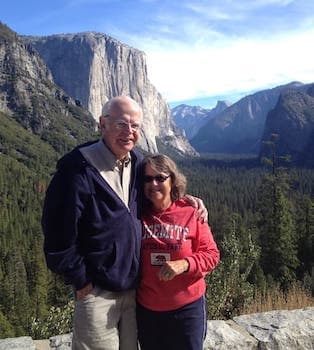
Curated with aloha by
Ted Mooney, P.E. RET
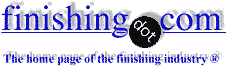
The authoritative public forum
for Metal Finishing 1989-2025
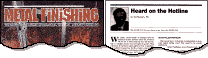
-----
Quantifying the effectiveness of scale removal
We run a metal coating process. Part of our process is scale removal. I am trying to optimize the scale removal process. How can I quantify the effectiveness of(or lack of) scale removal?
Ralph R PalumboAutomotive Part supplier - South Haven, Michigan
November 18, 2008
Hi, Ralph. I've never heard it expressed that way, although it doesn't sound unreasonable. Still, when you look at the surface, the part is suitable for its intended purpose (which is subsequent coating) or it isn't, so maybe that's a start. For example, parts need to be completely free of scale for electroplating and certain chemical displacement reactions.
Perhaps another possibility is a weight comparison between your chemically descaled parts and a sandblasted part to some particular sandblast specification.
Regards,
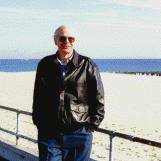
Ted Mooney, P.E.
Striving to live Aloha
finishing.com - Pine Beach, New Jersey
November 19, 2008
Ralph, Ted has made a good suggestion in using a "sandblast" specification; Namely a test for blasting intensity is the "Almen Test Strip". These strips are a means to measure compressive stress induced into surface of components, or in your application cleaning intensity. If you blast an Almen Strip, which can be affixed to raw part; then blasted into a "good part", the defection of the strip could be used to quantify the cleaning process. You should contact a supplier of Almen strips to see if they could help you run this experiment with you. Regards,
Tim DeakinNorth Tonawanda, New York
November 22, 2008
The SSPC (Steel Structures Painting Council) and the NACE (National Association of Corrosion Engineers) both have scales for evaluating the surfaces of substrates. Check out their web sites. For example, SSPC 8 is pickled. I don't think that there are any better references for what you seek. In my humble opinion, there are only three possible grades: (1) underpickled; there is still residual oxide on the surface; (2) pickled correctly; and (3) overpickled; there has been so much pickling done that the carbon and silicon on the surface interfere with subsequent processing.
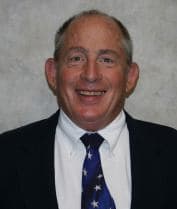
Tom Rochester
CTO - Jackson, Michigan, USA
Plating Systems & Technologies, Inc.

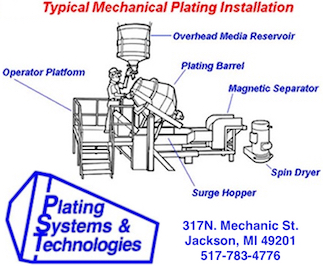
November 25, 2008
Q, A, or Comment on THIS thread -or- Start a NEW Thread