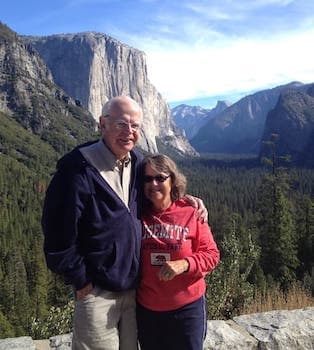
Curated with aloha by
Ted Mooney, P.E. RET
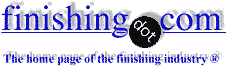
The authoritative public forum
for Metal Finishing 1989-2025
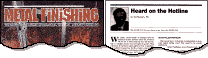
-----
Galvanic Reaction between Tin plated connectors and Aluminum wire
Q. I am trying to understand the galvanic reaction between tin plated aluminum body connectors used widely today and 8000 series aluminum conductors. Aluminum is more anodic than tin in the galvanic series. When used in a moist environment, would this not cause corrosion issues?
Alex MakEngineer - Vancouver, BC, Canada
September 1, 2008
A. Hi, Alex. Yes it would cause corrosion in a moist environment. Fortunately, aluminum tends to build stable corrosion products which helps minimize corrosion somewhat, tin and aluminum are reasonably close in the galvanic series, and the anodic surface area is large compared to the cathodic surface area, which spreads a limited galvanic current across a larger area. Cadmium was a good candidate for plating parts that would be in contact with aluminum, but it is a bioaccumulative poison and is avoided when possible.
Regards,
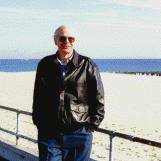
Ted Mooney, P.E.
Striving to live Aloha
finishing.com - Pine Beach, New Jersey
September 5, 2008
Q. Ted,
You kick butt! Based on my reading, I thought Tin and Copper was closer on the galvanic series in sea water than Aluminum. Is this the reason why there are some corrosion issues with aluminum conductors terminated in tin plated connectors close to the sea coast? Perhaps unplated aluminum connectors should be used instead?
What about the resistivity of the aluminum oxide film? Aluminum oxide is a great insulator, but the thickness of this film (50nm on average) should not pose much problems, correct? Otherwise, the oxide layer would've insulated the aluminum from the other metal and no galvanic corrosion can take place.
Thanks!
- Vancouver, BC
September 5, 2008
A. Thanks for the kind words. Unplated aluminum must not be used for connectors! An unplated aluminum terminal is almost guaranteed to offer a high resistance connection over time; this can cause heat and, unfortunately, fire.
Aluminum wiring can only be used under special circumstances where safety is not unreasonably compromised. Some years ago aluminum was widely used in house and commercial wiring, then the infamous Beverly Hills Supper Club fire was blamed on aluminum wiring and that was pretty much the end of it (google or you-tube it). Aluminum grows a high resistance surface skin, and can only be properly connected with special screw-type terminals that really dig through the skin and assure good contact, in concert with anti-oxidation compounds.
Copper wiring and terminals are generally preferred over aluminum because they do not have this high resistance film, but there are certainly cases like transmission lines where aluminum's lower weight, lower cost, and greater strength-to-weight ratio may make it the preferred choice. As for sea coast transmission lines, there may be codes or standards that require or suggest copper, but I am not in the transmission line industry and, sorry, I don't have knowledge of that. Good luck.
Regards,
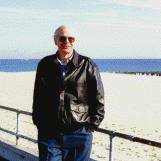
Ted Mooney, P.E.
Striving to live Aloha
finishing.com - Pine Beach, New Jersey
September 8, 2008
September 8, 2008
Hello Ted,
Thank you for the reply. I hold a tremendous amount of respect for your knowledge in this area, however, there are some information you may not be aware of when it comes to aluminum conductors. I was researching for reasons why tin plating is used when connecting aluminum connectors to aluminum conductors and there doesn't seem to be a qualified person out there that could answer this properly.
The issue with aluminum wiring back in the late sixties and early seventies was due to the use of copper devices with the aluminum wire. The two metals have different expansion rates and the subsequent on/off load cycles cause the loosening of the connection. In addition, the use of aluminum wire coupled directly with copper connectors also caused galvanic reaction and corroded the aluminum wire, thus giving aluminum wiring the term, non-corrosion resistant.
