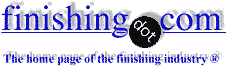
-----
Nickel plating on Inconel Q&A

Q. Bumps/build-up on low stress nickel plating?
In the last 2 months, I have been getting build-ups/bumps on the OD and face of Inconel 718 seals while doing nickel plating.
I filtered the tank and carbon-treated it, but no positive results have been obtained. Metal content in the solution bath is 1 ppm (suggested not to be > 10 ppm). pH and boric acid content are within spec requirements.
Lately, I have been keeping the pump off (no mechanical agitation occurs in the tank) and doing dummy plating for 12 hrs overnight; a bit of improvement, but still bumps/build-ups are observed.
I am looking for recommendation/advice on what I can do to solve this issue.
- Lowell, Massachusetts
January 10, 2023
![]() |
? How is the wetter? Any signs of dust floating on top of the solution? E Gonzales- Boulder Colorado A. Hi Stephanie - Winnipeg, CANADA A. You say metal content is 1 ppm. When you said "low stress nickel plating", do we assume you mean sulfamate nickel plating. Metal should be 10 ounces per gallon, lower causes noduling which you call "bumps". Come back with more data on nickel metal concentration, how you measure pH, temp, and exact boric acid. ![]() Robert H Probert Robert H Probert Technical Services ![]() Garner, North Carolina ![]() |
⇩ Related postings, oldest first ⇩
9th Edition, Vol. 5
"Surface Cleaning, Finishing & Coating"
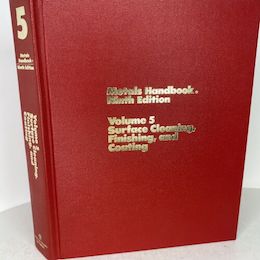
on eBay or Amazon
or AbeBooks
(affil link)
Q. I am trying to nickel strike Inconel 718 before hard nickel plating; the trouble I am having is adhesion to the substrate . What type of nickel strike to use?
Sean Jameshardchrome/nickel plating - Malaga, Western Australia
2003
Ed. note: While awaiting responses regarding adhesion, try to get access to the ASM Handbook Volume 5 which has a chapter on activation of Inconel and other difficult to activate metals ⇨
![]() |
A. Sean, ![]() Anders Sundman 4th Generation Surface Engineering Consultant - Arvika, Sweden A. Inconel is a very high nickel alloy, so it is not easy to plate. But you left out two important steps: How are you cleaning and how are you etching? The strike is irrelevant unless those two are adequate. A high acid Wood's Nickel Strike would be the preferred strike by nearly all platers. James Watts- Navarre, Florida A. Try a high chloride one such as Wood's nickel. ![]() Trevor Crichton R&D practical scientist Chesham, Bucks, UK |
A. We used to do hard chrome direct on Inconel 718 after activation in H2SO4/HF 30-50 A/sq dm, and the adhesion used to be very good .
Good luck,
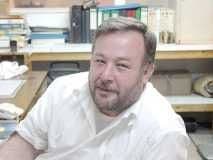
Khair Shishani
aircraft maintenance - Al Ain, UAE
2004
Nickel-gold (Ni/Au) plating on Inconel 690
Q. Need to plate an Inconel 690 bar, 2-3 inch diameter, with gold to serve as an electrical contact. Plan is to put on a nickel strike, then add a few hundred microns of Ni, and then add a gold overlay.
Questions:
Anyone have experience with plating on Inconel 690?
Is an electroless nickel acceptable for the Ni on top of the strike (does it affect conductivity)?
What is the expected conductivity of the plate?
How good is its adhesion - overall and each layer?
Can it stand to operate at 200 °C to 300 °C? Are there other options?
Consulting Chem/Corrosion Engr. - West Richland, Washington, US
2004
A. Inconel, as well as any high nickel alloy has to be struck with a highly acidic Wood's bath. Problems come when shapes are complex, since due to its high acidity, the throwing power of this bath is limited. EN can be plated on top of the Wood's without too much a problem, but to successfully gold plate on top of EN, an acid gold chemistry has to be used and transfer times kept at a minimum. Depending on your gold chemistry, a brief compatible organic acid rinse in between might help. About your other questions, current capacity of the gold plate is related to its cross-section. If too thin, current will find its path thru the substrate, lowering the overall conductivity. If dollars and volume allow it, options worth investigating would include PVD, CVD, sputtering, etc.
Guillermo MarrufoMonterrey, NL, Mexico
Multiple threads merged: please forgive chronology errors and repetition 🙂
Inconel surface activation for nickel plating
Q. I run a plating shop and am wondering if anyone out there knows how to successfully plate Inconel with nickel and then gold. Currently we have successfully coated the substrate but have experienced blistering at 260 °C. Does anyone know of an activation process prior to the Wood's strike that will enable the woods, EN, and gold to hold at 260 °C for 24 hours. Thanks for your time.
Jim Buckplating shop - Fort Wayne, Indiana, USA
2004
A. Inconel is not easy to plate as you are finding out. I have seen three procedures work after they were tweaked:
1. sulfuric-hydrofluoric mixture with a short low voltage anodic etch. Tricky point between activation and smutting.
