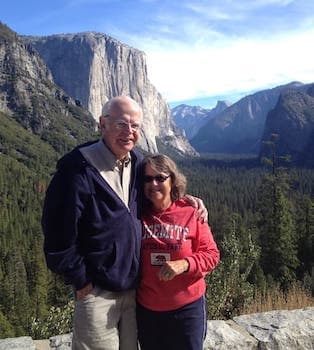
Curated with aloha by
Ted Mooney, P.E. RET
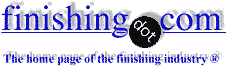
The authoritative public forum
for Metal Finishing 1989-2025
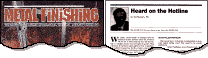
Thread 501/45
Rust Issue After Electro Chem Deburr
Hello folks. Hope someone may have some advice on our issue.
OK, we've recently installed an ECD machine to deburr cast iron machined parts. This is a totally new procedure for us, and we have no prior experience in this type of electro/chem process. The machine has an electrolyte consisting of Sodium Nitrate (NaNO3) in aqueous solution 1:1 to 1:15 SG (At least that is the original spec that we started with). The issue we are having is a certain amount of rust after deburring and washing. Our current process is deburr in the above solution, then place parts in an agitating dip tank containing a de-watering solution S5214 mixed with water @ 4% @ 40deg C for minimum of 1min. The parts are then washed in a Mecwash to remove the dip media, but are already rusty prior to this. It seems to mainly affect rough cast areas, rather than clean machined faces. We have also now tried a Sodium Chloride solution in the ECD machine with a specific gravity of 1.04 SG.
We cannot accept ANY amount of rust on these parts but we are primarily machinists and not chemistry orientated, so we have no experience/internal knowledge to fall back on with this process. The machine supplier has been a huge let down, and not been interested in supporting the issue other than a token level of interest.
I hope I've given useful data to enable some understanding of the process/issues, but please let me know if I have missed anything crucial.
Any help/suggestions gratefully received.
Thanks in advance.
production engineer - Birmingham, UK
September 29, 2008
publicly reply to John Loftus
I waited to see if someone might have the direct experience of the process and would reply. Here are my thoughts.
Cast iron is very prone to rusting when wet and particularly so after chemical treatment which will make it very active. The rough cast surfaces are more likely to retain process solution than the smoother areas.
Is the cast iron already rusted after the first rinse? If so I would speed-up the washing by vigorously agitating by hand rather than leaving the parts soaking. I don't know what S5214 is, but I would consider using plain cold water first rinse. Then transfer to a soap solution. NOT detergent but pure soap. You could buy sodium oleate or sodium stearate from a chemical supplier or use pure soap flakes from a supermarket. Then rinse again in water followed by a hot (~60c) rinse. I have found this to be an effective short term method of preventing rusting. Of course the system which you are using might be more effective than my proposed route.
If you can't avoid rusting then perhaps a separate de-rusting sequence might do to trick.
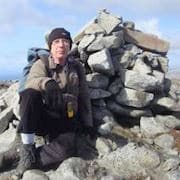
Harry Parkes
- Birmingham, UK
October 4, 2008
publicly reply to Harry Parkes
First of two simultaneous responses --
Have you considered using a straight dewatering oil such as a PX-24 or PX-10 type oil. This avoids the introduction of water after the ECD. You could leave the parts in the oiled state as this will offer protection against corrosion for a while. You can then use a suitable solvent to remove the oil when ready for further processing, e.g. a isoparaffinic hydrocarbon or one of the HFE or HFC family of solvents.
Brian TerryAerospace - Yeovil, Somerset, UK
publicly reply to Brian Terry
Second of two simultaneous responses -- October 8, 2008
Thanks Harry
We have gradually been trying to step through it, and we seem to be having some success with the secondary washing cycle. When we initially had the 2nd wash installed it came with the manufacturers
(Mecwash) own solution. But on investigation, we've found that after an initial period, the onsite contractors we use for all our industrial fluid control, had changed it for one of their own (Due to cost, surprise, surprise). We have just replaced with original fluid again, and are seeing some much better results. I will certainly keep your advice in mind, and appreciate the help. I'll update again when the current trial gives a definitive conclusion.
Thanks again.
- Birmingham, UK
publicly reply to John Loftus
Q, A, or Comment on THIS thread -or- Start a NEW Thread