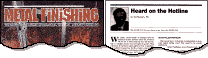
-----
Adhesion problems while powdercoating over clear zinc, chromate ROHS compliant
The parts are plated with clear zinc then we powdercoat this weldment approx. size is 38"X9"X24" tall, the powder is epoxy. We have had numerous problems with adhesion, sometimes we are experiencing the powder coming off in large sheets. They arrive from the plater and we let sit for 48 hrs, then we pre-bake at 400 degrees prior to applying the powder. I have powdered CRS and pre-plated material parts and baked them out with the weldments and all have passed adhesion tests.
Some time ago we experienced a similar problem, I was told it ended up being the chromate breaking down.
Industrial paint applicator - St Paul, Minnesota
November 30, 2008
December 1, 2008
Hi, Jeff. I suggest you inquire of the plating shop whether they are using hexavalent chromates or trivalent. Many shops have converted to trivalent due to RoHS requirements. All of these trivalent chromating processes are proprietary, there are many different approaches, and some of them simply aren't working for subsequent powder coating. Sorry for the non-answer but there isn't an easy one. The customer, the plating shop, and the powder coater must work together to select a cycle that will work.
Regards,
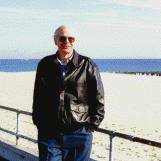
Ted Mooney, P.E.
Striving to live Aloha
finishing.com - Pine Beach, New Jersey
Good day Mr Olsen,
In my experience it is necessary to phosphate the parts after zinc plating in order to powder coat or E-coat them. You can use any kind of chromate you like, my choice is the lowest cost blue trivalent type. The kind of electrolyte in zinc plating also matters, the cyanide and alkaline types work better, the chloride baths sometimes also lead to peel off despite the phosphating.
all the best,
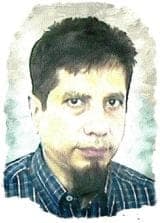
Khozem Vahaanwala
Saify Ind

Bengaluru, Karnataka, India
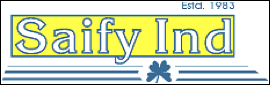
December 4, 2008
Q, A, or Comment on THIS thread -or- Start a NEW Thread