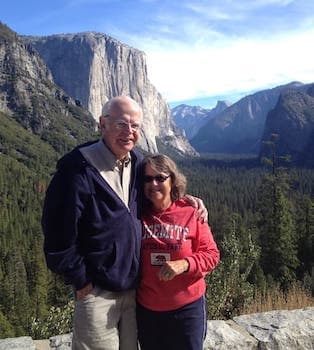
Curated with aloha by
Ted Mooney, P.E. RET
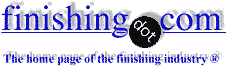
The authoritative public forum
for Metal Finishing 1989-2025
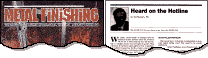
-----
Hard Anodize Ripple Problem
November 30, 2008
Recently our hard anodize process has been shut down because desired thickness is not being achieved (based on voltage at end of process). I am an electronics tech. that maintains the equipment not a plating expert so your help would be appreciated in this matter. At first I noted higher than normal ripple and went to work on the power supplies but could find no problem, then cleaned and secured all anode and cathode connections, still have high ripple. When doing test I observed that ripple was much higher when the air agitation was off (seems to build a capacitance between anode and cathode even though current is flowing), with air agitation on ripple is much better but still to high.
As the part is being anodized the voltage climbs to maintain constant current, my ripple also climbs,the opposite of what I would expect as ripple is always better the closer you get to full output of the power supply (a Dynapower 75v 300amp with no filter rated for 5% ripple).
Is it possible that my acid solution could be the problem? What are other symptoms seen when acid solutions are contaminated or out of spec?
Example of problem.
Before the part being processed, an inside diameter, gets to high enough voltage for spec. thickness the voltage will suddenly drop
(current stays at set point), its as if after the coating increases resistance to current flow at some point it finds an easier path to the cathode requiring less voltage.
Is the conductivity or lack of something to consider? I also see that there is alot of material eroded from the hangers, could this aluminum in the solution cause failure?
Any help or ideas would be very appreciated. Thanx. Kevin Obray
Plating Shop Employee (Electronics) - air force base, Utah, USA
December 1, 2008
Hi, Kevin. My first suspicion would be poor rack contacts. You need really good contact for hard anodizing because what can happen with poor contact is you start with no contact, so no anodizing is occurring; then as the voltage is raised you reach a "punch through" point. But the part has no anodized layer so it starts burning and building an instantaneous but poor anodized layer. You won't get anywhere until you have really solid contact. Good luck.
Regards,
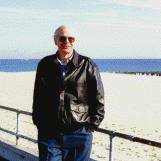
Ted Mooney, P.E.
Striving to live Aloha
finishing.com - Pine Beach, New Jersey
Q, A, or Comment on THIS thread -or- Start a NEW Thread