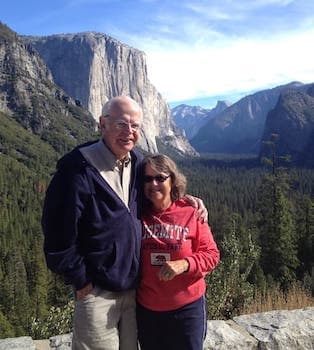
Curated with aloha by
Ted Mooney, P.E. RET
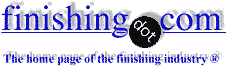
The authoritative public forum
for Metal Finishing 1989-2025
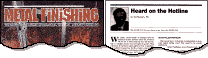
-----
17-4 Forging Rust on Unmachined Surface
I have an assembly made from several forged 17-4 stainless steel parts that then have secondary machining operations. All of the exterior parts are showing a light layer of rust on the surfaces that were not machined. The parts were passivated to AMS2700 method 1 type 4 after machining. Any advice on how to prevent this from happening?
Bill ThomasEngineer - Atlanta, Georgia
November 14, 2008
November 17, 2008
I cannot find my AMS 7400, but note. type IV has been discontinued from AMSQQP35
[canceled] which requires 17-4 to be passivated in their
"Type II or Type VIII". Type II is 25%/vol Nitric Acid with 2.5% /wt Sodium Dichromate at 125F. Type VIII is 50% Nitric Acid at 125 F.
ASTM A967 requires 17-4 to be passivated in what they call "Nitric
1" which is exactly the same as Type II above.
We suspect your passivator has a quality problem or is using the wrong process for 17-4.
Note that Nitric Acid actually control oxidizes the surface; citric acid merely reduces the surface and depends on th air to do the oxidation, and sometimes the protection is not good enough, especially on some alloys.
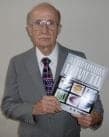
Robert H Probert
Robert H Probert Technical Services

Garner, North Carolina
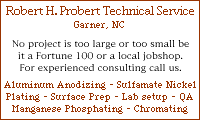
QQ-P-35c does not have type IV, but 2700 has the full list of eight types of nitric passivation baths including IV. However as Robert said, type IV is not recommended for 17-4. That grade should use I, II, III, or VIII, or a citric-based bath.
It is true that a citric passivation bath does not oxidize the steel surface. It is also true that a citric bath removes only the iron and does not etch the surface. A nitric bath removes the iron preferentially but does attack all the metals present in the alloy. This limits the depth of a chromium enriched layer that can be achieved to less than is possible with citric acid .
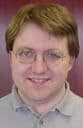
Ray Kremer
Stellar Solutions, Inc.

McHenry, Illinois
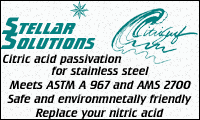
November 25, 2008
I will respectfully disagree with the citric acid statement above. Our facility is constantly re-passivating "citric" acid passivated
(300 series and other)stainless. Because the passive layer formed by the citrus process is inferior to the traditional Nitric acid process.
The citric process was developed for a more "green" disposal approach. It is (In my opinion from experience) an inferior process, with an inferior end product.
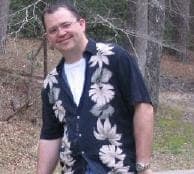
Ryan Cook
Toccoa, Georgia
January 5, 2009
Hi, Ryan. It's also true that in some ways trivalent chromates aren't as good as hex, and the substitutes for cadmium aren't as good as cadmium, and in some ways neither acid nor alkaline zinc is the equal of cyanide zinc. I'm confident you also constantly re-do those finishes.
Your experience is your experience and not to be dismissed, but this citric vs. nitric debate has been going on for 13 years on these pages, with both sides represented by vested interests. Both approaches can work.
Regards,
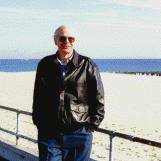
Ted Mooney, P.E.
Striving to live Aloha
finishing.com - Pine Beach, New Jersey
January 6, 2009
My 2 cents from experience. Stellar's Citric worked far better on 400 series SS than any of the nitric processes. On 300 series, they both worked. The nitric was cheaper, but more dangerous to use. So, it is dealer's choice.
James Watts- Navarre, Florida
January 6, 2009

this text gets replaced with bannerText
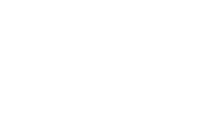
Q, A, or Comment on THIS thread -or- Start a NEW Thread