As you are well aware, aluminum is an extremely corrosion resistant material, much like stainless steel. The oxide film formed on its surface, just like stainless steel, provides this corrosion resistance. This oxide film is also stable between pH 4-8.5 aqueous solutions. And as you already know, this oxide film is self limiting and reaches a thickness no greater than 200nm. Otherwise, there would be no need to anodize aluminum to attain the 1 - 2 micron thickness of this oxide film.
The dielectric strength of this aluminum oxide approximately 16 kV/mm. As a result, the voltage required to breakdown this passivated layer is typically between 1-3 Volts (depending on the thickness formed). This is galvanic reaction can take place when aluminum is coupled with other metals such as copper. The difference in potential between the two metals is a meer 2 volts, and yet this potential is enough to drive the galvanic cell. A typical 120Volt system will punch the current right through this passivater oxide layer without any issues. That is why the NEC does not require oxide inhibitors when using aluminum conductors.
My biggest concern is the galvanic reaction between tin and aluminum. I suspect the industry may have inadvertently caused more harm than good when tin plating was introduced to couple aluminum connectors to aluminum conductors. Tin plating is a must when using dual rated aluminum connectors with copper conductors. But in humid coastal environments, this tin plating may be causing some corrosion issues with aluminum service entrance cables.
Thank you for your time and information on this subject. I work for Rio Tinto Alcan (formerly Aluminum Company of Canada), so I am quite familiar with aluminum's corrosion behavior.
- Vancouver, BC, Canada
A. Thanks for the very informative reply, Mak. I wish you the best in addressing any issues that are limiting the use of aluminum as a wiring material because it is obviously strong, light, highly conductive, and economical.
But the fact is, the discovery of aluminum wiring in a home is completely sufficient grounds for annulling a purchase contract (I was a home inspector for a couple of years); it cannot be repaired by changing plugs & switches to a different type of connection, but only by ripping out the walls and replacing it all with copper wire. But copper plated aluminum wiring does not cause the same problem. If you look at inexpensive anodized aluminum shower doors which are a few years old, you will see that corrosion is definitely not limited to nanometers or even a few microns; at the mitered corners which expose un-anodized aluminum at the saw lines, rather bulky corrosion products build up.
Cadmium is toxic and can be used only in limited applications, but it is the one plating that is truly galvanically compatible with aluminum; it is what aircraft fasteners were plated with for decades (although vapor deposited aluminum is widely used these days).
Thanks again, and Regards,
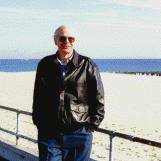
Ted Mooney, P.E.
Striving to live Aloha
finishing.com - Pine Beach, New Jersey
September 9, 2008
Tin plated or copper lugs for transfer welding machine terminals
December 24, 2017Q. Have a 225 amp welding machine that resided five miles from the Pacific Ocean for 25 years
inside a steel building.
The outlet connections are severely corroded.
The transformer conductors that attach to the outlet terminals are bare soft aluminum alloy.
The aluminum conductors are sandwiched between two since plated flange nuts.
The flange nuts are threaded to a hollow brass cylinder shape,
The welding leads with male connectors are pushed into the hollow threaded brass tube.
The machine configuration is all original.
Is a tinned plated copper lug crimped to a 1/0 stranded wire, sandwiched between two bare transformer conductors clamped with electroless zinc plated hardware, an acceptable upgrade.
Another option is to use a tin plated aluminum connector sandwiched between the two bare aluminum
conductors an acceptable option.
Tin plating the ends of the transformer leads is not an option.
- Delano, California, USA
A. Hi Roger. Zinc produces bulky, sticky, corrosion products; I don't think it should be used in electrical systems -- stick with tin plating.
As for the rest, a picture is worth a thousand words; sorry, I can't picture what you're describing. Maybe "since plated" was supposed to be "tin plated" or "zinc plated"? I'm also not sure that you are correct about "electroless zinc plated".
Regards,
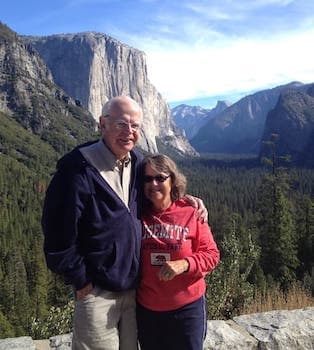
Ted Mooney, P.E. RET
Striving to live Aloha
finishing.com - Pine Beach, New Jersey
December 2017
Q, A, or Comment on THIS thread -or- Start a NEW Thread