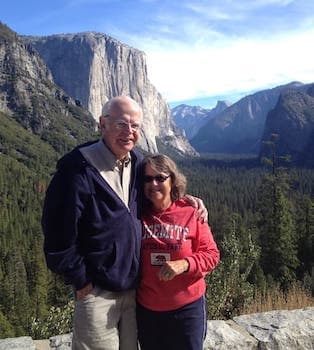
Curated with aloha by
Ted Mooney, P.E. RET
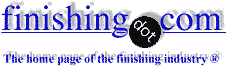
The authoritative public forum
for Metal Finishing 1989-2025
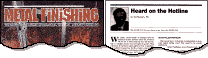
-----
Peeling problem in nickel-chrome plating
Q. Hello My name is Chris and I'm an electrician at a chrome plating operation. I am currently having problems with peeling between the Semi-bright and Trini layers. The problem seems to occur at two specific semi-bright tanks however I checked these rectifiers and they seem to be operating properly. The type of rectifier is a Dynapower primary thyristor controlled polyphase rectifier (with auxiliary). This rectifier has 6 primary SCRs and 6 diodes on the output side. My wave looks excellent on the oscilloscope however I've found the ripple is a little high on the semi's. The one is about
8% and the other one stands around 11%. We run these rectifiers at around 25% output. This has never really been a problem before until we got a new part and they always seem to peel at the same location
(On the auxiliary portion of the part but only the parts on the center of the plating rack).
I have also checked the rectifier that is responsible for the tri-Ni auxiliary layer and found that a phase was missing on it. I fixed this problem and found that it was a bad rheostat. However, the problem still persisted.
So here's the question I'm wondering about. Is it possible that a high ripple causes a peeling condition or will that only affect the quality of the plate? It is my understanding that the cause of peelers is due to a bi-polar condition in the tank or a loss of voltage during the plate cycle but I could be wrong because I'm not really a plating expert. Any help you give me will be greatly appreciated. Thanks.
Shop Electrician - Windsor, ON, Canada
November 4, 2008
A. Are you getting a bi-polar effect before you set down the rack and make contact. Use a cable and enter the solution "hot".
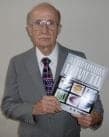
Robert H Probert
Robert H Probert Technical Services

Garner, North Carolina
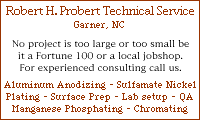
November 5, 2008
A. Cris,
you talk to peeling problem between semi nickel and tiny layer.Can you say what is the tiny layer is ? bright nickel, dur-nickel (particle), chrome, etc.
The peeling is between semi nickel and bright nickel
because of transfer from semi to bright nickel too delay /passivation the surface.
If you have parts in tank and other part from the rack touch, then bipolar condition happen and parts peel,
Check your brightener system work right also check electrical current break down during the plating.
Good Luck!
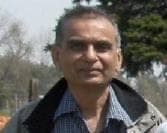
Popatbhai B. Patel
electroplating consultant - Roseville, Michigan
November 5, 2008
A. Hi Chris,
If you have two plating racks in the same solution cells at the same time. There can be a bi-poler effect. Try to let the current get down when you lifting one of the racks.
Regards,
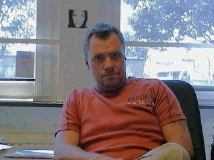
Anders Sundman
4th Generation Surface Engineering
Consultant - Arvika,
Sweden
November 7, 2008
A. First of all I'd like to thank you both for your responses and help.
Since I posted here last I had put a Chart recorder on the rectifier to show me how current and voltage respond during the plating cycles. I found that whenever a bar either entered or exited the second cell of the bath I had a very fast voltage/current drop to zero. I imagine that this is where I could be getting a bi-polar effect. I noticed that there is no voltage/current drop when the bars interact with the first cell so I'm assuming it's not the rectifier. I also put the recorder on another 2-cell tank and this drop wasn't present.
