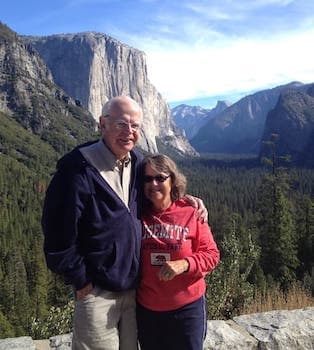
Curated with aloha by
Ted Mooney, P.E. RET
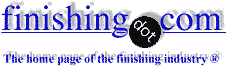
The authoritative public forum
for Metal Finishing 1989-2025
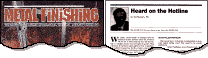
-----
Electroless Nickel Poor Finish on S7 Tool Steel
Greetings all. I am a recent mech engineering graduate just through my first year in the field. I am continually learning about available plating processes and have stumbled into a problem.
I have recently received a batch of parts that were EN plated with poor results. The parts are made of S7 tool steel, which is vacuum heat treated prior to being EN plated. The results per piece varied significantly. Some had minor pitting, some had significant pitting, and some were just plain rough. The part has a few through holes, which had a good looking finish towards their interior, which makes me think its not a substrate problem.
What do you think could cause this type of reaction? Do you think our substrate or machining process could have caused this? (see pics below)
We have had the same part EN plated in the past with excellent results. A smooth and bright finish both inside and out. The only variable I've identified is that we bead blasted
⇦ this on
eBay or
Amazon [affil links]
these parts prior to plating to remove some surface rust; however, the interior threads would not have been blasted.
I am using EN plating for its corrosion resistance, and to make the parts look good. Our plater specified they would coat per ASTM B733 0.0002" thick.
These are some links to pictures. Two parts are from the bad batch, the best looking part is the one that was blasted and turned out well.
|
|
|
|
I appreciate your comments and suggestions. I can provide more details if they are needed.
Nathan.
Product Design - Salina, Kansas
November 26, 2008
A. First, 0.0002" is not enough EN to have anything but the most minimal corrosion resistance.
Based on the second picture, the problem is in the S7 and not the plate.
The parts have had a significant amount of rust that you have a terrible surface. The plater's prep steps would remove a small amount of additional material, particularly in the rusted areas that were peened over by the blast step.
S7 is moderately rust resistant to start, so how did your firm possibly allow the parts to rust that bad?
I will guess that these become scrap and new parts are made.
- Navarre, Florida
A. If the initial oxidation you describe was not that bad, it could also be that the plater tried to strip an improper plating and the base material was severely attacked in uncovered selected areas. These obviously will not be leveled by the plating.
Guillermo MarrufoMonterrey, NL, Mexico
The batch of parts that resulted in this poor plating would have had minimal rust when they left our facility. They would not have been blasted by our facility. A batch that we had plated earlier, which plated with good results, did have considerable surface rust. However, the blast step did a good job to remove this rust.
The part in the second picture seems to have a build-up of plating rather than erosion of the base material. This build-up is spotty and in varying thicknesses, contributing to the rough look. Would this be a cleanliness issue?
Thank you for your responses. I have much yet to learn.
Product Design - Salina, Kansas
Q, A, or Comment on THIS thread -or- Start a NEW Thread