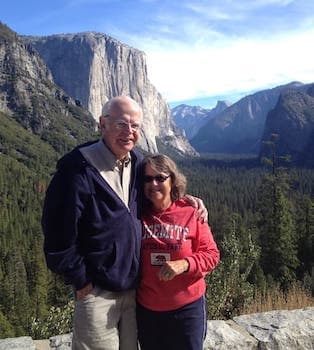
Curated with aloha by
Ted Mooney, P.E. RET
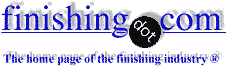
The authoritative public forum
for Metal Finishing 1989-2025
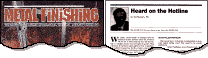
-----
Throw / Covering Power in Barrel Plating
October 7, 2008
Greetings:
I have a nickel sulphamate / acid cyanide gold plating application in which I am barrel plating connector components. In some cases the components are very small, with tiny, often very deep recessed holes.
My customer has a coverage requirement that calls for some amount of gold on all surfaces unless the diameter of the recess is .021" or less. It seems a rather arbitrary cut-off, and they don't say much about where it came from.
I immerse the parts in water with a surfactant and use a vacuum pretreatment to evacuate the air from the recess before plating, and this helps, but it's still hit or miss. Often parts with recess diameters of .03 or .04" and aspect ratios of 4 or 5 (depth/diameter) come out 50/50 covered/bare.
Is there an industry standard for this type of capability? Are there practices I can implement to improve my luck?
Thanks for the help!
-Ray
Plating Shop Engineer - New Hanover, PA USA
Increase the agitation directly under the barrel. You might point an eductor straight up at it.
James Watts- Navarre, Florida
October 9, 2008
The holes in your barrel may be slightly peened over. You might re-drill them to oven them up for better solution exchange in the barrel.
plating into recesses is normally done at low current density and barrel plating is a rather low effective current density.
You might look at raising your temperature a couple of degrees, but do not exceed normal limits for either solution.
I think that your recess limit is really pushing the envelope of possibilities for sulfamate nickel. EN and high micro throw copper will do much better.
- Navarre, Florida
October 10, 2008
Q, A, or Comment on THIS thread -or- Start a NEW Thread