I should probably mention that all of our semi's are live entry tanks. I have been told that its important that the main makes contact before the auxiliary on entry and breaks contact last on the exit. In order to do this we use copper ticklers which really is some thin gauge copper plate bent to make contact on the main before the bar actually sits in the saddle. When I looked at the ticklers I realized that there was arc/flash marks on one of the ticklers in the second cell. I'm thinking this arcing is what is causing my voltage/current drop. I changed the tickler to make better contact on entry/exit. I'm hoping this will fix my problem. I'll keep you guys posted. I should find out early this week.
By the way. For the gentleman that asked me about the "tiny layer". It's actually a Trini layer. That is just the short form of what we call the tank. I'm not 100% sure of this but I think the long form is Tri-lite nickel bath. This bath comes between the Semi and Bright layers. Do you not have a tri-Ni tank?
- Windsor, ON, Canada
November 8, 2008
A. Anders,
Thank you for your suggestions and response. I have heard of other plating operations ramping down current upon entry and exit of the cell. But we have never done that and we have never really had any problems until now. As I have explained in my previous post we use what we call "ticklers" to make the main before the auxiliary which allows the bar to enter the solution hot. This seems to solve the whole bi-polar problem.
I have changed and re-positioned one of the ticklers on the problem cell which seemed to fix the problem and I haven't had any voltage or current drops since then. I did this because I noticed some scorching and pitting on the tickler which suggests excessive arcing upon entry/exit.
I have also recently noticed that those particular saddles on that tank are further apart than the other tanks. I would imagine that some of the bars weren't fully contacting the ticklers which is causing an arcing problem and the voltage/current drop. I definitely need to do some work on the saddles to prevent this.
In conclusion, the problem seems to be gone and I hope this is the case. Once again I thank you all for your suggestions and your opinions are highly valued. I hope I can be as helpful to some of you in the future. Thanks again and good luck with your operations.
- Windsor, ON, Canada
November 13, 2008
Q. Hello,
I have the same problem of peeling off from semi bright nickel. we takes no time to transfer parts to bright nickel, but still some parts still peeling.
I observe that from semi bright nickel parts coming out almost dull rather than semi-bright. I add brighteners as recommended by supplier, but no improvement.
we do plating on auto parts like FENDERS, SILENCERS, and other parts like that. ALL PARTS COMING FULL DULL..
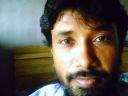
Aftab Jahangir
chemist - Karachi, Pakistan
November 15, 2008
January 9, 2013
Q. After chroming, chrome layer peels off from semi-bright nickel sometimes peels off occurred within chrome even could be removed by fingernail on some areas of parts, very bad adhesion.
Process flow: pre-treatment--> zincate free cyanide--> semi-bright nickel--> activation--> chroming
Parts substrate: Die-cast aluminium alloy.
All line chemicals provided from ATOTECH, HEEF25 series, CrO3, 300 g/l; H2SO4, 2 g/l (lower than 2.8 g/l recommended by ATOTECH because it caused bad throwing power to our complicated parts since we built line so we always work with 2 g/l sometimes even lower)
We have done some trials but no effect as following:
1. Increase content of sulfuric acid to 1.2 g/l in activation tank and dipping time from 30 to 80 seconds
2. Adjust ramp up time of rectifier from 0 seconds to 60 at every interval of 10 seconds in chrome tank
3. Put parts in chrome tank without current in first 2 mins and 5 mins then directly go to normal working current
4. Put parts in chrome tank with 1.5-2 times of normal working current for 2 mins then down to working current.
Any advice highly appreciated!
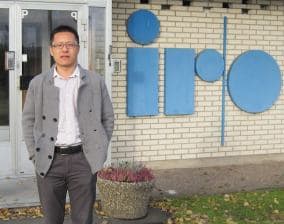
Steven Chen
plating shop employee - Wuxi city, Jiangsu province, China
A. Hi Steven.
HEEF (high efficiency, etch free) suggests it is a hard chrome plating process. Your problem is chrome is peeling from semibright nickel.