Next was a low current-high current sulfuric acid. This was long and generated lots of fumes, but worked.
Last was a dip in nitric hydrofluoric acid.
I do not remember the exact specifics of the three approaches. You may be able to find a similar process in one of the recommended books. I would see if INCO had any suggestions. I would also check with the international nickel institute.
James Watts- Navarre, Florida
A. Inconel is not difficult to activate and then plate on. I have described a method here at the forum before. Jim is right there recommending hydrofluoric acid. It's necessary to see the gassing on the part when activating in hydrofluoric acid step; it could take 30 sec to 2 minutes or more without gassing and no adhesion on Inconel material.
Regards,
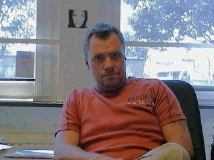
Anders Sundman
4th Generation Surface Engineering
Consultant - Arvika,
Sweden

Never use HF anywhere unless trained!
If you do, you MUST have the antidote gel on hand for instant use!
Calcium Gluconate
for HF acid burns
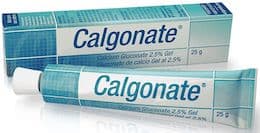
on eBay or Amazon
(affil link)
A. Hi,
Please remember that hydrofluoric acid is only for those trained in its use, and don't even think about getting any until you have calcium gluconate gel instantly available. Platers who are inured to cyanide and chromic acid still justifiably fear HF.
Luck & Regards,
Ted Mooney, P.E.
Striving to live Aloha
finishing.com - Pine Beach, New Jersey
Q. I found that the lifetime of H2SO4 or H2SO4+HF etching solution is very short for Inconel activation. Is there any way to extend the etching solution lifetime?
Sean XiaResearch - AB, Canada
2007
Q. I am involved in a Nickel Sulfamate plating process. The base materials over which this nickel plate is applied is an configuration of two Inconel flanges welded to a ferrous steel tube bonding the flanges together.
Cleaning: The part is immersed in a cleaning bath where we apply an electrical charge in both an anodic and cathodic cycle. My question is there a recommended sequence for these anodic and cathodic cycles?
Activation: The part is immersed in a Sulfuric acid bath where we apply an electrical charge in both an anodic and cathodic cycle. My question is there a recommended sequence for these anodic and cathodic cycles?
Plating shop employee - Euclid, Ohio, USA
October 23, 2008
A. Hi, Joe.
Electrocleaning: When the work is cathodic, the scrubbing bubbles are hydrogen; when it is anodic, the scrubbing bubbles are oxygen. There is twice as much hydrogen produced as oxygen, so the cathodic cleaning action is better, but it raises the possibility of hydrogen embrittlement and the deposition of metallic smuts on the work. So cathodic followed by anodic may be best.
Electroacid: The important rule here is that you can only properly plate on an activated surface, so you do not want to end the acid cycle on a phase where the part may be passive. I think that means the work should be cathodic.
However, don't forget that electroplating is an incredibly complicated process if you try to scientifically take every little detail into account. So there is a lot of empirical knowledge involved in the process. You may never resolve the science of how many seconds of this and how many seconds of that; you may have to just go with what works, and just hold those parameters.
Regards,
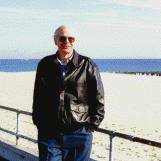
Ted Mooney, P.E.
Striving to live Aloha
finishing.com - Pine Beach, New Jersey
A. You can get some guidance from books on plating that include prep steps.
I think that you have a poor engineering setup with Inconel being considerably more difficult to activate than the steel.
You run the risk of over activating the steel or under activating the Inconel.
I like ending on cathodic as the tank retains a charge after the current is shut down and actually reverses and the part become anodic for a second or two. The use of current requires that you have a much less contaminated tank than a simple no current or it will deposit trash during the cathodic cycle. I would experiment with a scrap part to see what might work best for you.
- Navarre, Florida
October 24, 2008
Electroless Nickel plating on Inconel
Q. Dear all,
I would like to ask a question, please.
We trying to use electroless Nickel plating for Inconel sample, but it is not working. It is not plating an Inconel piece at all although we are following all instructions for it (right temperature, right pH, right mixture for the bath solution).
Do you have any idea why it might be happening?
Thank you for all your advice in advance,
Elena
- Bracknell, UK
April 29, 2014
A. Elena,
Are you striking Inconel using Wood's Nickel - reverse and forward?
- Kitchener, Ontario, Canada
June 11, 2014
A. ELENA,
Inconel is a very high nickel content typically 13.5% and 6% Chromium.
Typical sequence for plating on Inconel :- Soak cleaning , Acid Dipping , Etching ( 20 to 30 Sec ) , Wood's Nickel Strike cathodic ( 2 to 3 minutes ) , Plating.
Regards,
Process Engineer - Tumkur , Karnataka , INDIA.
June 14, 2014
A. I've never found a need to etch Inconel... My process was as follows:
1.) Soak clean
2.) Electro-clean
3.) 50% HCl for 1-2 minutes
4.) Wood's nickel strike, 3-5 minutes
5.) Plate
- Lowell, Massachusetts USA
June 16, 2014
Q, A, or Comment on THIS thread -or- Start a NEW Thread