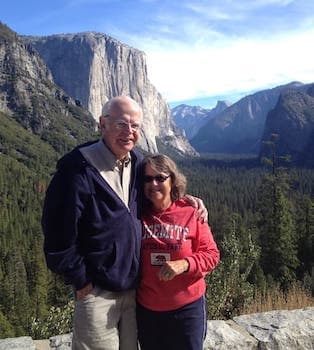
Curated with aloha by
Ted Mooney, P.E. RET
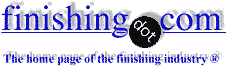
The authoritative public forum
for Metal Finishing 1989-2025
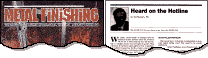
-----
Plating Specification for Solderable Copper Plated Aluminum Wire
September 30, 2008
Hi,
For a nuclear physics research project I need to have some custom aluminum-conductor cable constructed. The conductors (30AWG aluminum wire) should be copper-plated for solderability reasons, however we should keep the amount of plating material as low as possible. I need some advice what thickness to specify for the plating, in order that the wire will reliably be solderable (with tin/lead solder). The wire company will do 5-15 microinch nickel under the copper. Will copper
40-60 microinch be enough for solderability? I would hope not much more than that. If on the other hand this is way more than enough for solderability, I would appreciate to know that too. Your help is very much appreciated, thanks!
electronics engineer - Bloomington, Indiana, USA
A second thought. 30 AWG is really fine, why not go with copper wire to start with. You can find this commercially that has been tin plated. With the copper, you could go to an even smaller wire if load vs weight is a problem.
James Watts- Navarre, Florida
October 2, 2008
October 7, 2008
It is for a simple technical reason that we need to go with aluminum; the measurement we need to make in this experiment is contaminated by "secondary" particles generated in all the materials from which our detector is constructed, and the level of this contamination is more or less proportional to atomic number squared and proportional to the mass. In this way, aluminum generates far less contamination in our measurement than copper, for the same amount of current carried in the wires.
But for practical, reliable connections we want to solder these wires into standard connectors. Hence the need for a copper plated aluminum wire, and the question how thick should the copper plating be?
There is also "copper clad aluminum" (CCAW) available commercially
(usually it is used as a magnet wire for lightweight coils/transformers, I believe). However, it is 27% copper by weight, this is undesirable. We hope for something like 1/4 of that.
- Bloomington, IN, USA
December 19, 2008
I'd recommend going with an aluminum wire and mechanical connection, weld to copper, or, as the semiconductor industry does, an ultrasonic bond.
The IC folks use commercial ultrasonic vibrations to scrub oxides off Al prior to connection. Your EE department might have a specialized machine for this lying around. I wouldn't yank on these wires like ordinary lamp wire, but they're relatively mechanically strong. If the input and output wires are shock corded, you could put the bonded junction in a small box which would serve almost indefinitely without difficulty.
Would a Seebeck effect be bothersome? If so heat sink the junctions to maintain both junctions at the same temperature. Usually the Seebeck effect isn't a problem since IC makers ignore it and even linear ICs perform well without taking it into account.
They tried aluminum wiring in home construction, but had too many accidents due to poor training leading to poor cleaning of Al wires leading to fire. It's still used, but by power utilities who employ highly trained electricians to join Al wire.
- Bremerton, Washington, USA
Q, A, or Comment on THIS thread -or- Start a NEW Thread