1. The activation step prior to chroming troubles me. Is this necessary?
2. You should avoid point 3 (put parts in chrome tank without current for 2 to 5 mins) This will only passivate the parts. Live entry is preferable. 1.5 to 2 times working current for live entry seem too high. You may burn the parts.
- Penang, Malaysia
January 11, 2013
Thank for your opinions. Activation is indeed required according to ATOTECH local experts; otherwise will cause much more adhesion problems as well as we use it since starting line without the similar issue I've posted. This is a first time we have the problem that peels off from semi-bright nickel and sometimes within chrome layer itself.
When we use the over 1.5-2 times current against normal work current the result shows a little better, so it helps in somewhat
Thanks again!
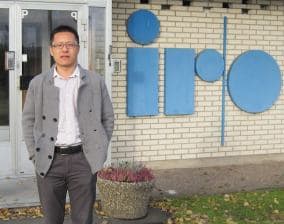
Steven Chen
- Wuxi city, Jiangsu province, China
January 17, 2013
A. Hi Steven. Obviously, you are more familiar with the operation of your line than we are. But I agree with Cheah that for decorative nickel-chrome the traditional sequence is: after nickel plating, rinse quickly and go directly to the chrome plating tank at normal voltage. Try it, you might like it.
In typical decorative nickel-chrome plating, the chrome would not exceed about 40 millionths of an inch thick, tops; so it sounds hard to believe that you would be able to see laminations within the chrome plating itself when they would be, say, only 5 or 10 millionths of an inch thick.
Regards,
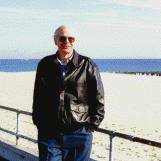
Ted Mooney, P.E.
Striving to live Aloha
finishing.com - Pine Beach, New Jersey
January 17, 2013
A. Hi Chan
Do you have a drag out tank after semibright nickel? Nickel layer can get passivated in the drag out dip if the drag out solution density as well as pH is higher than the operating range of your nickel bath.
- India
January 18, 2013
A. Hi Steven.
I have the impression that you have two types of peeling problem.
1. The chrome is peeling from the semi bright nickel.
2. The semi bright nickel is peeling from the substrate.
Your substrate is diecast aluminum alloy. Can you elaborate on your pre-treatment process. Thanks.
- Penang, Malaysia
First of two simultaneous letters -- January 22, 2013
Q. Thanks Ted and Kumba, our line is a hard nickel-chrome not decorative.
After semi-bright nickel there are subsequently 2 steps of sulfuric acid dipping with concentration of around 0.07-0.14 ml/L and another activation tank dipping with concentration of 0.8 g/L H2SO4 and 2g/L CrO3 then go directly to chroming with normal current.
One more question needs your help, how to improve throwing power as our parts are very complicated showing in pictures I have posted before, any good ideas for that will be very appreciated!
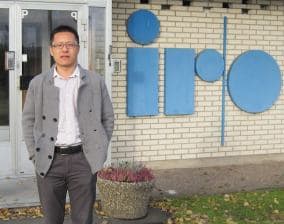
Steven Chen
- Wuxi city, Jiangsu province, China
Second of two simultaneous letters -- January 23, 2013
A. Hi Steven,
Several ways used to improve hard chrome plating throwing power:
1. Using conforming anodes (or auxiliary anodes) to align with complicated plating surface (hard-to-plate area).
2. Optimize chromic acid to sulphate (or other catalyst) ratio (~100:1).
3. Increase current density.
4. Reduce bath temperature.
5. Increase bath pH.
Regards,
David
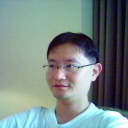
David Shiu
- Singapore
Q, A, or Comment on THIS thread -or- Start a NEW Thread