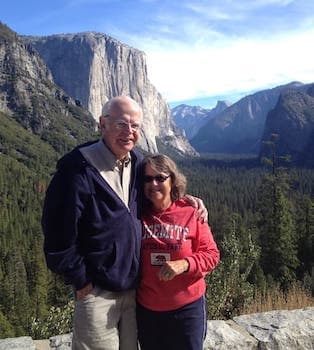
Curated with aloha by
Ted Mooney, P.E. RET
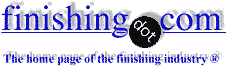
The authoritative public forum
for Metal Finishing 1989-2025
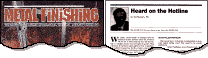
-----
Seal issue with nickel fluoride and hot flashed part
I am in Detroit root causing an ultrasonic sensor membrane that turns from black to purple in less than 200 days sunlight exposure. We looked at good parts and bad parts with the SEM-EDX and see nickel on the good parts but no nickel on the bad. The good parts also start cracking on the surface due to the electron bombardment of the SEM. The supplier uses a low temperature sealant from a qualified source. The supplier also performs a rinse and a hot flash (10-20 minutes at 165-175 °F; pH 5.0-6.0)after the seal tank. We looked into the control data and the process was out of control at times (0.83% concentration vs. 1.0-1.25% control plan; but also technical bulletin for the sealant recommends 1.5-2.0%). My question is: is the concentration of sealant a viable root cause? Everything I read on your site, which is excellent by the way, makes me believe the bad parts must of just flat missed the last two tanks.
Allen Schwartzproduct specifier/user - Detroit, Michigan, USA
November 19, 2008
Obviously it is not "sealed". Do an ASTM B136 seal test. Seals are very easy to contaminate because of the weak solution. Just a smidgen of drag in, then regardless of the analysis and pH, they will not "seal". So-called low temperature sealing formulations are even more sensitive, so much so, that most of the reputable suppliers have discouraged low temp sealing completely. Start applying a regular seal test, then consider specifying a mid-temp-nickel acetate-sealant.
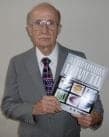
Robert H Probert
Robert H Probert Technical Services

Garner, North Carolina
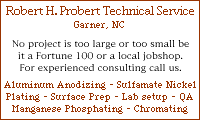
November 21, 2008
Q, A, or Comment on THIS thread -or- Start a NEW Thread