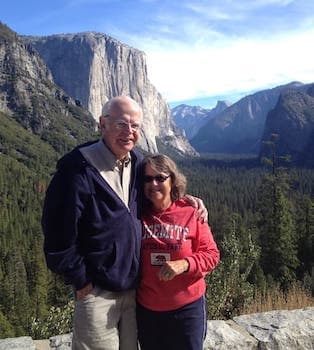
Curated with aloha by
Ted Mooney, P.E. RET
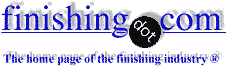
The authoritative public forum
for Metal Finishing 1989-2025
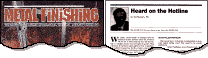
-----
A corrosion dilemma. PH stainless steel or Carbon {alloy} Steel+Coating ?
September 3, 2008
Hello. I am developing a firearm product that will need great corrosion resistance. I am requiring it to have a high level of hardness [heat treatable] and wear resistance.
The material will be stamped steel. It's thickness will be 1.0 -
1.5mm.
I have narrowed the steel down to a PH Stainless steel and carbon
{alloy}steel [with coating].
This material will not be a high stress part but it will encounter medium-high friction and excess abuse.
There are so many miraculous coating available today, I cannot figure out which material to choose [stainless or carbon
{alloy}steel].
Stainless would work with no coating, yet would be high in cost.
Carbon {alloy} would work great with the right coating, yet the heat treating might be tricky [depending on the coating].
I would like to know what the best, least expensive, method is for my application ?
Spend the extra money and use stainless. Never worry about coatings flaking, cracking or wearing.
Use a much cheaper steel and stay up at night wondering if the coating was applied correctly... and was the right one chosen.
?
I need some expert opinions here.
I will say that hard chrome would work great but I need near perfect dimensional accuracy. I also cannot afford possible cracking.
I am very open to suggestions. I want to finish my design with the correct steel.
Thank you very much.
Product designer / Gunsmith - Ringgold, GA, USA
High friction from what--It makes a big difference. I would talk to a specialty steel vendor and make the choice based on specs vs cost. I would go the specialty steel route possibly 17-4 PH or D-2 for extreme use.
James Watts- Navarre, Florida
September 5, 2008
The material [that I am deciding] will be in contact with 7075-T6 and 8620 HT steel.
The contact will be medium and intermittent.
It will likely never go above 200-300 degrees F.
The wear against the 8620 will be reciprocating. The catch is, it will not contact very much of the material. Also, it will not always be in contact. Very confusing, I know.
I believe a very good, thin, coating will work but I do not know how long it would last. Every company will "assure" me that it will... they want to sell their coating, so they are a little biased.
Stainless is the best bet but expensive and it work hardens [a good thing for the final product, not great for fabrication].
- Ringgold, GA, USA
September 5, 2008
Have you also considered electroless nickel? It is hard, adherent, lubricious, corrosion resistant and totally uniform in thickness for dimensional control. I personally would rank it above chrome for applications like yours. Many firearm OEM manufacturers offer it as one of their top coatings.
Guillermo MarrufoMonterrey, NL, Mexico
September 8, 2008
With the additional information, I would go with a 400 series SS. It machines very well in the annealed state and hardens quite well without a great dimensional change.
7xxx Al is not easy to hard coat, but good shops do a nice job.
My personal belief is that there is no such thing as teflon impregnated hard coat. A lot of people will talk about teflon impregnated anodize and I do not buy that claim either.
Chrome plate is an option, but it is not cheap.
Teflon impregnated Electroless Nickel would probably do very good for this application, but is not cheap either and not many job shops do it.
- Navarre, Florida
September 9, 2008
Have you considered solid lubricant coatings, such as diamond-like-carbon (DLC), molybdenum disulfide (MoS2), or tungsten disulfide (WS2)? All of these coatings are applied at low temperatures, so can be deposited on alloy steel. DLC coatings provide both high lubricity and high hardness. MoS2 would give you the lowest friction coefficient, and WS2 can take extremely high loads.
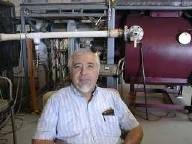
Jim Treglio - scwineryreview.com
PVD Consultant & Wine Lover
San Diego, California
September 11, 2008
Q, A, or Comment on THIS thread -or- Start a NEW Thread