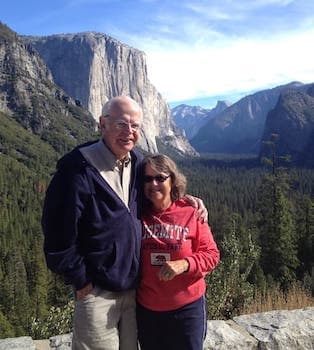
Curated with aloha by
Ted Mooney, P.E. RET
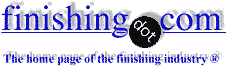
The authoritative public forum
for Metal Finishing 1989-2025
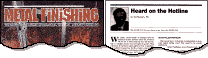
Thread 50/65
De Waxing of Parts after Electroplating
Q. My company are about to replace trichloroethylene vapour degreasing with an aqueous base process. The "Trike" is also used for final dewaxing of parts post electroplating. We have not found a satisfactory replacement process for dewaxing as yet. I would welcome comments on possible environmentally sound alternatives in use.
Mark Dunphy- Dublin, Ireland
2000
publicly reply to Mark Dunphy
A. Actually, perchloroethylene is slightly better for wax removal as it has a higher temperature, aiding in thermally removing wax (quicker). Perc is about as bad as trike, but since its vapor point is higher, it is easier for the coils to knock it down. You can reduce your solvent use considerably by putting a higher freeboard on the tank. eliminate cross drafts as much as possible.
Normally, simple walls can be cheaply installed and removed for maintenance as required and will cut use enough to pay for the addition in a month or so in many facilities. Use a slower hoist speed, both in and out. Allow for a longer drip time in the cold zone. Freeboard chiller coils are a mixed bag. some help but bad for the solution in areas of high humidity that will cause condensation of water into the tank. The excess wax can be removed from the top of the tank on a routine basis by shutting the tank down overnight and using a homemade holey long handled hoe.
For all of the claims made, nothing has replaced the efficient and economical use of a well designed and well operated vapor degreaser.
- Navarre, Florida
2000
publicly reply to James Watts
Q. Mike,
Have you made any progress in your search? Carol Eden (United Airlines) in San Francisco published an article in Plating and Surface Finishing magazine.
- Annapolis, Maryland
2000
publicly reply to Katherine Dougan
A. Dear Mark-
We at United Airlines Maintenance base have totally removed all degreasers from our shop. We no longer use them for cleaning or dewaxing on engines and aircraft. For cleaning, all our products are aqueous based. For dewaxing after plating, we use hot water (180-190 °F) to melt off the wax, which we recover, and then go into Bioact 280 (an aqueous cleaner/solvent), then rinse and into a cleaner and rinse again. This process has been in use for two years and we have the bugs worked out. Either Carol Eden (the author of the article the previous writer mentioned) or I (the process engineer) could give you more details if you need them.
- San Francisco, California
2000
publicly reply to Jeanne Kitazaki
Q. Jeanne Kitazaki,
I'm unsure of the date of this post so this is a shot in the dark. If possible, I would like to ask you about your hot water dewaxing and reclaiming process. We're currently using Bioact 280 with an oven as the initial dewaxing method. If you reply I will provide some contact information. Thank you.
- Nashua, New Hampshire
September 30, 2014
publicly reply to Emily Brown
Hi Emily. We've added the date to the posting so you can see that Jeanne's message was from 2000. Jeanne hasn't posted here for twelve years now, so I doubt that she'll see your message. But this site is about public discussions rather than private contact anyway, and hopefully others besides you two are employing this process by now and will want to engage in discussion. Good luck.
Regards,
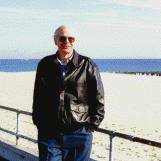
Ted Mooney, P.E.
Striving to live Aloha
finishing.com - Pine Beach, New Jersey
September 2014
publicly reply to Ted Mooney
Q, A, or Comment on THIS thread -or- Start a NEW Thread