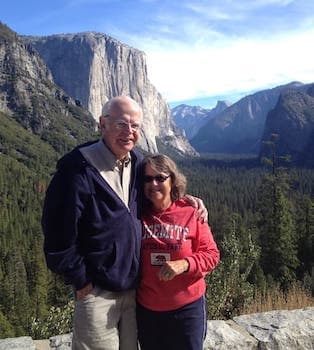
Curated with aloha by
Ted Mooney, P.E. RET
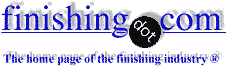
The authoritative public forum
for Metal Finishing 1989-2025
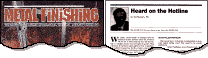
-----
Corrosion and pitting during pre-anodize clean and etch on 7075-T7351?
October 10, 2008
We are an aerospace manufacturing company that supplies complex parts, built to specification, for several customers building satellites and related hardware. Our parts are made from a variety of metals with the most common being 7075 Aluminum. All parts are sent to outside processors for different types of finishes.
We recently had an order of parts, made from 7075, that displayed of pitting and corrosion in a very specific area of the part following the clean and etch process normally performed prior to the anodize process. The corrosion resembled a matte gray coating with black spots and blotches within it. The surface contamination could be removed mechanically (scraping lightly with a knife edge) leaving pits that had additional black contamination in them. Further mechanical processing with fine "Scotch Brite" was able to remove the black residue from the pits leaving a shiny void.
As I understand so far, zinc is the primary culprit in corrosion. This was pointed out by the metal finishing house and confirmed in other publications found on the internet. The metal finishing house assessed the cause as being random concentrations of zinc and perhaps something we had done during machining.
The review of the parts that I did shows the corrosion and pitting to be confined to one area of the part, a .050" step adjacent to a larger flat surface. The corrosion and pitting is confined to just the surface of the .050" step. I would anticipate that a bad heat of
7075 would have concentrations of zinc throughout the aluminum and would expect corrosion to be in random areas on all surfaces of the parts.
Is there something we did in the machining/cleaning that would cause the corrosion and pitting to happen? (This is the first time we have seen this in 13 years.) Is there something in the cleaning/etching process that would concentrate corrosion to zinc on the narrow stepped surface while not affecting concentrations of zinc on other larger surfaces?
Is the gray and black surface contamination formed on the surface in the cleaning/etching solution or does it appear at a later time when the part is dry?
As I understand pitting, it is considered a critical source for crack propagation and cannot be tolerated in flight parts. Can the pits be reworked to eliminate this problem?
We have additional orders of parts ready to go out for anodize and we are on hold until we find out what happened to this order.
Any ideas and feedback would be greatly appreciated.
Best Regards,
mfgr of parts requiring special process metal finishing - Longmont, Colorado, USA
First of two simultaneous responses --
7075 Aluminum is sensitive to etching. I think you may be over etching. I suggest a very short etch time or none at all. The deoxidizing step etches enough. Use a short time in the deox (or nitric acid if used)
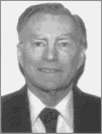
Don Baudrand
Consultant - Poulsbo, Washington
(Don is co-author of "Plating on Plastics" [on Amazon or AbeBooks affil links]
and "Plating ABS Plastics" [on Amazon or eBay or AbeBooks affil links])
October 14, 2008
Second of two simultaneous responses --
7075 contains copper at 1.6% as well as zinc at 5.6 %, and both of these metals "walk" with time and/or temperature to the grain boundaries. If these metals walk out of alloy onto the or near the surface, then the etch, deox, and electrolytic sulfuric acid will selectively pull them off and leave pits. MOst zinc salts are white or gray. Some copper salts and oxides are black.
Go back and try to find some "fresh" (not so aged) 7075. Sharpen the tool that cuts the "step" and pour on more coolant. Ramp up slower in the anodize and do not exceed 12 amps per square foot (unless you mean hard coat, then you have to use about 24 ASF). This advice has helped many clients, but I did experience one batch of 7075 that I absolutely could not hard coat without pitting.
Do come back and let us know what happens with this and also other's advice .
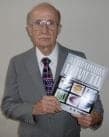
Robert H Probert
Robert H Probert Technical Services

Garner, North Carolina
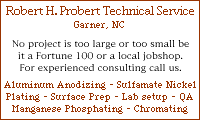
October 14, 2008
Richard
The fact that your problem occurs only in one area suggests something other than the material/alloy itself. At what point can you
'scrape' off corrosion product? Prior to shipment to your processor? Does the problem show up only after a cleaning process? Could coolant
(or rinse water) have been allowed to remain on the step after cutting? Was the coolant aged? Could you have galling from a dull cutter?
You might have your processor gold chem film (
MIL-DTL-5541
[⇦ this spec on DLA] Class 1A) a couple of parts with a no-etch clean, and inspect the finish. Then some with an etch. (What is the aluminum content of the etch?) The results can narrow your search.
- Colorado Springs, Colorado
October 15, 2008
October 20, 2008
Greetings Willie Alexander,
Thank you for your response and pertinent questions. I will try to answer them as best I can. For clarity about this issue, let me re-state - There is one order of 34 parts, all made from the same plate of aluminum and this is the first and only time this corrosion problem has been identified in the thirteen year history of St. Vrain Manufacturing.
Your Questions:
At what point can you 'scrape' off corrosion product? The special process provider cleaned and etched the parts for anodize. The corrosion was detected just before the parts were to be racked and anodized. St. Vrain Manufacturing shipped the parts to the special process provider with no signs of corrosion. I believe the correct answer to this question is: The corrosion can be scrapped off after the parts were cleaned and etched by the special process provider.
Prior to shipment to your processor? No, the corrosion was not visible when it left St. Vrain Manufacturing. It was only identified at the special processor after clean and etch and prior to Anodize
(The parts were NOT anodized - they were returned to St. Vrain manufacturing after the corrosion was identified).
Does the problem show up only after a cleaning process? The corrosion was not identified when being machined, inspected and packaged at St. Vrain Manufacturing. The problem was identified by the special processor after clean and etch.
Could coolant (or rinse water) have been allowed to remain on the step after cutting? The machinist used compressed air to blow coolant off the part. What coolant remained was on the parts from one to four days as the entire order was processed. Prior to inspection, parts were then washed with soap and water, rinsed with tap water and blown dry with compressed air.
Was the coolant aged? The coolant was in the machine for three months
(the coolant was changed and the machine cleaned after processing a tungsten job). It is a water based coolant manufactured by Hangsterfer called Neosol 400CF.
Could you have galling from a dull cutter? The job started with a new cutter and cutter was not replaced during the run. Set up pieces do not show signs of galling and areas adjacent to corrosion do not appear to have galling.
What is the aluminum content of the etch? I do not know the answer to that question. If I ask the special processor that cleaned the parts, will (should) they know the answer?
We are moving forward with a test of the following nature. We will machine sample coupons made from the same heat of 7075. Half the coupons will be cleaned immediately after machining. The other half will be left in coolant, left with coolant to dry, cleaned with soapy water, poorly rinsed and left to air dry. The special processor will do a typical clean and etch on all coupons, without knowledge of how the coupons were processed. We will then look at the results of the clean and etch and any corrosion that may appear.
I hope this additional information will be useful as you consider this problem.
Thanks to all for your helpful ideas and suggestions.
Best Regards,
- Longmont, Colorado, USA
Richard
If you are sending your product to a 'special process supplier', I would expect that they would have records to indicate what they did, for how long, who did it, etc.
The only time I can recall seeing corrosion product on aluminum (7xxx) during a cleaning operation was when we left the parts in a tap water rinse too long. The harder the water, the less time required to produce corrosion / pitting.
Your blind tests should provide some useful information. Hopefully, your processor is able to duplicate the initial corrosion problem. I would ask them to process the same as the first round rather than as typical, and document what they did. The first time around may not have been 'typical'.
Good luck.
- Colorado Springs, Colorado
October 23, 2008
Q, A, or Comment on THIS thread -or- Start a NEW Thread